separating fiction from reality... a couple of days on the DYNO
#926
i have run the stock FD sensor relocated to the post IC tube... i have no idea as to other sensors... i do know the K will get it done and will be interested to see the temp immediately after the turbo at various boost levels, how it is effected by the pre turbo AI and how much help i get from the IC.
i did pick up the finished manifold this aft.
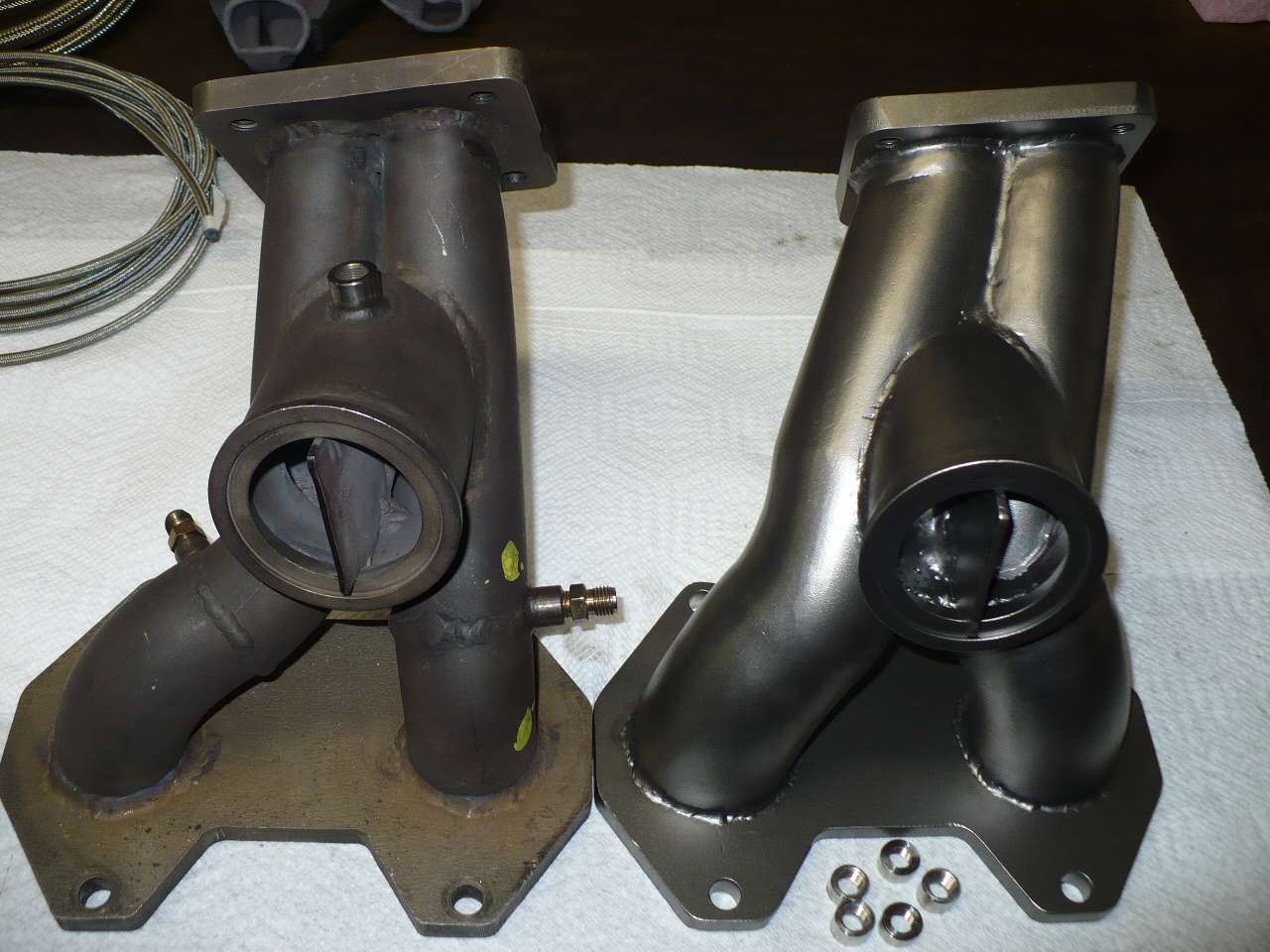
the newer manifold has 51% more inside runner area as well as having less bends. since it locates the often cherry red turbine housing within 3/8 inch of the front LIM runners a Mica heat shield is essential. zero heat penetrates Mica. the manifold enables a 9 inch by 7 inch K&N filter straight forward of the compressor making the preturbo injector a kill shot..
the final component will be a box for the filter so it draws essential outside air but that will have to wait a bit as we need to get rolling and we dyno, of course, w the hood open.
hc
i did pick up the finished manifold this aft.
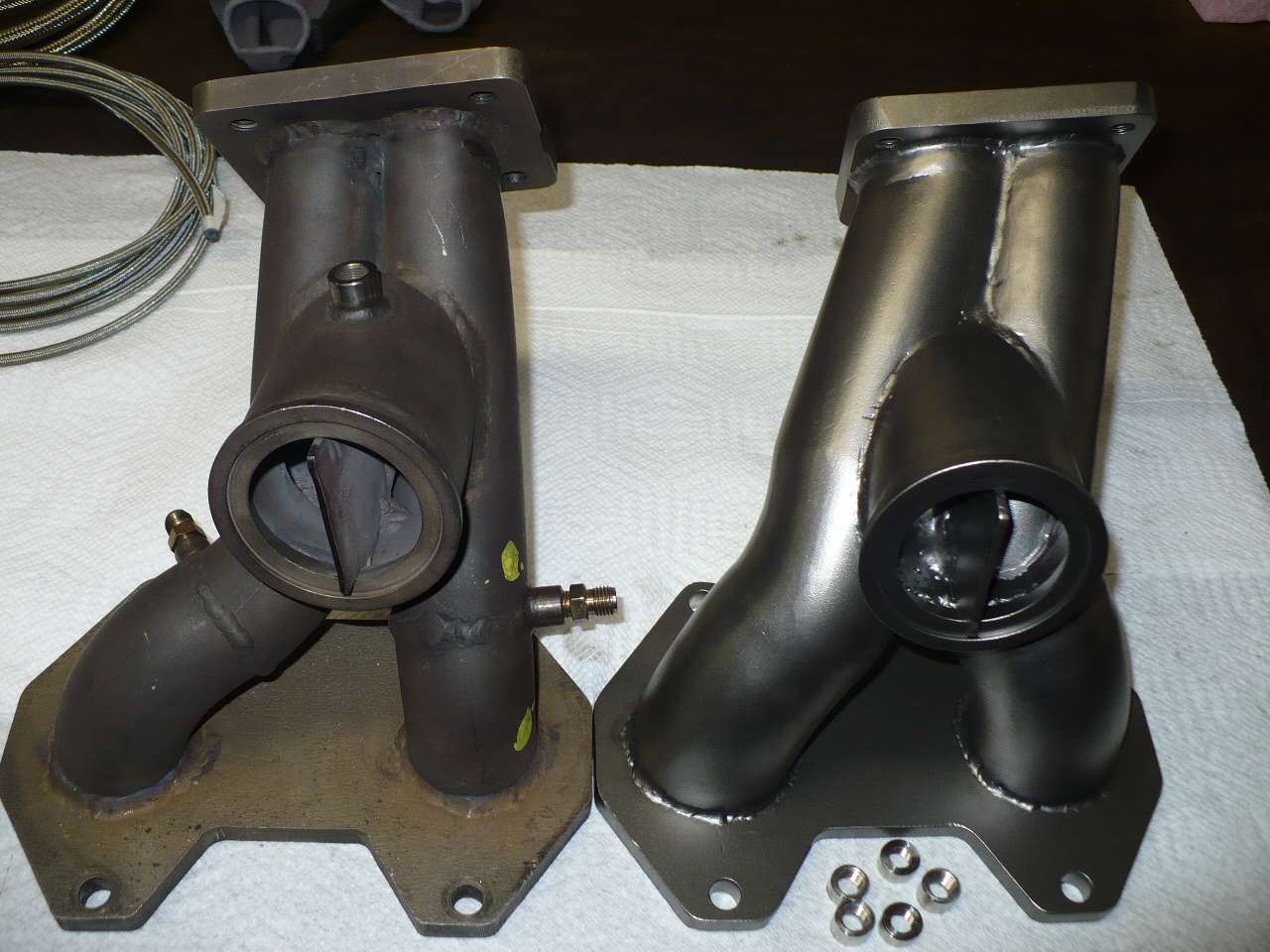
the newer manifold has 51% more inside runner area as well as having less bends. since it locates the often cherry red turbine housing within 3/8 inch of the front LIM runners a Mica heat shield is essential. zero heat penetrates Mica. the manifold enables a 9 inch by 7 inch K&N filter straight forward of the compressor making the preturbo injector a kill shot..
the final component will be a box for the filter so it draws essential outside air but that will have to wait a bit as we need to get rolling and we dyno, of course, w the hood open.
hc
What size runners were you using, and what size are you using on this new mainfold.
Another major difference between our setups is your v-mount intercoolersetup verses my Front my mount setup, and actual size of the intercoolers wher e mine is larger. Because of my front mount, longer pipes are used to make the loop. That in addition to a larger intercooler equates to a much larger volume for the turbo to fill with air, thus longer time needed to create pressue.
Your thoughts on this please.
#928
If you have a free flowing turbo back exhaust (3.5-4") it will likely boost creep....
here's the lowest boost we ran. i believe it was off the spring. i don't see significant boost creep.
Looks good! Your wastegate opened ~15psi and held under 17psi which as you said is normal behavior running off the spring.
Looks like my experience with 60mm wastegate on way undersized exhaust housing doesn't translate at all to a properly sized turbo like the ones you are running.
Looking forward to seeing more of your results and thanks for sharing your project and data.
here's the lowest boost we ran. i believe it was off the spring. i don't see significant boost creep.
Looks good! Your wastegate opened ~15psi and held under 17psi which as you said is normal behavior running off the spring.
Looks like my experience with 60mm wastegate on way undersized exhaust housing doesn't translate at all to a properly sized turbo like the ones you are running.
Looking forward to seeing more of your results and thanks for sharing your project and data.
#930
Racing Rotary Since 1983

Thread Starter
iTrader: (6)
"do you plan on doing more testing with the GT4094R"
absolutely. i own the GT4094 and it is the turbo that i plan to run at the Texas Mile. i think the 4094 is the least understood turbo in the Garrett product line. the GT4094 has 97.5% of the compressor area of the GT4294 yet it comes in a compact package. the GT42 must locate in front of the engine (meaning the turbine housing is forward of the front intake runner whereas my 4094 can situate almost in the engine longitudinal center.... making the runners shorter w less bends. i designed my manifold around the 4094.
if i could bolt the turbo to the motor i would... short straight runners are the primary design feature of my manifold. front mount turbos have an additional bend and longer runners.
caveat: i know mounting a larger turbo on any motor will make more power even if it is in front on the rotary... turbos are all about airflow and bigger is more flow. i don't need the bulky GT42 or the other 80 pound plus turbos for my setup. so, yes, you can post a pic of someone w a 700+ hp setup on a long runner front mount manifold, but that isn't my game. my game is efficiency and 600 max.
my design parameter is 600 hp max. i am not interested in anything beyond 600. given my target, the most efficient location, is alongside the motor.
by locating the turbo in the (stock) location i also fascilitate the use of a large air filter and the proper (straight) intake for pre turbo AI as well as a (to be designed) outside air box.
no outside air for your front mount turbo? you are sucking 160 F air into the motor.
"My 4094R 106 a/r does not hit 10 psi until 4500RPM"
i can assure you your boost lag has nothing to do w the 4094. the boost curve is significantly effected by many many factors. for instance, tune. most everyone, including myself, generally talks EGTs at their target boost. if you look at EGTs from zero boost to close to target you will find they often are around 1100. tune your EGT to 1400 and you will be looking at a different boost curve.
ports have a great deal of influence, specifically the exhaust... the stock FD exhaust port is huge, peripheral and has lots of duration. i early open the exhaust to transfer the modest remaining energy from the rear wheels to the turbine wheel. this helps midrange.
your 4094 should make 20 psi at 4500.
"What size runners were you using, and what size are you using on this new manifold."
manifolds are generally constructed from SS tubing (not recommended) or pipe. pipe is robust and the proper material for the task. pipe comes in two sizes...
1.68 i d which is 2.216 sq inches of area
2.067 i d which is 3.355 sq inches of area
the (round) FD exhaust port is 3.048 sq inches
i purposely constructed manifold one from the smaller pipe. smaller cross sectional area =s higher velocity. i beveled the half inch flange to make the transition. the bevel of course adds a resistance or drag.
my second manifold is constructed from the larger pipe. no bevel/drag of course. lower velocity.
since i log exhaust gas back pressure as well as front and rear EGTs we shall see. unfortunately it isn't quite apples/apples as there is less bend in manifold two.
"your v-mount intercoolersetup"
i run a SMIC,
intercooler chat tends to be a bit like apex seals or oil..... think sheepherders V cattle ranchers. strong opinions abound.
including me. i do agree that IC location does depend a bit on what you plan to do w your FD.
i am a road racer and front mounts don't work in this app. in addition to obscuring the coolant radiator FMIC really screw up weight distribution. my car has 53% rear weight and bolting a very heavy anything on the absolute front of the car doesn't work for me.
FMs probably work great for drag racing.
of course there is the additional volume of tubing but given the speed of the charge air it probably isn't much of a factor. i also am not sold on the V mount. i think a V overly clutters the already crowded engine compartment.
BTW, at 60 mph the airspeed thru a 3.5 inch IC is less than 7 mph. most of the heat transfer comes from radiation. the last time i checked, my SMIC was removing 130 F from my charge air.
i am very much in to flow. if you look at the pics of my setup you will see two intercoolers. Cam/Pettit supplied my ICs and each has a specific intake port location to keep tubing as short/straight as possible. IC one fits the 4094 and the GT3574/TD61 and IC two is for the BW. further, my BOV is not on the tube between the IC and elbow. as i have previously posted, i don't like a 2 inch hole in the 2.75 inch tube that supplies the motor.
back to your question... unless there is something plugged in your IC i doubt it is your spool problem.
"Howard's manifold is also very turbo flow oriented."
that is a correct assessment.
i designed it to favor turbo flow at the expense of the WG port.
helping WG flow, however, is a large WG and extremely favorable blend angle to the downpipe. the entire circuit needs to be considered when getting to the net.
while not fully evaluated, i like my data so far.
w only 26 dyno logs, probably 3/4 devoted to re-tuning drive-ability (new manifold, new AI setup etc)
the spring run (which was only around 1100 EGT F during spool)
average max boost EGT was 1457 F over approx 3000 rpm
average pre turbo exhaust back pressure was 28.9 psi at 15-17
in my view, if the WG was really bad the EGTs would have cumulated/trended higher w RPM. they were flat.
the 514 hp run
average EGT was 1499 F (and stable) not bad at 514 hp
average pre turbo exhaust back pressure was 27.48
on other subjects:
i am finishing my fuel lines today... the FFE rails need a few 120 degree fittings. (pics later).
the dash 3 AI lines are in along w the new larger filter.
the preturbo/airfilter assembly finishes this weekend.
i have almost finished building my four IGN-1A ignition coil mount and have found a great location.
i lucked out w the two Bosch RX8 knock sensors. it turns out that the stock FD harness has a bunch of connectors that will work as pigtails (from the solenoids in the rat's nest).
howard
absolutely. i own the GT4094 and it is the turbo that i plan to run at the Texas Mile. i think the 4094 is the least understood turbo in the Garrett product line. the GT4094 has 97.5% of the compressor area of the GT4294 yet it comes in a compact package. the GT42 must locate in front of the engine (meaning the turbine housing is forward of the front intake runner whereas my 4094 can situate almost in the engine longitudinal center.... making the runners shorter w less bends. i designed my manifold around the 4094.
if i could bolt the turbo to the motor i would... short straight runners are the primary design feature of my manifold. front mount turbos have an additional bend and longer runners.
caveat: i know mounting a larger turbo on any motor will make more power even if it is in front on the rotary... turbos are all about airflow and bigger is more flow. i don't need the bulky GT42 or the other 80 pound plus turbos for my setup. so, yes, you can post a pic of someone w a 700+ hp setup on a long runner front mount manifold, but that isn't my game. my game is efficiency and 600 max.
my design parameter is 600 hp max. i am not interested in anything beyond 600. given my target, the most efficient location, is alongside the motor.
by locating the turbo in the (stock) location i also fascilitate the use of a large air filter and the proper (straight) intake for pre turbo AI as well as a (to be designed) outside air box.
no outside air for your front mount turbo? you are sucking 160 F air into the motor.
"My 4094R 106 a/r does not hit 10 psi until 4500RPM"
i can assure you your boost lag has nothing to do w the 4094. the boost curve is significantly effected by many many factors. for instance, tune. most everyone, including myself, generally talks EGTs at their target boost. if you look at EGTs from zero boost to close to target you will find they often are around 1100. tune your EGT to 1400 and you will be looking at a different boost curve.
ports have a great deal of influence, specifically the exhaust... the stock FD exhaust port is huge, peripheral and has lots of duration. i early open the exhaust to transfer the modest remaining energy from the rear wheels to the turbine wheel. this helps midrange.
your 4094 should make 20 psi at 4500.
"What size runners were you using, and what size are you using on this new manifold."
manifolds are generally constructed from SS tubing (not recommended) or pipe. pipe is robust and the proper material for the task. pipe comes in two sizes...
1.68 i d which is 2.216 sq inches of area
2.067 i d which is 3.355 sq inches of area
the (round) FD exhaust port is 3.048 sq inches
i purposely constructed manifold one from the smaller pipe. smaller cross sectional area =s higher velocity. i beveled the half inch flange to make the transition. the bevel of course adds a resistance or drag.
my second manifold is constructed from the larger pipe. no bevel/drag of course. lower velocity.
since i log exhaust gas back pressure as well as front and rear EGTs we shall see. unfortunately it isn't quite apples/apples as there is less bend in manifold two.
"your v-mount intercoolersetup"
i run a SMIC,
intercooler chat tends to be a bit like apex seals or oil..... think sheepherders V cattle ranchers. strong opinions abound.
including me. i do agree that IC location does depend a bit on what you plan to do w your FD.
i am a road racer and front mounts don't work in this app. in addition to obscuring the coolant radiator FMIC really screw up weight distribution. my car has 53% rear weight and bolting a very heavy anything on the absolute front of the car doesn't work for me.
FMs probably work great for drag racing.
of course there is the additional volume of tubing but given the speed of the charge air it probably isn't much of a factor. i also am not sold on the V mount. i think a V overly clutters the already crowded engine compartment.
BTW, at 60 mph the airspeed thru a 3.5 inch IC is less than 7 mph. most of the heat transfer comes from radiation. the last time i checked, my SMIC was removing 130 F from my charge air.
i am very much in to flow. if you look at the pics of my setup you will see two intercoolers. Cam/Pettit supplied my ICs and each has a specific intake port location to keep tubing as short/straight as possible. IC one fits the 4094 and the GT3574/TD61 and IC two is for the BW. further, my BOV is not on the tube between the IC and elbow. as i have previously posted, i don't like a 2 inch hole in the 2.75 inch tube that supplies the motor.
back to your question... unless there is something plugged in your IC i doubt it is your spool problem.
"Howard's manifold is also very turbo flow oriented."
that is a correct assessment.
i designed it to favor turbo flow at the expense of the WG port.
helping WG flow, however, is a large WG and extremely favorable blend angle to the downpipe. the entire circuit needs to be considered when getting to the net.
while not fully evaluated, i like my data so far.
w only 26 dyno logs, probably 3/4 devoted to re-tuning drive-ability (new manifold, new AI setup etc)
the spring run (which was only around 1100 EGT F during spool)
average max boost EGT was 1457 F over approx 3000 rpm
average pre turbo exhaust back pressure was 28.9 psi at 15-17
in my view, if the WG was really bad the EGTs would have cumulated/trended higher w RPM. they were flat.
the 514 hp run
average EGT was 1499 F (and stable) not bad at 514 hp

average pre turbo exhaust back pressure was 27.48
on other subjects:
i am finishing my fuel lines today... the FFE rails need a few 120 degree fittings. (pics later).
the dash 3 AI lines are in along w the new larger filter.
the preturbo/airfilter assembly finishes this weekend.
i have almost finished building my four IGN-1A ignition coil mount and have found a great location.
i lucked out w the two Bosch RX8 knock sensors. it turns out that the stock FD harness has a bunch of connectors that will work as pigtails (from the solenoids in the rat's nest).
howard
#931
Speaking as someone who has built I don't even know how many manifolds out of "tubing" and prefer to, I can tell you tubing is not a issue. I use .120 wall tubing which is the same thickness essentially as schedule 10 pipe. It allows for better diameter selection as well as bend selection and less welds required. The fewer welds you have the more stable and stronger the overall piece will be practically every time.
~S~
#932
Racing Rotary Since 1983

Thread Starter
iTrader: (6)
Hi Sean,
i completely agree w you re thick wall tubing... i was referring to the thinner stuff which often has cracking issues and should have stated it as such...
hc
i completely agree w you re thick wall tubing... i was referring to the thinner stuff which often has cracking issues and should have stated it as such...
hc
#934
poor wastegate flow will still hurt power, even though it may avoid boost creep. i bet emap will be abnormally high after wastegate opens. would you put an 180 deg kink in your exhaust pipe?
Yeah, but a nice wastegate lead in that promotes WG flow like I did will disturb smooth flow to the turbo where most his exhaust is going with these larger turbos.
Its a balance.
I have been thinking about this a LOOOONG time and the key would be to find a shape that flows well to the turbo and wastegate with minimal drag/drop in velocity.
The idea I came up with is a 60mm diameter pipe straight off the exhaust port about 4" long with a 60mm WG on the end for each exhaust runner.
Wastegate flow covered.
Another smaller 45 deg bend pipe ~40mm diameter starts INSIDE the 60mm WG pipe about 30mm from the port and exits out the top of the WG pipe to the turbo flange.
With wastegate closed the exhaust sees a 60-40mm velocity stack as the turbulence around the lip of the 40mm turbo runner pipe protrusion will stack up at the junction of the two pipes.
With wastegate open the exhaust will have a reasonable area of flow straight to the WG.
I haven't put anything together and flow benched it yet to prove my idea.
Yeah, but a nice wastegate lead in that promotes WG flow like I did will disturb smooth flow to the turbo where most his exhaust is going with these larger turbos.
Its a balance.
I have been thinking about this a LOOOONG time and the key would be to find a shape that flows well to the turbo and wastegate with minimal drag/drop in velocity.
The idea I came up with is a 60mm diameter pipe straight off the exhaust port about 4" long with a 60mm WG on the end for each exhaust runner.
Wastegate flow covered.
Another smaller 45 deg bend pipe ~40mm diameter starts INSIDE the 60mm WG pipe about 30mm from the port and exits out the top of the WG pipe to the turbo flange.
With wastegate closed the exhaust sees a 60-40mm velocity stack as the turbulence around the lip of the 40mm turbo runner pipe protrusion will stack up at the junction of the two pipes.
With wastegate open the exhaust will have a reasonable area of flow straight to the WG.
I haven't put anything together and flow benched it yet to prove my idea.
#938
Banned. I got OWNED!!!

[QUOTE=BLUE TII;11132412][I]
I have been thinking about this a LOOOONG time and the key would be to find a shape that flows well to the turbo and wastegate with minimal drag/drop in velocity.
The idea I came up with is a 60mm diameter pipe straight off the exhaust port about 4" long with a 60mm WG on the end for each exhaust runner.
Wastegate flow covered.
Another smaller 45 deg bend pipe ~40mm diameter starts INSIDE the 60mm WG pipe about 30mm from the port and exits out the top of the WG pipe to the turbo flange.
QUOTE]
I believe he means something like this.... Although the runner going up to the turbo does not stick down into the larger WG runner, it simply breaks off smoothly.
http://www.flickr.com/photos/74953263@N07/6924833633/http://www.flickr.com/photos/74953263@N07/6924833633/ by http://www.flickr.com/people/74953263@N07/, on Flickr
The problem with this is once the gates open, you still have an entire runners length of exhaust which has already passed (the gate), and still reaches the turbo, causing a spike. How moderate or severe of a spike is dependant on the conditions/setup, but the bottom line is that a gate placed near the motor is not an ideal location if you want to best use it for its intended purpose.
I have been thinking about this a LOOOONG time and the key would be to find a shape that flows well to the turbo and wastegate with minimal drag/drop in velocity.
The idea I came up with is a 60mm diameter pipe straight off the exhaust port about 4" long with a 60mm WG on the end for each exhaust runner.
Wastegate flow covered.
Another smaller 45 deg bend pipe ~40mm diameter starts INSIDE the 60mm WG pipe about 30mm from the port and exits out the top of the WG pipe to the turbo flange.
QUOTE]
I believe he means something like this.... Although the runner going up to the turbo does not stick down into the larger WG runner, it simply breaks off smoothly.
http://www.flickr.com/photos/74953263@N07/6924833633/http://www.flickr.com/photos/74953263@N07/6924833633/ by http://www.flickr.com/people/74953263@N07/, on Flickr
The problem with this is once the gates open, you still have an entire runners length of exhaust which has already passed (the gate), and still reaches the turbo, causing a spike. How moderate or severe of a spike is dependant on the conditions/setup, but the bottom line is that a gate placed near the motor is not an ideal location if you want to best use it for its intended purpose.
#942
SENZA PARI, the manifold design you pictured is something I had thought of as well, but the flow path to the turbo intuitively seemed a bit tortured for my liking.
However, airflow as proven on a flowbench is often far from intuitive.
Question, were poppet style wastegates employed on that manifold or swing valve?
Poppet valve facing exhaust port just seems like it would cause pressure wave reversion on a rotary open or closed.
That said, I am worried about the Turbonetics 60mm swing valves wastegates as they don't have the best reputation for reliability on rotaries.
However, airflow as proven on a flowbench is often far from intuitive.
Question, were poppet style wastegates employed on that manifold or swing valve?
Poppet valve facing exhaust port just seems like it would cause pressure wave reversion on a rotary open or closed.
That said, I am worried about the Turbonetics 60mm swing valves wastegates as they don't have the best reputation for reliability on rotaries.
#943
"Elusive, not deceptive!”

Howard's design includes some good ideas.
A couple of things to consider when designing manifolds.
1- From Allison Turbine manuals...."blades are driven by impact and reaction of the gasses".
In other words the turbine blades are driven not just by flow and pressure, but also in our case, by the pulse of the port opening.
The straighter the pipe the better. Ideally the turbine blades should "see" the port opening!
2- We should also keep in mind that it is called a "waste gate". Unless we want to add a power recovery turbine to the manifold.... we are just bleeding off gasses. Don't make this the priority for flow.
My thoughts,
Barry
A couple of things to consider when designing manifolds.
1- From Allison Turbine manuals...."blades are driven by impact and reaction of the gasses".
In other words the turbine blades are driven not just by flow and pressure, but also in our case, by the pulse of the port opening.
The straighter the pipe the better. Ideally the turbine blades should "see" the port opening!
2- We should also keep in mind that it is called a "waste gate". Unless we want to add a power recovery turbine to the manifold.... we are just bleeding off gasses. Don't make this the priority for flow.
My thoughts,
Barry
#944
Howard's design includes some good ideas.
A couple of things to consider when designing manifolds.
1- From Allison Turbine manuals...."blades are driven by impact and reaction of the gasses".
In other words the turbine blades are driven not just by flow and pressure, but also in our case, by the pulse of the port opening.
The straighter the pipe the better. Ideally the turbine blades should "see" the port opening!
2- We should also keep in mind that it is called a "waste gate". Unless we want to add a power recovery turbine to the manifold.... we are just bleeding off gasses. Don't make this the priority for flow.
My thoughts,
Barry
A couple of things to consider when designing manifolds.
1- From Allison Turbine manuals...."blades are driven by impact and reaction of the gasses".
In other words the turbine blades are driven not just by flow and pressure, but also in our case, by the pulse of the port opening.
The straighter the pipe the better. Ideally the turbine blades should "see" the port opening!
2- We should also keep in mind that it is called a "waste gate". Unless we want to add a power recovery turbine to the manifold.... we are just bleeding off gasses. Don't make this the priority for flow.
My thoughts,
Barry
#945
Arrogant Wankeler

Any additional pressure in exhaust manifold will result in greater mass flow and energy to the turbine, which means more boost & a change in operating conditions, A wastegate is nothing more that a restricted manifold leak that is closed loop controlled. Provided the gate runners do not provide so much restriction at to not allow enough bypass to hold your maximum acceptable boost at peak flow, the gate will simply present a restriction, that in combination with the wastegate flow path of the manifold, delivers the required mass/energy to the turbine for the target boost.
People are putting way to much effort into wastegate flow setup, you want the best flow path to the turbine #1 as any restriction/energy loss to the turbine does mean more exhaust manifold pressure (and exhaust stroke pumping power loss & heat retention due to higher density gas delivering more to the manifold etc - so less power from the same air and more heat to deal with for same rwhp) as you need to deliver a certain energy to your compressor for your target intake pressure at whatever load condition. All you need so far as wastegating is a combined restriction to dump/atmosphere over which you have enough control to maintain for target intake density.
I have no doubt that there are people getting around making less power than they could, with higher boost threshold and worse transient response with more engine system/manifold degradation with whatever turbo they have because they have focussed on "letting the wastegate breathe".
#946
Senior Member

Join Date: Nov 2008
Location: Czech republic
Posts: 357
Likes: 0
Received 0 Likes
on
0 Posts
Howard's design includes some good ideas.
A couple of things to consider when designing manifolds.
1- From Allison Turbine manuals...."blades are driven by impact and reaction of the gasses".
In other words the turbine blades are driven not just by flow and pressure, but also in our case, by the pulse of the port opening.
The straighter the pipe the better. Ideally the turbine blades should "see" the port opening!
2- We should also keep in mind that it is called a "waste gate". Unless we want to add a power recovery turbine to the manifold.... we are just bleeding off gasses. Don't make this the priority for flow.
My thoughts,
Barry
A couple of things to consider when designing manifolds.
1- From Allison Turbine manuals...."blades are driven by impact and reaction of the gasses".
In other words the turbine blades are driven not just by flow and pressure, but also in our case, by the pulse of the port opening.
The straighter the pipe the better. Ideally the turbine blades should "see" the port opening!
2- We should also keep in mind that it is called a "waste gate". Unless we want to add a power recovery turbine to the manifold.... we are just bleeding off gasses. Don't make this the priority for flow.
My thoughts,
Barry
Just to be 100% clear, assuming same engine operating parameters and same exhaust restriction post turbine/gate, with no convolutions added to manifold path to the turbine (at that would lift EMBP for same inlet pressure condition) that statement is absolutely wrong.
Any additional pressure in exhaust manifold will result in greater mass flow and energy to the turbine, which means more boost & a change in operating conditions, A wastegate is nothing more that a restricted manifold leak that is closed loop controlled. Provided the gate runners do not provide so much restriction at to not allow enough bypass to hold your maximum acceptable boost at peak flow, the gate will simply present a restriction, that in combination with the wastegate flow path of the manifold, delivers the required mass/energy to the turbine for the target boost.
People are putting way to much effort into wastegate flow setup, you want the best flow path to the turbine #1 as any restriction/energy loss to the turbine does mean more exhaust manifold pressure (and exhaust stroke pumping power loss & heat retention due to higher density gas delivering more to the manifold etc - so less power from the same air and more heat to deal with for same rwhp) as you need to deliver a certain energy to your compressor for your target intake pressure at whatever load condition. All you need so far as wastegating is a combined restriction to dump/atmosphere over which you have enough control to maintain for target intake density.
I have no doubt that there are people getting around making less power than they could, with higher boost threshold and worse transient response with more engine system/manifold degradation with whatever turbo they have because they have focussed on "letting the wastegate breathe".
Any additional pressure in exhaust manifold will result in greater mass flow and energy to the turbine, which means more boost & a change in operating conditions, A wastegate is nothing more that a restricted manifold leak that is closed loop controlled. Provided the gate runners do not provide so much restriction at to not allow enough bypass to hold your maximum acceptable boost at peak flow, the gate will simply present a restriction, that in combination with the wastegate flow path of the manifold, delivers the required mass/energy to the turbine for the target boost.
People are putting way to much effort into wastegate flow setup, you want the best flow path to the turbine #1 as any restriction/energy loss to the turbine does mean more exhaust manifold pressure (and exhaust stroke pumping power loss & heat retention due to higher density gas delivering more to the manifold etc - so less power from the same air and more heat to deal with for same rwhp) as you need to deliver a certain energy to your compressor for your target intake pressure at whatever load condition. All you need so far as wastegating is a combined restriction to dump/atmosphere over which you have enough control to maintain for target intake density.
I have no doubt that there are people getting around making less power than they could, with higher boost threshold and worse transient response with more engine system/manifold degradation with whatever turbo they have because they have focussed on "letting the wastegate breathe".
I feel stupid that I don't have much to add, but these posts sums it up.
Compressor needs certain power for given airflow and pressure ratio and this power is extracted from heat, pressure differential and mass flow of exhaust gases through the turbine. But there is also that strong pulse effect. Main part of whole exhaust mass flow is concentrated in blowdown phase of exhaust stroke and for best transient response, lowest boost threshold and lowest backpressure with other parameters held equal, its vital to have turbine flow as #1 priority without any disruption to flow.
Its really simple, turbine needs certain energy and manifold should deliver it most efficiently. Heat losses, pressure losses and loss of pulsing effect must be made up by increase in pressure as mass flow is kept constant.
Whats even better, turbine preferred manifold will support larger hotsides without any loss of response for even lower backpressure and EGT's. Its been already reported by Turblown, that quite big hotsides on properly designed manifolds have lower boost threshold even though they "should" need more mass flow to deliver same energy. IMO its clear indication that larger hotsides work with higher efficiency. Some people say that its due to leverage effect, I believe that it lies in certain parameter concerning blade tip speed and velocity of gas entering the turbine.
Perfect example are F1 turbo engines. They were extracting quite big portion of energy to power compressors to very high pressure ratios and flow levels, yet they had lower exhaust pressure than intake pressure and wastegate runners seems to be positioned at about 90 degrees from collector on all setups, no magic there

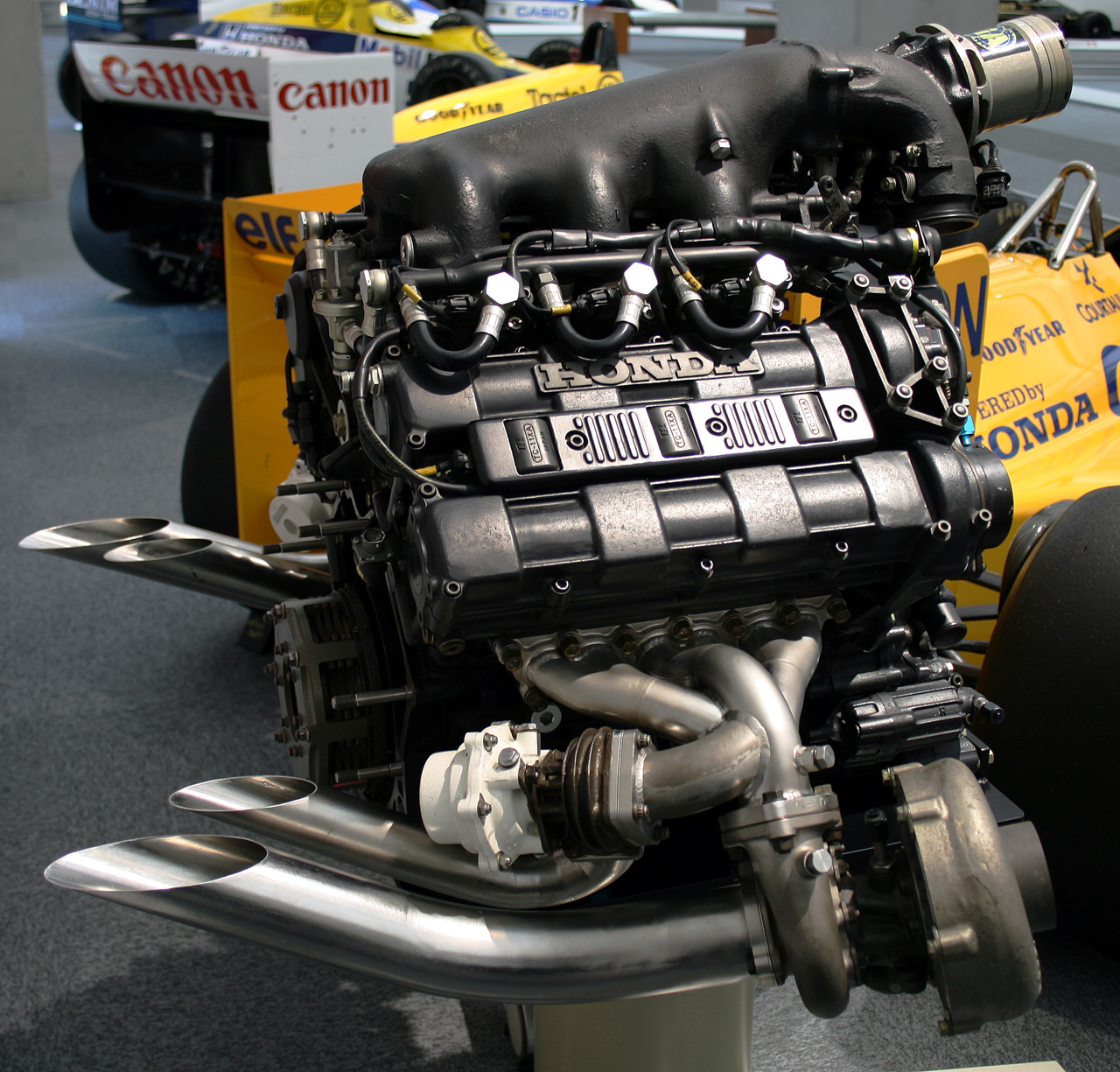
#947
Racing Rotary Since 1983

Thread Starter
iTrader: (6)
""blades are driven by impact and reaction of the gasses".
In other words the turbine blades are driven not just by flow and pressure, but also in our case, by the pulse of the port opening.""
i have logged EMP (pre turbo exhaust manifold pressure) since 2004. i have always been struck by the degree of rotary exhaust pulse violence V the piston equivalent.
of course there is no mystery here... the brew exhaust port is amazing w re to efficacy.
it is huge
it is PERIPHERAL (as in direct... hardly any port runner. no bends. no flow resistance)
long duration being open
IMMEDIATE OPEN v a valve's slow dynamic profile
IMMEDIATE CLOSE
the poor turbine wheel must feel like it is being hit w a hammer
my data supports this.
looking at 4000 to 8650 at 25.6 average boost...
average EMP 28.66 psi
min average 14.98
max average 38.37
my EMP port is located where the WG and primary runners meet and monitors directly from an 1/8 inch hole drilled into the front rear separator so it reads both front and rear impulses.
at 9000 RPM the brew produces 300 power impulses per second
9000 / 3 X = 3000 rotor RPM X 3 (sides to rotor) = 9000 power impulses per minute X 2 (rotors) = 18,000 power impulses in a minute / 60 seconds = 300 power impulses in a second.
i logged 11 per second which means my data represents 3.6% of the impulses.
a poor snapshot. (my new ECU ViPEC V88 will log 50/sec)
nevertheless, it is clear that the pressure within the manifold between pulses is less than 10 psi and the spike max impulse at around 25 psi boost could be 40.
these impulses drive the turbine. while i don't know the formula i suspect their power measured thru a tube diminishes in a non-linear fashion w re to tube length.... as does heat. meaning double the length and you get less than 50% of the power/heat.
size matters and short is Huge. (sorry, couldn't resist)
as mentioned before, i open the exhaust port a bit early to re-direct part of the pulse from the crank to the turbine wheel.
the rotary exhaust port is a wondrous thing. most of the reason for the fact that the rotary runs at approx 425 higher EGT (1322 piston, 1750 rotary) is the heat generated by the grenade going off internally (combustion) does not have to thread its way around the exhaust valve stem. no twisting exhaust port. it has an immediate exit to the turbine.
i am quite interested in comparing the two manifolds as to EMP/EGT given the 51% larger cross sectional area..
BTW, the F1 turbo pic is eye candy of the first order and is lots upon which to noodle. thanks for it.
hc
In other words the turbine blades are driven not just by flow and pressure, but also in our case, by the pulse of the port opening.""
i have logged EMP (pre turbo exhaust manifold pressure) since 2004. i have always been struck by the degree of rotary exhaust pulse violence V the piston equivalent.
of course there is no mystery here... the brew exhaust port is amazing w re to efficacy.
it is huge
it is PERIPHERAL (as in direct... hardly any port runner. no bends. no flow resistance)
long duration being open
IMMEDIATE OPEN v a valve's slow dynamic profile
IMMEDIATE CLOSE
the poor turbine wheel must feel like it is being hit w a hammer
my data supports this.
looking at 4000 to 8650 at 25.6 average boost...
average EMP 28.66 psi
min average 14.98
max average 38.37
my EMP port is located where the WG and primary runners meet and monitors directly from an 1/8 inch hole drilled into the front rear separator so it reads both front and rear impulses.
at 9000 RPM the brew produces 300 power impulses per second
9000 / 3 X = 3000 rotor RPM X 3 (sides to rotor) = 9000 power impulses per minute X 2 (rotors) = 18,000 power impulses in a minute / 60 seconds = 300 power impulses in a second.
i logged 11 per second which means my data represents 3.6% of the impulses.
a poor snapshot. (my new ECU ViPEC V88 will log 50/sec)
nevertheless, it is clear that the pressure within the manifold between pulses is less than 10 psi and the spike max impulse at around 25 psi boost could be 40.
these impulses drive the turbine. while i don't know the formula i suspect their power measured thru a tube diminishes in a non-linear fashion w re to tube length.... as does heat. meaning double the length and you get less than 50% of the power/heat.
size matters and short is Huge. (sorry, couldn't resist)
as mentioned before, i open the exhaust port a bit early to re-direct part of the pulse from the crank to the turbine wheel.
the rotary exhaust port is a wondrous thing. most of the reason for the fact that the rotary runs at approx 425 higher EGT (1322 piston, 1750 rotary) is the heat generated by the grenade going off internally (combustion) does not have to thread its way around the exhaust valve stem. no twisting exhaust port. it has an immediate exit to the turbine.
i am quite interested in comparing the two manifolds as to EMP/EGT given the 51% larger cross sectional area..
BTW, the F1 turbo pic is eye candy of the first order and is lots upon which to noodle. thanks for it.
hc
#948
Banned. I got OWNED!!!

I must also add that I too feel that flow to the turbine wheel is priority number 1. Carry on.
#949
Blue TII, I think you are going to find that setup not ideal. For one just doing quick rough math you'll have less flow than a 50mm gate but you will have the response of a 60mm gate. I'm not sure why there is a need for anyone to run dual 60mm gates it honestly serves little to no purpose. I've ran dual 44's which flow more than a single 60mm as well as a single 60mm on 13B's making 900whp, without any issue in boost control. I wouldn't run the swing gates, while a good idea they definitely have reliability issues.
i completely agree w you re thick wall tubing... i was referring to the thinner stuff which often has cracking issues and should have stated it as such...
No problem sir I wasn't knocking you as much as clarifying for others "tubing" doesn't only come in thin wall.
I've run gates near the engine on 6" runners to 21" runners and all I can say is a lot depends on the way everything is set up, but rarely do I see spikes in boost logs while on the dyno once dialed in.
I know this first hand with our FC manifolds, they seem to out perform just about everything else we make.
Funny I was thinking the same thing after seeing all this.
Should be as important to you as driving the turbine once things get going, though I would like to think of it more as letting the engine breath.
Compressor needs certain power for given airflow and pressure ratio and this power is extracted from heat, pressure differential and mass flow of exhaust gases through the turbine. But there is also that strong pulse effect. Main part of whole exhaust mass flow is concentrated in blowdown phase of exhaust stroke and for best transient response, lowest boost threshold and lowest backpressure with other parameters held equal, its vital to have turbine flow as #1 priority without any disruption to flow.
Its really simple, turbine needs certain energy and manifold should deliver it most efficiently. Heat losses, pressure losses and loss of pulsing effect must be made up by increase in pressure as mass flow is kept constant.
Whats even better, turbine preferred manifold will support larger hotsides without any loss of response for even lower backpressure and EGT's. Its been already reported by Turblown, that quite big hotsides on properly designed manifolds have lower boost threshold even though they "should" need more mass flow to deliver same energy. IMO its clear indication that larger hotsides work with higher efficiency. Some people say that its due to leverage effect, I believe that it lies in certain parameter concerning blade tip speed and velocity of gas entering the turbine.
Perfect example are F1 turbo engines. They were extracting quite big portion of energy to power compressors to very high pressure ratios and flow levels, yet they had lower exhaust pressure than intake pressure and wastegate runners seems to be positioned at about 90 degrees from collector on all setups, no magic there
Turblown should see boost threshold sooner, more than likely in most circumstances it will take longer to reach peak boost though, depending on what your trying to do on what type of engine this will either be very noticeable or not too bad.
Pics of F1 cars to prove a point are pointless, I have pics stuffed in every corner of my hard drive of F1, Cart, Champ Car, IMSA, Rally you name it. Guess what? Some have WG priority some have Turbine priority. None have I ever seen with WG at 90* of the runners if it looks that way your not seeing the whole picture or it isn't what you think it is. Some ran no WG's back in the day and strictly ran off inlet pressure valves. Some use long runners, some use short runners, some use stepped runners like N/a. All are at the highest levels of motorsports. All are engineered at exceptionally high levels. One thing is the same on all of them though...
Overall this whole debate is a bit much. Senza Pari's manifold works, Howard's manifold works, Elliot's manifolds work, My manifolds work. All are different just like what I just stated above. None of us or our customers are competing at F1 levels. The one thing that should be a given regardless is smooth flow to the gate is your best bet at making a good solid performing setup that regulates boost well wether it has priority or not and regardless of boost level. I've ran over 60psi through these engines and still needed to get flow to the gate correct or it had issues. My Buddy Jess runs over 200psi on his setups and flow through the gate matters or he has issues.
We could all argue all day what's better. It's no different than arguing about Heat rejection versus flow on IC's.
Smartest thing said here.
~S~
Originally Posted by Howard Coleman
i completely agree w you re thick wall tubing... i was referring to the thinner stuff which often has cracking issues and should have stated it as such...
Originally Posted by SENZA PARI
The problem with this is once the gates open, you still have an entire runners length of exhaust which has already passed (the gate), and still reaches the turbo, causing a spike. How moderate or severe of a spike is dependant on the conditions/setup, but the bottom line is that a gate placed near the motor is not an ideal location if you want to best use it for its intended purpose.
Originally Posted by Barry Bordes
The straighter the pipe the better. Ideally the turbine blades should "see" the port opening!
Originally Posted by slides
People are putting way to much effort into wastegate flow setup.
Originally Posted by slides
"letting the wastegate breathe"
Originally Posted by Liborek
Compressor needs certain power for given airflow and pressure ratio and this power is extracted from heat, pressure differential and mass flow of exhaust gases through the turbine. But there is also that strong pulse effect. Main part of whole exhaust mass flow is concentrated in blowdown phase of exhaust stroke and for best transient response, lowest boost threshold and lowest backpressure with other parameters held equal, its vital to have turbine flow as #1 priority without any disruption to flow.
Its really simple, turbine needs certain energy and manifold should deliver it most efficiently. Heat losses, pressure losses and loss of pulsing effect must be made up by increase in pressure as mass flow is kept constant.
Whats even better, turbine preferred manifold will support larger hotsides without any loss of response for even lower backpressure and EGT's. Its been already reported by Turblown, that quite big hotsides on properly designed manifolds have lower boost threshold even though they "should" need more mass flow to deliver same energy. IMO its clear indication that larger hotsides work with higher efficiency. Some people say that its due to leverage effect, I believe that it lies in certain parameter concerning blade tip speed and velocity of gas entering the turbine.
Perfect example are F1 turbo engines. They were extracting quite big portion of energy to power compressors to very high pressure ratios and flow levels, yet they had lower exhaust pressure than intake pressure and wastegate runners seems to be positioned at about 90 degrees from collector on all setups, no magic there
Pics of F1 cars to prove a point are pointless, I have pics stuffed in every corner of my hard drive of F1, Cart, Champ Car, IMSA, Rally you name it. Guess what? Some have WG priority some have Turbine priority. None have I ever seen with WG at 90* of the runners if it looks that way your not seeing the whole picture or it isn't what you think it is. Some ran no WG's back in the day and strictly ran off inlet pressure valves. Some use long runners, some use short runners, some use stepped runners like N/a. All are at the highest levels of motorsports. All are engineered at exceptionally high levels. One thing is the same on all of them though...
Overall this whole debate is a bit much. Senza Pari's manifold works, Howard's manifold works, Elliot's manifolds work, My manifolds work. All are different just like what I just stated above. None of us or our customers are competing at F1 levels. The one thing that should be a given regardless is smooth flow to the gate is your best bet at making a good solid performing setup that regulates boost well wether it has priority or not and regardless of boost level. I've ran over 60psi through these engines and still needed to get flow to the gate correct or it had issues. My Buddy Jess runs over 200psi on his setups and flow through the gate matters or he has issues.
We could all argue all day what's better. It's no different than arguing about Heat rejection versus flow on IC's.
Originally Posted by MannyKiller
There's a perfect balance somewhere..
~S~
Last edited by Zero R; 06-23-12 at 02:56 PM.