Latest Experiment…Failure!
#227
Pineapple Racing sells a $2 mod to increase front oil pressure. With an rew rear oil pressure regulator a line loop is not needed.
Raising the pressure at the front bypass regulator with shims does not raise the pressure at the front stationary gear bearing.
All the oil goes from pump to front bypass to oil cooler to rear regulator to oil filter to rear stat gear bearing to upper dowels to front stat bearing. Rotor bearings and rotor cooling jets are fed by their respective stat gear bearings.
All the oil goes from pump to front bypass to oil cooler to rear regulator to oil filter to rear stat gear bearing to upper dowels to front stat bearing. Rotor bearings and rotor cooling jets are fed by their respective stat gear bearings.
First, Pineapple Racing does sell a couple of washers to shim the front pressure regulator for $2.95. I explained why raising "front oil pressure " will not raise oil pressure at the front stat gear bearing.
Second, a FD rear oil pressure regulator or an adjustable MFR rear regulator or a modification to another rear regulator will raise overall oil pressure. Without a loop line you still have pressure drop reducing oil pressure at the front stat gear bearing as compared to the rear. Race engines use a MFR rear regulator and a loop line.
There is pressure drop in the oil supply to the front stat gear bearing that feeds the front rotor bearing as it travels from the filter stand through ~19 inches of passages of varying volume and smoothness with three intersections of 90 deg where the passages are simply bored at right angles to each other.
The rear stat gear bearing enjoys a ~6 inch straight shot of smooth constant volume from the same oil filter stand.
That pressure drop is what a loop line addresses.
Hope I was clear this time

The following users liked this post:
ArmyOfOne (02-19-23)
#228
Banned. I got OWNED!!!
iTrader: (2)
when you say a 6" straight shot ... I'm trying to picture what exactly you're refering too. would you be able to provice a picture? I'm trying to absorb as much of this as possible but lack of engine rebuilds isn't helping.
Also about the copper nano particles, do you have a few sites to back up the statements ontop of your head (the increase in thermal conductivity that is)? I might be trying this out in the Formula SAE car that I help out on.
Also about the copper nano particles, do you have a few sites to back up the statements ontop of your head (the increase in thermal conductivity that is)? I might be trying this out in the Formula SAE car that I help out on.
#229
"Elusive, not deceptive!”

Thread Starter
There were a couple misconceptions I saw in the above quote and I addressed the first directly while answering the second by explaining the oil flow route to show how the loop line fits in.
To clarify my statements-
First, Pineapple Racing does sell a couple of washers to shim the front pressure regulator for $2.95. I explained why raising "front oil pressure " will not raise oil pressure at the front stat gear bearing.
Second, a FD rear oil pressure regulator or an adjustable MFR rear regulator or a modification to another rear regulator will raise overall oil pressure. Without a loop line you still have pressure drop reducing oil pressure at the front stat gear bearing as compared to the rear. Race engines use a MFR rear regulator and a loop line.
There is pressure drop in the oil supply to the front stat gear bearing that feeds the front rotor bearing as it travels from the filter stand through ~19 inches of passages of varying volume and smoothness with three intersections of 90 deg where the passages are simply bored at right angles to each other.
The rear stat gear bearing enjoys a ~6 inch straight shot of smooth constant volume from the same oil filter stand.
That pressure drop is what a loop line addresses.
Hope I was clear this time
To clarify my statements-
First, Pineapple Racing does sell a couple of washers to shim the front pressure regulator for $2.95. I explained why raising "front oil pressure " will not raise oil pressure at the front stat gear bearing.
Second, a FD rear oil pressure regulator or an adjustable MFR rear regulator or a modification to another rear regulator will raise overall oil pressure. Without a loop line you still have pressure drop reducing oil pressure at the front stat gear bearing as compared to the rear. Race engines use a MFR rear regulator and a loop line.
There is pressure drop in the oil supply to the front stat gear bearing that feeds the front rotor bearing as it travels from the filter stand through ~19 inches of passages of varying volume and smoothness with three intersections of 90 deg where the passages are simply bored at right angles to each other.
The rear stat gear bearing enjoys a ~6 inch straight shot of smooth constant volume from the same oil filter stand.
That pressure drop is what a loop line addresses.
Hope I was clear this time

As a side question, I wonder how many main bearing failures have been front vs. rear. I have had only one, a rear.
Barry
#230
Okay, okay now it's clear to me now. And I actually spoke with Rob at Pineapple racing today about the line loop feature. He said yes that the line loop will help and he has done it on his race motors in the past. He also said it's more of a long term durability mod.
I will give this some thought, may incorporate it into my motor. Thanks TII for your contribution to this thread.
I will give this some thought, may incorporate it into my motor. Thanks TII for your contribution to this thread.
#231
Thanks TII for your contribution to this thread.
12-29-08 07:31 PM
12-29-08 07:31 PM
As a side question, I wonder how many main bearing failures have been front vs. rear. I have had only one, a rear.
The loop line mod is to gain more oil pressure at the front stationary gear bearing, but only as a round about way of getting more oil pressure at the front ROTOR bearing as it is fed through the front stat gear.
I have had only one rotor bearing failure after I lost oil pressure (blown turbo oil feed line) and it was the front rotor bearing that seized- both main bearings were still perfect.
The race oil jet modification to the e-shaft also is to gain more oil pressure at the rotor bearings by using a SMALLER orifice than the stock check valved jet. This smaller orifice means higher pressure at the rotor bearing since it is a smaller oil leak.
The race oil jet just happens to be a larger leak at idle than the stock one as it doesn't have a check ball closing it off for faster warm up.
#232
"Elusive, not deceptive!”

Thread Starter
TII, getting back to the cooling of the housing in the sparkplug area.
I think Adam is doing a great job in addressing this, the number one problem with our rotary engines.
Do you have any additional thoughts on shrinking the growth of the sparkplug bosses besides using an alternate cooling fluid?
Barry
I think Adam is doing a great job in addressing this, the number one problem with our rotary engines.
Do you have any additional thoughts on shrinking the growth of the sparkplug bosses besides using an alternate cooling fluid?
Barry
#234
Old [Sch|F]ool

And in a region where you really don't need increased surface temps in a high boost application or sustained high rpm's.
Something to ponder - the coolant goes down the bottom of the engine, flows up, and then comes up through the top. Maybe the coolant coming through the top is HEATING the top of the engine and not cooling it. So, if you wanted to keep the intake ports cool, perhaps you'd want to avoid getting coolant in that area.
#237
"Elusive, not deceptive!”

Thread Starter
#238
"Elusive, not deceptive!”

Thread Starter
#239
No, I don't get the stain of blow by on my rotor housings.
I have used old rotor housings with cracked spark leading spark plug bosses, but haven't had one crack or spread in my motor.
I have certainly broken apex seals, though not the 3mm and 2mm Rotary Aviation seals I have used on the last several builds
It has been sideseals breaking with the rotary aviation seals.
I do tune for very low EGT under load with rich AFR.
I have used old rotor housings with cracked spark leading spark plug bosses, but haven't had one crack or spread in my motor.
I have certainly broken apex seals, though not the 3mm and 2mm Rotary Aviation seals I have used on the last several builds
It has been sideseals breaking with the rotary aviation seals.
I do tune for very low EGT under load with rich AFR.
#240
It's not really "blow by" by definition, blow by is oil getting into the combustion chamber (usually in excess). The stain we see is the apex seal "jumping" as it passes over the spark plug hole. Which is due to excessive heat in the plug boss area, causing it to "swell".
-J

-J
#241
So, has there ever been any actually before/after testing of the coolant passage mods as illustrated here and on Racing Beat and other web sites? Is this all theoretical?
It seems like it would help but I'm curious if there is data on it.
How does one come to decide that they should do this mod? Do you decide to do it based on the coolant temps you see or on some other basis?
Thanks for the education.
It seems like it would help but I'm curious if there is data on it.
How does one come to decide that they should do this mod? Do you decide to do it based on the coolant temps you see or on some other basis?
Thanks for the education.
#242
"Elusive, not deceptive!”

Thread Starter
So, has there ever been any actually before/after testing of the coolant passage mods as illustrated here and on Racing Beat and other web sites? Is this all theoretical?
It seems like it would help but I'm curious if there is data on it.
How does one come to decide that they should do this mod? Do you decide to do it based on the coolant temps you see or on some other basis?
Thanks for the education.
It seems like it would help but I'm curious if there is data on it.
How does one come to decide that they should do this mod? Do you decide to do it based on the coolant temps you see or on some other basis?
Thanks for the education.
Mazda embedded many temp probes within millimeters of the surface in their testing of housing temps. We don’t have that level of investigation. The best we can do is to observe teardown clues of what is happening. My next disassembly will be in about 5000 miles.
My/our problem might be solely related to high EGT’s. My engine peaks at 1000şC at 8000 RPM.
I added an idler to increase traction on the waterpump pulley. This may help.
I'm getting ready to compare water, 50/50 water/meth, and 100% meth for EGT readings.
Barry
#243
Now that you mention it, I could see Mazda doing that kind of R&D.
I do have some further questions on the topic of water jacket mods. I hope you guys don't mind me revisiting that even though it came up early in this thread.
Referring to Racing Beat photos of the water jacket mod here:
http://racingbeat.com/resultset.asp?partnumber=11488
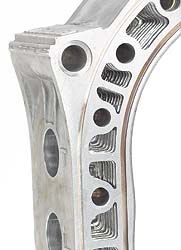
Rotorsports has a similar image on their site.
In the photo above, they etched grooves into the housings where the water flows through. I have heard people referring to this as adding "surface area" that would aid in cooling. Racing Beat's content says:
"This modification involves cutting grooves in the water jacket in the vicinity of the leading and trailing spark plugs to increase heat transfer out of the housing inner surface."
Now we know that area gets very hot and that this heat can potentially cause "localized boiling" of the coolant. However, thinking about it from a flow perspective, I wonder if this type of modification could itself cause "localized boiling". With the striations/grooves perpendicular to the flow of the coolant, I would think the grooves disturb the smooth flow of the coolant in a similar way as the water pump spinning beyond its effective range and causing cavitation.
When you run water perpendicularly over a ridged surface such as that, it starts to foam and splash. Wouldn't the same thing happen in your coolant passages and wouldn't that worsen the potential for hot spots and localized boiling?
Thanks.
I do have some further questions on the topic of water jacket mods. I hope you guys don't mind me revisiting that even though it came up early in this thread.
Referring to Racing Beat photos of the water jacket mod here:
http://racingbeat.com/resultset.asp?partnumber=11488
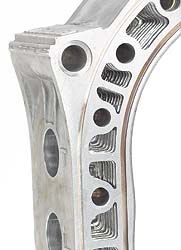
Rotorsports has a similar image on their site.
In the photo above, they etched grooves into the housings where the water flows through. I have heard people referring to this as adding "surface area" that would aid in cooling. Racing Beat's content says:
"This modification involves cutting grooves in the water jacket in the vicinity of the leading and trailing spark plugs to increase heat transfer out of the housing inner surface."
Now we know that area gets very hot and that this heat can potentially cause "localized boiling" of the coolant. However, thinking about it from a flow perspective, I wonder if this type of modification could itself cause "localized boiling". With the striations/grooves perpendicular to the flow of the coolant, I would think the grooves disturb the smooth flow of the coolant in a similar way as the water pump spinning beyond its effective range and causing cavitation.
When you run water perpendicularly over a ridged surface such as that, it starts to foam and splash. Wouldn't the same thing happen in your coolant passages and wouldn't that worsen the potential for hot spots and localized boiling?
Thanks.
#245
Now that you mention it, I could see Mazda doing that kind of R&D.
I do have some further questions on the topic of water jacket mods. I hope you guys don't mind me revisiting that even though it came up early in this thread.
Referring to Racing Beat photos of the water jacket mod here:
http://racingbeat.com/resultset.asp?partnumber=11488
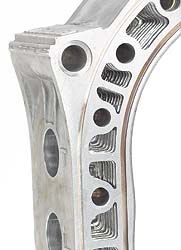
Rotorsports has a similar image on their site.
In the photo above, they etched grooves into the housings where the water flows through. I have heard people referring to this as adding "surface area" that would aid in cooling. Racing Beat's content says:
"This modification involves cutting grooves in the water jacket in the vicinity of the leading and trailing spark plugs to increase heat transfer out of the housing inner surface."
Now we know that area gets very hot and that this heat can potentially cause "localized boiling" of the coolant. However, thinking about it from a flow perspective, I wonder if this type of modification could itself cause "localized boiling". With the striations/grooves perpendicular to the flow of the coolant, I would think the grooves disturb the smooth flow of the coolant in a similar way as the water pump spinning beyond its effective range and causing cavitation.
When you run water perpendicularly over a ridged surface such as that, it starts to foam and splash. Wouldn't the same thing happen in your coolant passages and wouldn't that worsen the potential for hot spots and localized boiling?
Thanks.
I do have some further questions on the topic of water jacket mods. I hope you guys don't mind me revisiting that even though it came up early in this thread.
Referring to Racing Beat photos of the water jacket mod here:
http://racingbeat.com/resultset.asp?partnumber=11488
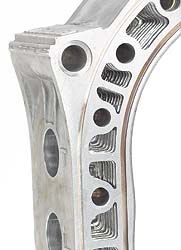
Rotorsports has a similar image on their site.
In the photo above, they etched grooves into the housings where the water flows through. I have heard people referring to this as adding "surface area" that would aid in cooling. Racing Beat's content says:
"This modification involves cutting grooves in the water jacket in the vicinity of the leading and trailing spark plugs to increase heat transfer out of the housing inner surface."
Now we know that area gets very hot and that this heat can potentially cause "localized boiling" of the coolant. However, thinking about it from a flow perspective, I wonder if this type of modification could itself cause "localized boiling". With the striations/grooves perpendicular to the flow of the coolant, I would think the grooves disturb the smooth flow of the coolant in a similar way as the water pump spinning beyond its effective range and causing cavitation.
When you run water perpendicularly over a ridged surface such as that, it starts to foam and splash. Wouldn't the same thing happen in your coolant passages and wouldn't that worsen the potential for hot spots and localized boiling?
Thanks.
Worth considering I suppose. Personally I'm a fan of 'relieving' that side of the housing by hacksawing between the through bolt area and the water seal groove, just as the MFR housings are. Not only does this increase surface area, it lets the housing deform under high load situations without being permanent. In my experience it reduces the high spot around the spark plug holes, as does running the coldest plug you can get away with.
#246
"Elusive, not deceptive!”

Thread Starter
Worth considering I suppose. Personally I'm a fan of 'relieving' that side of the housing by hacksawing between the through bolt area and the water seal groove, just as the MFR housings are. Not only does this increase surface area, it lets the housing deform under high load situations without being permanent. In my experience it reduces the high spot around the spark plug holes, as does running the coldest plug you can get away with.
Very interested. I am ready to try this next.
Gracer7, I only add the grooves in the area around the sparkplug at the housing side. The grooves add area and as PFD said , act like vortex generators disrupting boundary layer/smooth flow for better cooling.
Barry