No start on 85 12A
#1
Full Member
Thread Starter

I'm at wits end. I still can't get my rebuilt 12A to start. I've double checked the distributor pin alignment using TDC on the flywheel and timing marks. I have tried using the original ignition setup of only a trailing and leading coil. .. Fuel pump is supplying 4 psi and 1400cc/min to carb. I've pulled the Niki carb, open it up, and cleaned all the jets...I've shot ATF through the spark plug holes. Compression seem good, but I'd like to check it, but don't have a tester... any suggestions?
#2
Senior Member
You probably know all of these but just in case…. Things I learned starting my rebuild.
You can get a cheap $20 regular piston engine compression tester and do a quick and dirty test. Or if you have a OReillys or the like nearby they rent them for free. Here is how to use it on a rotary.
Have you checked fuel level in float bowls. Fuel
pressure is high, should be 2.5 psi. Wondering if the 4psi is blowing fuel past the needles and flooding the carb?
After repeated start attempts are you pulling and drying the plugs by passing them through a lighter flame, and cranking the engine whilst the plugs are out to blow out unburned fuel? (Don’t do what I did and leave a spark plug wire too near the plug hole when doing this. Results were interesting!)
Have you tried adding a couple of teaspoons of 2 stroke through the spark plug hole using a dropper prior to replacing plugs, then hand rotating the engine using ratchet on main pulley bolt to spread the oil around the rotor seals helping them seal for compression?
Have you pulled the plugs, reconnected them to their wires, laid them so you can see their ends then cranked the engine making sure you can see sparks at all four plugs?
Have you pulled the accelerator cable whilst looking down the carb barrel to make sure the accelerator pump is squirting gas into the barrels?
Do you know if your pulley is OEM and has the timing marks in the right place? Send pics of pulley if not sure.
Just some things I went through trying to get my rebuild started. Have faith and keep trying….. the moment it starts is a true glory!
You can get a cheap $20 regular piston engine compression tester and do a quick and dirty test. Or if you have a OReillys or the like nearby they rent them for free. Here is how to use it on a rotary.
Have you checked fuel level in float bowls. Fuel
pressure is high, should be 2.5 psi. Wondering if the 4psi is blowing fuel past the needles and flooding the carb?
After repeated start attempts are you pulling and drying the plugs by passing them through a lighter flame, and cranking the engine whilst the plugs are out to blow out unburned fuel? (Don’t do what I did and leave a spark plug wire too near the plug hole when doing this. Results were interesting!)
Have you tried adding a couple of teaspoons of 2 stroke through the spark plug hole using a dropper prior to replacing plugs, then hand rotating the engine using ratchet on main pulley bolt to spread the oil around the rotor seals helping them seal for compression?
Have you pulled the plugs, reconnected them to their wires, laid them so you can see their ends then cranked the engine making sure you can see sparks at all four plugs?
Have you pulled the accelerator cable whilst looking down the carb barrel to make sure the accelerator pump is squirting gas into the barrels?
Do you know if your pulley is OEM and has the timing marks in the right place? Send pics of pulley if not sure.
Just some things I went through trying to get my rebuild started. Have faith and keep trying….. the moment it starts is a true glory!
Last edited by Slow_sevens; 10-09-23 at 12:16 AM.
#3
just to add ....
while you're getting the compression tester, i would see if you can also get your hands on a timing light. if you were closer, i'd bring you mine.
the one time i had a lot of trouble starting a rebuilt 12A, it turned out to be the timing despite the fact that i was lining everything up correctly. the timing was way off. i happened across it by chance because, like you, i was at my wit's end and started moving the distributor a tooth at a time. that incident was the reason i bought my timing light.
at any rate, if you confirm that you're getting fuel and spark, check the timing with a light.
while you're getting the compression tester, i would see if you can also get your hands on a timing light. if you were closer, i'd bring you mine.
the one time i had a lot of trouble starting a rebuilt 12A, it turned out to be the timing despite the fact that i was lining everything up correctly. the timing was way off. i happened across it by chance because, like you, i was at my wit's end and started moving the distributor a tooth at a time. that incident was the reason i bought my timing light.

#4
Full Member
Thread Starter
Got the compression tester from OReillys, followed the video. The front rotor is putting out around 65 PSI on all three rotor rotation past the leading spark plug hole, suggesting good apex seals. The rear rotor is only putting out 65 PSI on on of the three rotations past the leading spark plug hole. On the other two rotations past the hole, I'm getting 0 psi. I guess I've got a bad apex seal on the rear rotator. Plenty of oil vapor expelled when the engine is cranked with the plugs removed.
I don't think the fuel pressure is the issue , Carb floats aren't over flowing, and the acceleration jets spray like hey are suppose to. The OEM pully timing marks were checked against TDC using the flat side of the flywheel looking through the access panel on pax side of engine. Distributor was also properly set and placed during the timing mark check.
Guess I'm going to have to get it rebuilt again. (Insert curse word here!) It was rebuilt two years age, waiting for the repairs to be done to the body of the car. The engine was pickled with oil in the rotors and hand spun on a regular basis to keep it lubed.
I don't think the fuel pressure is the issue , Carb floats aren't over flowing, and the acceleration jets spray like hey are suppose to. The OEM pully timing marks were checked against TDC using the flat side of the flywheel looking through the access panel on pax side of engine. Distributor was also properly set and placed during the timing mark check.
Guess I'm going to have to get it rebuilt again. (Insert curse word here!) It was rebuilt two years age, waiting for the repairs to be done to the body of the car. The engine was pickled with oil in the rotors and hand spun on a regular basis to keep it lubed.
#5
Senior Member
Well crap. Any chance you can film the gauge with your phone and post the result to Youtube so we can see it.
I believe you want to see over 80psi, any one else care to step in on that one? But the pressure reading is less important as varies significantly depending on cranking speed. More important is the 65 0 0 65 0 0 65 0 0 reading which is the death knell.
How much you paying for the rebuild? Is it so large a chunk that it would be worth blowing $300 on a dedicated rotary compression tester to prove beyond doubt that you need to rebuild? Maybe also seafoam or other magic fluid in the spark plug hole to see if the bad seal can be unstuck if it’s simply hung up?
And…. Maybe rebuild it yourself? It’s actually not that hard, and the reward when you drive the car at 7000rpm in an engine YOU built is a very special feeling. See if you can find a how to video so you can see what you are in for.
I believe you want to see over 80psi, any one else care to step in on that one? But the pressure reading is less important as varies significantly depending on cranking speed. More important is the 65 0 0 65 0 0 65 0 0 reading which is the death knell.
How much you paying for the rebuild? Is it so large a chunk that it would be worth blowing $300 on a dedicated rotary compression tester to prove beyond doubt that you need to rebuild? Maybe also seafoam or other magic fluid in the spark plug hole to see if the bad seal can be unstuck if it’s simply hung up?
And…. Maybe rebuild it yourself? It’s actually not that hard, and the reward when you drive the car at 7000rpm in an engine YOU built is a very special feeling. See if you can find a how to video so you can see what you are in for.
#7
Senior Member
The sound tells me something was maybe done wrong during the compression testing! Hear that
Pfft pfft pfft noose on yours? Sounds like escaping air. My test did not make that noise. See video.
Dumb question…. One spark plug removed for tester, other plug in it’s place and tightened? Tester nice and right? See if it makes that noise with both plugs in their place?
Or maybe you are testing correctly, but have a plug removed from the housing you are not testing, and that’s the noise we are hearing?
Pfft pfft pfft noose on yours? Sounds like escaping air. My test did not make that noise. See video.
Dumb question…. One spark plug removed for tester, other plug in it’s place and tightened? Tester nice and right? See if it makes that noise with both plugs in their place?
Or maybe you are testing correctly, but have a plug removed from the housing you are not testing, and that’s the noise we are hearing?
Last edited by Slow_sevens; 10-09-23 at 05:44 PM.
Trending Topics
#9
Senior Member
Good ideas. Try everything this side of exorcism before rebuilding.
#10
Full Member
Thread Starter
When doing the compression test, I removed both leading spark plugs, and left one open while the compression gauge was in the other, hence the background noise.
The person who rebuilt the engine has moved out of state, so no recourse there. Is it possible to do a partial teardown from the flywheel side to get to the rear rotor and replace just the bad seal?
The person who rebuilt the engine has moved out of state, so no recourse there. Is it possible to do a partial teardown from the flywheel side to get to the rear rotor and replace just the bad seal?
#11
When doing the compression test, I removed both leading spark plugs, and left one open while the compression gauge was in the other, hence the background noise.
The person who rebuilt the engine has moved out of state, so no recourse there. Is it possible to do a partial teardown from the flywheel side to get to the rear rotor and replace just the bad seal?
The person who rebuilt the engine has moved out of state, so no recourse there. Is it possible to do a partial teardown from the flywheel side to get to the rear rotor and replace just the bad seal?
#12
Full Member
Thread Starter
#13
Full Member
Thread Starter
Well, after two weeks of massaging, oiling, and moving the seals, there has been no change with the compression on the rear rotor. So I've pulled the engine and about to disassemble to replace the apex seals. Uggh!
#14
Senior Member
What you following for instructions? There are some tricks for cutting the side seals and getting the rotor back in. Maybe check in once the motor is apart and know if the housings are reusable.
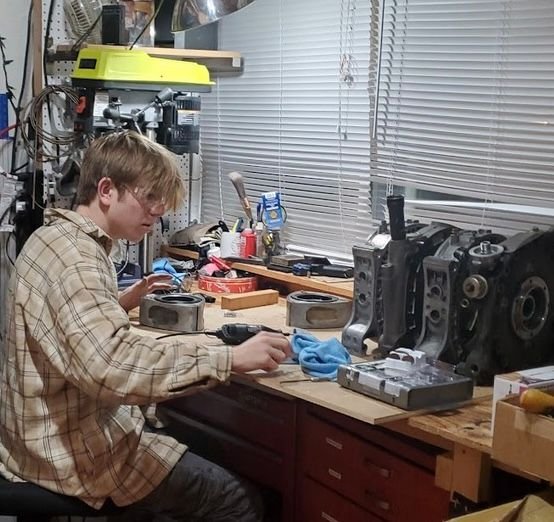
#17
Senior Member
Excuse the book-like length, but this is a random list of parts and things I learned when rebuilding my 12a. Sounds like you know what you are doing, so much may be already obvious to you. I sent this a few months ago to a friend rebuilding his, who was new to rotary. By no means comprehensive, and the grey beards here on the forum will have wise things to add... but does have some things I learned the hard way like not removing the main pulley bolt once engine is together, and those two flat washers behind the water pump that are NOT in the manual, but if not installed cause the darned thing to leak coolant everywhere.
Also have some things I learned when trying for first start. Let us know when you get there.
Good luck!
PARTS LIST Part numbers are Atkins Rotary.
- Rebuild kit from Atkins. I used 79-85 12A Rx7 Overhaul Kit C (ARE23)
In addition you should get:
- Belts. Air pump 1757-13-715. Alternator 8311-18-381A-9U-85. I dont have an AC so no third belt for me.
- Vaseline / petroleum jelly for some rubber seal interfaces and for keeping rotor seals in place.
- Water pump gaskets N2Y0-15-162 and N2Y0-15-116, plus two shims 1757-15-106-K. The shims are used on the two water pump housing bolts that do not pass through the gasket. Otherwise the pump housing twists and leaks. Found that one out the hard way.
- Box of random crush washers. I found a $20 box on Amazon. For oil lines etc.
- RTV Black gasket sealant. Get the one with the trigger as soooooo much easier to make the complicated shapes the legs of the housings require.
- Gasgacinch sealant for front cover gasket.
- Extra side seal kit ARE97. You WILL cut some of the side seals provided in the rebuild too short, so you WILL need an extra set.
- Throttle and choke cables if the originals are frayed or damaged. They get sticky very easily.
- Carb spacer Gasket 1480-13-220C. This spacer has a non-replaceable gasket so you have to buy the whole thing.
- Clutch HE11-16-460A and alignment tool EX-PT007. They are not expensive and you really dont want to have to mate the transmission to the engine more than once.
- Check all the original hoses. Particularly carefully check the hoses that pass right rear side of the engine near the manifold. They get cooked by the exhaust heat. Also check the hose that comes out of the rear of the water pump... its around 10cm long, has a bend cast into it and its ends are two different diameters. That part is no longer available, so you will need to make your own by choosing a diameter mid way between the two different end diameters and hose clamping it the best you can.
BUILD HINTS
- When the rebuild kit arrives, lay out, ID and bag all the parts. They will arrive as a loose box of random pieces so will take some detective work eg laying O rings in to their recesses on the irons to work out what goes where and best done before you start so you can compare very close items and work out which part is which.
- When taking the engine apart, take a picture using your phone of each part before you remove it, with a pencil pointing at the part so you remember which bit you are referring to. Then bag the part when removed, and write the time and date from the photo on the bag. Makes it sooooo much easier to rebuild as you can reverse the time line, and finding parts by day and time is soooo much easier than trying to remember what you meant by ' Silver thingy from the back of the bent rod'.
- Keep some of the old side and apex seals as they are good for cleaning out slots such as the water jacket seal grooves.
- When reassembling the oil pump, pack it with vaseline. I did not do this, and had no oil pressure on first start!
- Careful when pressing in the oil seals, they are REALLY sharp and I made a mess of my fingers.
- For shortening the side seals: 1. Rough cut the side seals slightly too long using a cut off wheel in a Dremel. 2. G-clamp the Dremel to your work bench, so the wheel is cut off wheel is vertical. 3. Clamp an approx 3/4 inch of plywood to the bench immediately next to the Dremel wheel. 4. Place an old side seal on the plywood resting on its edge and push its end up against the Dremel wheel, adjusting the angle of the seal so its chamfered end angle rests against the wheel. 5. Hold the side seal in place so it does not move and draw along the side with a pencil onto the plywood. The pencil line should be about the same length as the side seal, and have the same arc. 6. Take a rough cut side seal, align it with the pencil line on the plywood and push it against the running cut off wheel knowing the angle you are grinding down is correct. Grind of a little at a time, then test by slotting into the rotor and using a feeler gauge to check gap. Really tedious, but kinda satisfying at the same time!
- Dropping rotors into housing. This can be a pain if pieces keep falling out! Use three rubber bands per rotor to hold the apex seals in place. Wrap the bands around the rotor vertically (with rotor aligned as if it were the engine). Once band around the middle of the rotor, one band close to the bottom of the rotor, one band close to the top. Lower the rotor into the housing the first 1/2 inch of so then have someone cut the lowest rubber band. Lower to about half way in and cut the middle band. Then when almost all the way in cut the last band. Also use less Vaseline than you think you need when holding the corner seals in place, as too much turns from a glue to a lubricant.
- Once the engine is stacked up, but before you set end play etc... rotate the shaft by hand and make sure you can get more than a full 360 degree turn on the shaft. There should be a moderate amount of constant steady resistance... but should not require force or come to a hard stop. I dropped a corner seal during assembly which wedged in a port jamming a rotor. Glad I found this out during this test before I finished the build.
- Once you have the end play set and the main pulley bolt installed... do not remove the main pulley bolt unless the engine is orientated with the front cover upwards and you are careful to not move the main shaft, or (if in the car) the clutch pedal is held down. Otherwise the main shaft can slide causing the bearing shim to dislodge and the only way to fix it is to do the rebuild again.
- Run a compression test before reinstalling the engine. Crank the engine using the starter motor rigged to a battery. If you dont have a rotary compression tester, use a standard compression tester with none return valve removed. Film the needle of the tester with your phone on slo-mo as it crank then replay the video. You should see regular equally spaced pulses of pressure all around the same PSI, hopefully over 100 psi per pulse.
- Mating the engine to the transmission with the transmission already in the car is a total awful pain. I would do anything to avoid doing it again. I would strongly suggest mating the transmission to the engine before reinstalling in the car. If you do need to reinstall the engine after the transmission is in the car, use two chains on your engine hoist... one at the front of the engine and one at the rear and incorporate a turnbuckle into one of the chains so you can use it to adjust the angle the engine sits in the hoist and make mating to the transmission easier. You can also make guide studs by removing the heads from bolts with the same thread as those that tighten the bell housing to the motor, and cutting a slot in the cut end for later removal. Thread three of these studs in where the bell housing to motor bolts go, then use them as guides to align motor to bell housing. Once in place remove one guide at a time using a screwdriver and replace with the actual bolt.
-
Also have some things I learned when trying for first start. Let us know when you get there.
Good luck!
PARTS LIST Part numbers are Atkins Rotary.
- Rebuild kit from Atkins. I used 79-85 12A Rx7 Overhaul Kit C (ARE23)
In addition you should get:
- Belts. Air pump 1757-13-715. Alternator 8311-18-381A-9U-85. I dont have an AC so no third belt for me.
- Vaseline / petroleum jelly for some rubber seal interfaces and for keeping rotor seals in place.
- Water pump gaskets N2Y0-15-162 and N2Y0-15-116, plus two shims 1757-15-106-K. The shims are used on the two water pump housing bolts that do not pass through the gasket. Otherwise the pump housing twists and leaks. Found that one out the hard way.
- Box of random crush washers. I found a $20 box on Amazon. For oil lines etc.
- RTV Black gasket sealant. Get the one with the trigger as soooooo much easier to make the complicated shapes the legs of the housings require.
- Gasgacinch sealant for front cover gasket.
- Extra side seal kit ARE97. You WILL cut some of the side seals provided in the rebuild too short, so you WILL need an extra set.
- Throttle and choke cables if the originals are frayed or damaged. They get sticky very easily.
- Carb spacer Gasket 1480-13-220C. This spacer has a non-replaceable gasket so you have to buy the whole thing.
- Clutch HE11-16-460A and alignment tool EX-PT007. They are not expensive and you really dont want to have to mate the transmission to the engine more than once.
- Check all the original hoses. Particularly carefully check the hoses that pass right rear side of the engine near the manifold. They get cooked by the exhaust heat. Also check the hose that comes out of the rear of the water pump... its around 10cm long, has a bend cast into it and its ends are two different diameters. That part is no longer available, so you will need to make your own by choosing a diameter mid way between the two different end diameters and hose clamping it the best you can.
BUILD HINTS
- When the rebuild kit arrives, lay out, ID and bag all the parts. They will arrive as a loose box of random pieces so will take some detective work eg laying O rings in to their recesses on the irons to work out what goes where and best done before you start so you can compare very close items and work out which part is which.
- When taking the engine apart, take a picture using your phone of each part before you remove it, with a pencil pointing at the part so you remember which bit you are referring to. Then bag the part when removed, and write the time and date from the photo on the bag. Makes it sooooo much easier to rebuild as you can reverse the time line, and finding parts by day and time is soooo much easier than trying to remember what you meant by ' Silver thingy from the back of the bent rod'.
- Keep some of the old side and apex seals as they are good for cleaning out slots such as the water jacket seal grooves.
- When reassembling the oil pump, pack it with vaseline. I did not do this, and had no oil pressure on first start!
- Careful when pressing in the oil seals, they are REALLY sharp and I made a mess of my fingers.
- For shortening the side seals: 1. Rough cut the side seals slightly too long using a cut off wheel in a Dremel. 2. G-clamp the Dremel to your work bench, so the wheel is cut off wheel is vertical. 3. Clamp an approx 3/4 inch of plywood to the bench immediately next to the Dremel wheel. 4. Place an old side seal on the plywood resting on its edge and push its end up against the Dremel wheel, adjusting the angle of the seal so its chamfered end angle rests against the wheel. 5. Hold the side seal in place so it does not move and draw along the side with a pencil onto the plywood. The pencil line should be about the same length as the side seal, and have the same arc. 6. Take a rough cut side seal, align it with the pencil line on the plywood and push it against the running cut off wheel knowing the angle you are grinding down is correct. Grind of a little at a time, then test by slotting into the rotor and using a feeler gauge to check gap. Really tedious, but kinda satisfying at the same time!
- Dropping rotors into housing. This can be a pain if pieces keep falling out! Use three rubber bands per rotor to hold the apex seals in place. Wrap the bands around the rotor vertically (with rotor aligned as if it were the engine). Once band around the middle of the rotor, one band close to the bottom of the rotor, one band close to the top. Lower the rotor into the housing the first 1/2 inch of so then have someone cut the lowest rubber band. Lower to about half way in and cut the middle band. Then when almost all the way in cut the last band. Also use less Vaseline than you think you need when holding the corner seals in place, as too much turns from a glue to a lubricant.
- Once the engine is stacked up, but before you set end play etc... rotate the shaft by hand and make sure you can get more than a full 360 degree turn on the shaft. There should be a moderate amount of constant steady resistance... but should not require force or come to a hard stop. I dropped a corner seal during assembly which wedged in a port jamming a rotor. Glad I found this out during this test before I finished the build.
- Once you have the end play set and the main pulley bolt installed... do not remove the main pulley bolt unless the engine is orientated with the front cover upwards and you are careful to not move the main shaft, or (if in the car) the clutch pedal is held down. Otherwise the main shaft can slide causing the bearing shim to dislodge and the only way to fix it is to do the rebuild again.
- Run a compression test before reinstalling the engine. Crank the engine using the starter motor rigged to a battery. If you dont have a rotary compression tester, use a standard compression tester with none return valve removed. Film the needle of the tester with your phone on slo-mo as it crank then replay the video. You should see regular equally spaced pulses of pressure all around the same PSI, hopefully over 100 psi per pulse.
- Mating the engine to the transmission with the transmission already in the car is a total awful pain. I would do anything to avoid doing it again. I would strongly suggest mating the transmission to the engine before reinstalling in the car. If you do need to reinstall the engine after the transmission is in the car, use two chains on your engine hoist... one at the front of the engine and one at the rear and incorporate a turnbuckle into one of the chains so you can use it to adjust the angle the engine sits in the hoist and make mating to the transmission easier. You can also make guide studs by removing the heads from bolts with the same thread as those that tighten the bell housing to the motor, and cutting a slot in the cut end for later removal. Thread three of these studs in where the bell housing to motor bolts go, then use them as guides to align motor to bell housing. Once in place remove one guide at a time using a screwdriver and replace with the actual bolt.
-
The following 2 users liked this post by Slow_sevens:
diabolical1 (10-26-23),
Seniorchief (10-26-23)
Thread
Thread Starter
Forum
Replies
Last Post
gilmore03
1st Generation Specific (1979-1985)
5
11-04-05 05:59 PM