compressor output 329 F. how much pre turbo water?
#1
Racing Rotary Since 1983

Thread Starter
iTrader: (6)
compressor output 329 F. how much pre turbo water?
i am running E85 so i really don't need any in chamber cooling. i do want to bring down the temperature of the charge air coming out of my turbo.
here's a dyno run from today...

the bottom two plots are the temp of the air coming out of the GT4094r turbo,
329 F, and the temp of the air at the stock IAT location 147F.
we have no knock thanks mainly to the E85 but i want to reduce the compressor temp.
we are around 560 hp and will be raising the boost to 29.
i have a nice setup and will plumb a nozzle into the top of the airfilter. straight water.
my question is what CC (all pre-turbo) do you suggest at 600 hp? again, i do not need knock help, i just want to take 50/100 F out of the compressor.
thanks,
howard
here's a dyno run from today...

the bottom two plots are the temp of the air coming out of the GT4094r turbo,
329 F, and the temp of the air at the stock IAT location 147F.
we have no knock thanks mainly to the E85 but i want to reduce the compressor temp.
we are around 560 hp and will be raising the boost to 29.
i have a nice setup and will plumb a nozzle into the top of the airfilter. straight water.
my question is what CC (all pre-turbo) do you suggest at 600 hp? again, i do not need knock help, i just want to take 50/100 F out of the compressor.
thanks,
howard
#3
Of topic...
Have you tried winding in more timing half a degree at the time? I'm suspicious you don't have a lot of power hiding there as much as 60BHP at that 560BHP power level.
At that outlet temperature 100cc/min water completely vapourised will reduce the air temperature by 10degC.
329degF = 165degC
each 100cc/min vaporised will reduce the compressor outlet temperature by ~10degC in theory.
I don't think you'll get any power from the lower outlet temperature but you will add knock protection. I have personally warped apex seals, overheated and flattened corner seal springs and also broken a rear engine end plate using E85 tuned richer than your ratio. I was pushing the envelope of my setup however.
0.78 lambda / 11.5:1 metered, with ~300cc/min per 400bhp worked well for me. I was using more timing than you are, slightly more boost, albeit at a lower flow / power level (because of turbine choke) on a 9.4:1 compression engine.
From memory I was getting up around 185degF / 85degC IAT temperatures after standing 400m even in winter.
Have you tried winding in more timing half a degree at the time? I'm suspicious you don't have a lot of power hiding there as much as 60BHP at that 560BHP power level.
At that outlet temperature 100cc/min water completely vapourised will reduce the air temperature by 10degC.
329degF = 165degC
each 100cc/min vaporised will reduce the compressor outlet temperature by ~10degC in theory.
I don't think you'll get any power from the lower outlet temperature but you will add knock protection. I have personally warped apex seals, overheated and flattened corner seal springs and also broken a rear engine end plate using E85 tuned richer than your ratio. I was pushing the envelope of my setup however.
0.78 lambda / 11.5:1 metered, with ~300cc/min per 400bhp worked well for me. I was using more timing than you are, slightly more boost, albeit at a lower flow / power level (because of turbine choke) on a 9.4:1 compression engine.
From memory I was getting up around 185degF / 85degC IAT temperatures after standing 400m even in winter.
#4
Howard, what are your EGT's like at 25psi and do you think lowering the intake temps yeild siginificantly lower EGT's? I also run the GT4094R with the same specs as yours. I am also running 25+ psi, but on pump fuel. I am seeing a little over 1900F EGT' at peak. I have no Idea what my compressor temps are.
#5
So this is what I came up with over morning coffee today--on the back of a napkin, so to speak.
Knowing Howard likes to run numbers, let's take his cue and take an analytical approach to demonstrate how we might solve this interesting problem:
What we need to know: Temp rise, heated mass, specific heat (of the mass), a period of time and max boost as absolute pressure.
Temp rise = t(rise) = 261 deg F derived from: 329 deg F (outlet) - 68 deg F (compressor inlet, dry air, estimated) We're using HC's existing recorded temp for demonstration purposes. Note that the outlet temp will likely rise somewhat with his proposed boost increase, changing the results slightly, but not negating them.
Mass = est'd 77 lbs. @ 29psi boost. MF calculated at 100% volumetric efficiency (VE) and 8500 rpm. The 13b can move approx 77 lbs/min corrected flow under these conditions (estimated recovered density ratio = 2.64 at intake port; estimated compressor pressure ratio = 3.1)
specific heat of the mass: Air = 0.238 relative specific heat (at constant pressure and temperature, so this is approximate).
Time unit = 1 minute (this is the common unit for mass flow and injection flow, so we will use this).
Accordingly:
An air mass of 77lbs increases in temperature 261 deg F in a period of 1 minute. 77 * 261 = 20097 units. Multiply this product by the specific heat of the mass and you can quantify the heat gained: 20097 * 0.238 = 4783 btu gained (normalized to a period of 1 minute).
So now you need to figure out how much water to add to reduce the temp by the desired amount, which Howard has stated as 50 to 100 deg F.
The latent heat of vaporization for water is about 970.4 Btu per pound of water vaporized. Water boils at 212 deg F at an ambient atmospheric pressure of 1 atm which is about 14.7 psi and slightly higher than 1 bar.
So here's where things get tricky. Note the foregoing is the heat of Vaporization--and note that this is NOT the same as Atomization. Because the boiling point of water rises with an increase in the ambient pressure, there is now a lower delta between the compressor outlet temperature and the temperature at which water boils. This is important because it sets a practical limit to how much heat you can remove with pure water. If the water doesn't boil off, the temp isn't going to be reduced much, or very quickly. The rate at which water vaporizes below its boiling point is much slower (aka evaporation); a process less suited or useful for reducing IATs.
At 29psi boost (gauge) the absolute pressure is going to be about 44psi or so and water boils at ~ 273 def F at this pressure. That's a difference of only 329 deg - 273 deg or 56 deg F that we can efficiently/effectively remove by rapid vaporization. (This means we cannot lower the temp 100 deg F using water only.)
NOTE: This is the primary reason that water is limited as to its effect on reducing IATs and perhaps a factor as to why pure water may lose its effectiveness as an injectant as boost increases (per published NACA tests). Because alcohols are more volatile, the boiling point of water/alcohol mixtures are reduced; increasing the headroom available for its evaporation and thus its potential effectiveness for WAI application.
Getting back to the problem at hand:
Let's say we want to evaporate enough water to reduce the compressor sensible outlet temps by 50 deg F (in consideration of the ~ 56deg limit imposed above).
From the foregoing equations, we know that out 77# of air has gained 4783 btu to get from 68 deg F ambient to 329 deg F at the compressor outlet. So each degree F of temp rise = 18.33 btu = 4783 btu / 261 t(rise).
Therefore, to reduce the sensible temperature of the mass 50 deg F, we need to convert 18.33 * 50 or about 916 btu/min.
If we divide 916 btu by the water's latent heat of evaporation, we find that we need 0.944 pounds of water to accomplish this (916 btu/min / 970.4 btu/lb).
Water is 8.33 lb/gal and 231 cu. in./gal (by volume). Knowing this, we divide 0.944 lb / 8.33 lb = 0.113 gallons required; and,
0.113 gal * 231 = 26.178 cu in * 16.387 = 429cc / min.
So approx 429cc/min water required to reduce compressor outlet temps by ~ 50 deg F. solely by latent heat of vaporization (assuming 100% phase conversion).
And engineering types may note that, as expected, the results of the foregoing are congruent with the saturation pressure of water vapor in air at the specified conditions; thus generally validating the result.
The foregoing is simplified for purposes of illustration and is a close approximation. Some values are estimated, some assumptions have been made (e.g., dry air intake) and some factors are neglected to keep it straightforward and avoid being too technical and unnecessarily complicated.
I hope this sheds some quantitative insight on this subject and helps you guys out.
Knowing Howard likes to run numbers, let's take his cue and take an analytical approach to demonstrate how we might solve this interesting problem:
What we need to know: Temp rise, heated mass, specific heat (of the mass), a period of time and max boost as absolute pressure.
Temp rise = t(rise) = 261 deg F derived from: 329 deg F (outlet) - 68 deg F (compressor inlet, dry air, estimated) We're using HC's existing recorded temp for demonstration purposes. Note that the outlet temp will likely rise somewhat with his proposed boost increase, changing the results slightly, but not negating them.
Mass = est'd 77 lbs. @ 29psi boost. MF calculated at 100% volumetric efficiency (VE) and 8500 rpm. The 13b can move approx 77 lbs/min corrected flow under these conditions (estimated recovered density ratio = 2.64 at intake port; estimated compressor pressure ratio = 3.1)
specific heat of the mass: Air = 0.238 relative specific heat (at constant pressure and temperature, so this is approximate).
Time unit = 1 minute (this is the common unit for mass flow and injection flow, so we will use this).
Accordingly:
An air mass of 77lbs increases in temperature 261 deg F in a period of 1 minute. 77 * 261 = 20097 units. Multiply this product by the specific heat of the mass and you can quantify the heat gained: 20097 * 0.238 = 4783 btu gained (normalized to a period of 1 minute).
So now you need to figure out how much water to add to reduce the temp by the desired amount, which Howard has stated as 50 to 100 deg F.
The latent heat of vaporization for water is about 970.4 Btu per pound of water vaporized. Water boils at 212 deg F at an ambient atmospheric pressure of 1 atm which is about 14.7 psi and slightly higher than 1 bar.
So here's where things get tricky. Note the foregoing is the heat of Vaporization--and note that this is NOT the same as Atomization. Because the boiling point of water rises with an increase in the ambient pressure, there is now a lower delta between the compressor outlet temperature and the temperature at which water boils. This is important because it sets a practical limit to how much heat you can remove with pure water. If the water doesn't boil off, the temp isn't going to be reduced much, or very quickly. The rate at which water vaporizes below its boiling point is much slower (aka evaporation); a process less suited or useful for reducing IATs.
At 29psi boost (gauge) the absolute pressure is going to be about 44psi or so and water boils at ~ 273 def F at this pressure. That's a difference of only 329 deg - 273 deg or 56 deg F that we can efficiently/effectively remove by rapid vaporization. (This means we cannot lower the temp 100 deg F using water only.)
NOTE: This is the primary reason that water is limited as to its effect on reducing IATs and perhaps a factor as to why pure water may lose its effectiveness as an injectant as boost increases (per published NACA tests). Because alcohols are more volatile, the boiling point of water/alcohol mixtures are reduced; increasing the headroom available for its evaporation and thus its potential effectiveness for WAI application.
Getting back to the problem at hand:
Let's say we want to evaporate enough water to reduce the compressor sensible outlet temps by 50 deg F (in consideration of the ~ 56deg limit imposed above).
From the foregoing equations, we know that out 77# of air has gained 4783 btu to get from 68 deg F ambient to 329 deg F at the compressor outlet. So each degree F of temp rise = 18.33 btu = 4783 btu / 261 t(rise).
Therefore, to reduce the sensible temperature of the mass 50 deg F, we need to convert 18.33 * 50 or about 916 btu/min.
If we divide 916 btu by the water's latent heat of evaporation, we find that we need 0.944 pounds of water to accomplish this (916 btu/min / 970.4 btu/lb).
Water is 8.33 lb/gal and 231 cu. in./gal (by volume). Knowing this, we divide 0.944 lb / 8.33 lb = 0.113 gallons required; and,
0.113 gal * 231 = 26.178 cu in * 16.387 = 429cc / min.
So approx 429cc/min water required to reduce compressor outlet temps by ~ 50 deg F. solely by latent heat of vaporization (assuming 100% phase conversion).
And engineering types may note that, as expected, the results of the foregoing are congruent with the saturation pressure of water vapor in air at the specified conditions; thus generally validating the result.
The foregoing is simplified for purposes of illustration and is a close approximation. Some values are estimated, some assumptions have been made (e.g., dry air intake) and some factors are neglected to keep it straightforward and avoid being too technical and unnecessarily complicated.
I hope this sheds some quantitative insight on this subject and helps you guys out.
#6
Racing Rotary Since 1983

Thread Starter
iTrader: (6)
Thanks Everyone for your valuable responses.
we will start w an M5 which is 315 CC at 100. it will be a tad over-driven.
if it is up an running we dyno next tuesday and i will post the data. i wouldn't mind using meth but wouldn't get thru tech unless i wrap my 4.5 gallon AI tank in steel. just don't have the time ATM.
i could do a 40M-60W mix which isn't flammable... if i don't get what i want w water that will be on the menue for tues.
"what are your EGT's like at 25psi and do you think lowering the intake temps yield significantly lower EGT's?"
EGTs top at 1650.
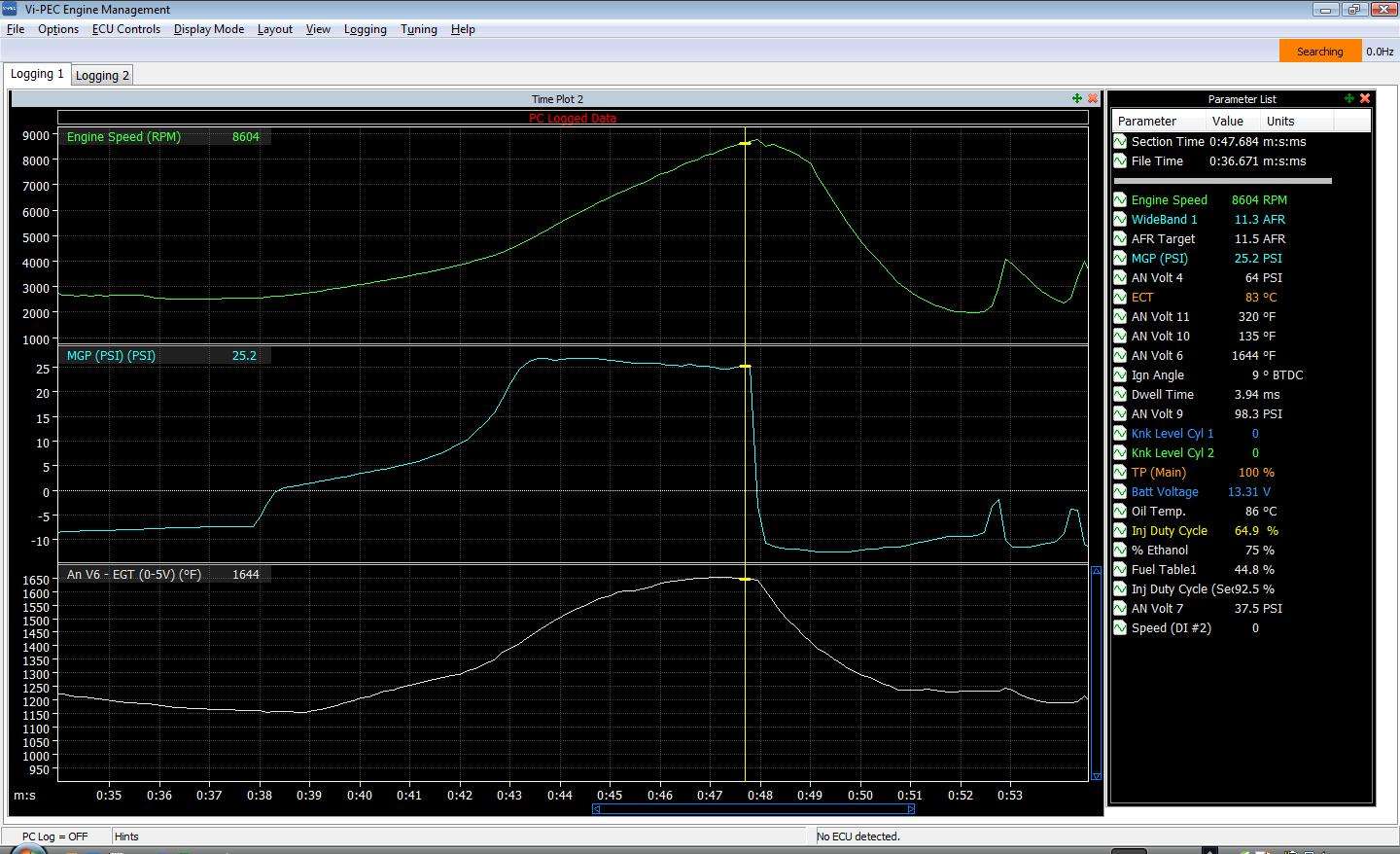
EGTs are a function of timing and to a lesser extent AFRs so IAT isn't much of a factor. 1900 indicates you either have too little timing or too much timing or you are too lean.
howard
we will start w an M5 which is 315 CC at 100. it will be a tad over-driven.
if it is up an running we dyno next tuesday and i will post the data. i wouldn't mind using meth but wouldn't get thru tech unless i wrap my 4.5 gallon AI tank in steel. just don't have the time ATM.
i could do a 40M-60W mix which isn't flammable... if i don't get what i want w water that will be on the menue for tues.
"what are your EGT's like at 25psi and do you think lowering the intake temps yield significantly lower EGT's?"
EGTs top at 1650.
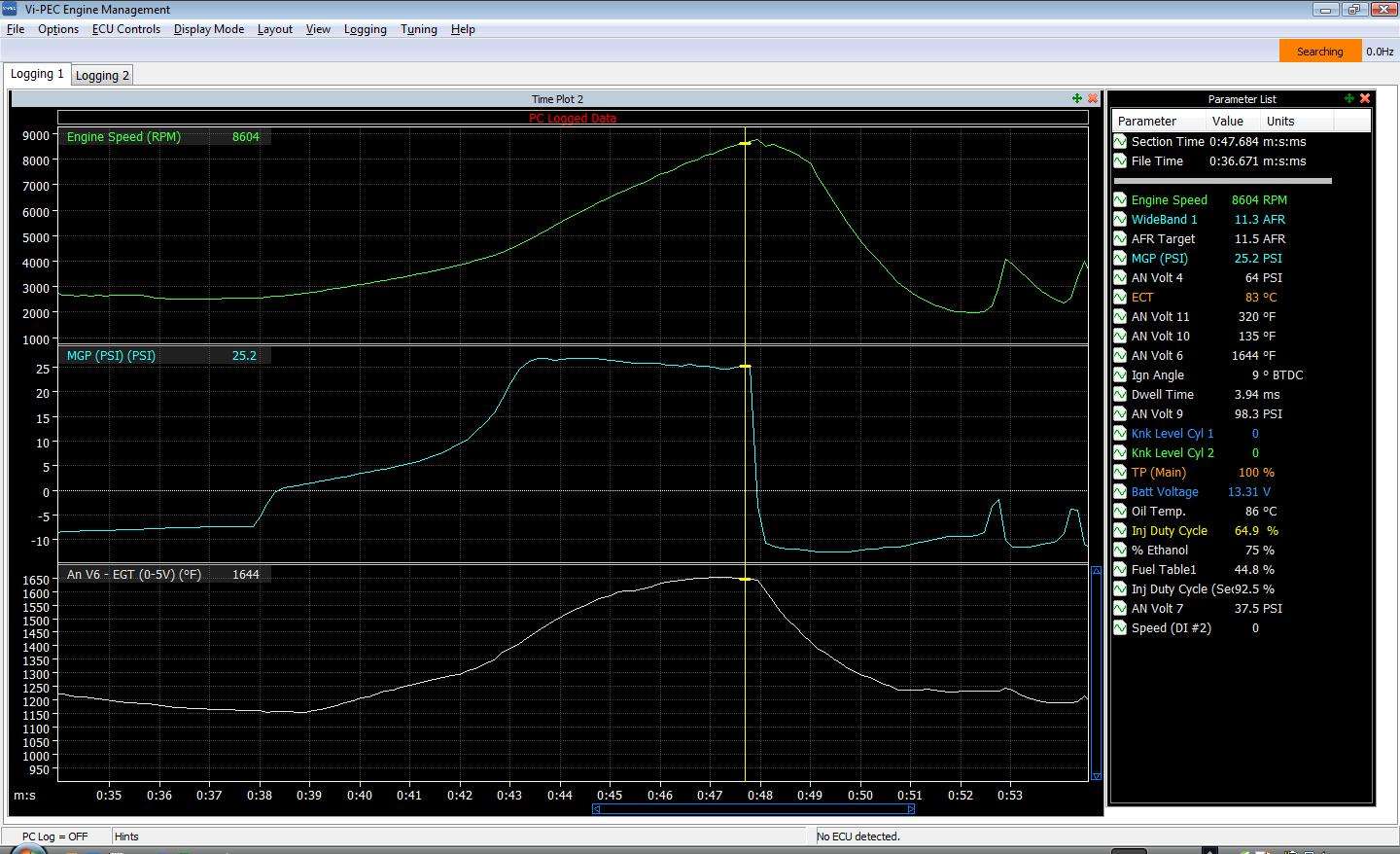
EGTs are a function of timing and to a lesser extent AFRs so IAT isn't much of a factor. 1900 indicates you either have too little timing or too much timing or you are too lean.
howard
Last edited by Howard Coleman; 10-04-13 at 04:24 PM.
Trending Topics
#8
Howard,
I would shoot for temps after the intercooler to be 45C or less. That's a pretty standard design point. 165C compressor outlets is not uncommon. Just keep increasing the pre turbo water as far as you are willing to try and build a full data set. Then you can make a trendline in Excel pretty easily to see the relationship between preturbo cc and post intercooler air temp. That will tell you how close these preliminary estimates are.
With enough time and resources, you could put a whole study together to see the effect of different water/meth mixes and different levels of flow.
I would shoot for temps after the intercooler to be 45C or less. That's a pretty standard design point. 165C compressor outlets is not uncommon. Just keep increasing the pre turbo water as far as you are willing to try and build a full data set. Then you can make a trendline in Excel pretty easily to see the relationship between preturbo cc and post intercooler air temp. That will tell you how close these preliminary estimates are.
With enough time and resources, you could put a whole study together to see the effect of different water/meth mixes and different levels of flow.
#9
Racing Rotary Since 1983

Thread Starter
iTrader: (6)
neat.... love to do Excel graphing as well as the slicing and dicing. currently charge air temps at my OE position thermocouple are 46% of the turbo discharge temp.
we are scheduled to dyno next tuesday so i will have some interesting data.
hc
we are scheduled to dyno next tuesday so i will have some interesting data.
hc
#10
Water doesn't really do anything for the ait's compared to 50/50 WM, I'm doing lots of testing and tuning lately spraying pre turbo and post IC, with different nozzle sizes. I was spraying water only and the ait's would rise alot, and now with the water/meth its a huge difference in keeping the ait's low and keep them from rising during boost, the ait's are holding steady and drop after a pull in any gear, and after a run through the gears they are the same afterwards as before the run, they go up and down a few degrees after shifting gears. FRAITS in the stock location. My next test is going to be putting the post IC nozzle to the beginning of the greddy elbow, because my IC pipe to the greddy elbow gets heat from my radiator fans so this might explain a little rise in AIT after shifting gears and boosting again, but then the temps come back down through that next gear. I am spraying alot though, today I was testing with a #10 pre turbo and #12 post IC, nozzles from AIS, but they are flowing less volume due to lower pressures because of spyaing with two nozzles.
One street run my AITs started off at 28C, they dropped to 24 after a couple quick full throttles, then they rose to 29C during 3rd gear and then dropped to 22 two seconds after letting off. most other tests the temp holds steady around 25C for one example and they always drop a little right after letting off the gas.
One street run my AITs started off at 28C, they dropped to 24 after a couple quick full throttles, then they rose to 29C during 3rd gear and then dropped to 22 two seconds after letting off. most other tests the temp holds steady around 25C for one example and they always drop a little right after letting off the gas.
#12
Senior Member

good post
So this is what I came up with over morning coffee today--on the back of a napkin, so to speak.
Knowing Howard likes to run numbers, let's take his cue and take an analytical approach to demonstrate how we might solve this interesting problem:
What we need to know: Temp rise, heated mass, specific heat (of the mass), a period of time and max boost as absolute pressure.
Temp rise = t(rise) = 261 deg F derived from: 329 deg F (outlet) - 68 deg F (compressor inlet, dry air, estimated) We're using HC's existing recorded temp for demonstration purposes. Note that the outlet temp will likely rise somewhat with his proposed boost increase, changing the results slightly, but not negating them.
Mass = est'd 77 lbs. @ 29psi boost. MF calculated at 100% volumetric efficiency (VE) and 8500 rpm. The 13b can move approx 77 lbs/min corrected flow under these conditions (estimated recovered density ratio = 2.64 at intake port; estimated compressor pressure ratio = 3.1)
specific heat of the mass: Air = 0.238 relative specific heat (at constant pressure and temperature, so this is approximate).
Time unit = 1 minute (this is the common unit for mass flow and injection flow, so we will use this).
Accordingly:
An air mass of 77lbs increases in temperature 261 deg F in a period of 1 minute. 77 * 261 = 20097 units. Multiply this product by the specific heat of the mass and you can quantify the heat gained: 20097 * 0.238 = 4783 btu gained (normalized to a period of 1 minute).
So now you need to figure out how much water to add to reduce the temp by the desired amount, which Howard has stated as 50 to 100 deg F.
The latent heat of vaporization for water is about 970.4 Btu per pound of water vaporized. Water boils at 212 deg F at an ambient atmospheric pressure of 1 atm which is about 14.7 psi and slightly higher than 1 bar.
So here's where things get tricky. Note the foregoing is the heat of Vaporization--and note that this is NOT the same as Atomization. Because the boiling point of water rises with an increase in the ambient pressure, there is now a lower delta between the compressor outlet temperature and the temperature at which water boils. This is important because it sets a practical limit to how much heat you can remove with pure water. If the water doesn't boil off, the temp isn't going to be reduced much, or very quickly. The rate at which water vaporizes below its boiling point is much slower (aka evaporation); a process less suited or useful for reducing IATs.
At 29psi boost (gauge) the absolute pressure is going to be about 44psi or so and water boils at ~ 273 def F at this pressure. That's a difference of only 329 deg - 273 deg or 56 deg F that we can efficiently/effectively remove by rapid vaporization. (This means we cannot lower the temp 100 deg F using water only.)
NOTE: This is the primary reason that water is limited as to its effect on reducing IATs and perhaps a factor as to why pure water may lose its effectiveness as an injectant as boost increases (per published NACA tests). Because alcohols are more volatile, the boiling point of water/alcohol mixtures are reduced; increasing the headroom available for its evaporation and thus its potential effectiveness for WAI application.
Getting back to the problem at hand:
Let's say we want to evaporate enough water to reduce the compressor sensible outlet temps by 50 deg F (in consideration of the ~ 56deg limit imposed above).
From the foregoing equations, we know that out 77# of air has gained 4783 btu to get from 68 deg F ambient to 329 deg F at the compressor outlet. So each degree F of temp rise = 18.33 btu = 4783 btu / 261 t(rise).
Therefore, to reduce the sensible temperature of the mass 50 deg F, we need to convert 18.33 * 50 or about 916 btu/min.
If we divide 916 btu by the water's latent heat of evaporation, we find that we need 0.944 pounds of water to accomplish this (916 btu/min / 970.4 btu/lb).
Water is 8.33 lb/gal and 231 cu. in./gal (by volume). Knowing this, we divide 0.944 lb / 8.33 lb = 0.113 gallons required; and,
0.113 gal * 231 = 26.178 cu in * 16.387 = 429cc / min.
So approx 429cc/min water required to reduce compressor outlet temps by ~ 50 deg F. solely by latent heat of vaporization (assuming 100% phase conversion).
And engineering types may note that, as expected, the results of the foregoing are congruent with the saturation pressure of water vapor in air at the specified conditions; thus generally validating the result.
The foregoing is simplified for purposes of illustration and is a close approximation. Some values are estimated, some assumptions have been made (e.g., dry air intake) and some factors are neglected to keep it straightforward and avoid being too technical and unnecessarily complicated.
I hope this sheds some quantitative insight on this subject and helps you guys out.
Knowing Howard likes to run numbers, let's take his cue and take an analytical approach to demonstrate how we might solve this interesting problem:
What we need to know: Temp rise, heated mass, specific heat (of the mass), a period of time and max boost as absolute pressure.
Temp rise = t(rise) = 261 deg F derived from: 329 deg F (outlet) - 68 deg F (compressor inlet, dry air, estimated) We're using HC's existing recorded temp for demonstration purposes. Note that the outlet temp will likely rise somewhat with his proposed boost increase, changing the results slightly, but not negating them.
Mass = est'd 77 lbs. @ 29psi boost. MF calculated at 100% volumetric efficiency (VE) and 8500 rpm. The 13b can move approx 77 lbs/min corrected flow under these conditions (estimated recovered density ratio = 2.64 at intake port; estimated compressor pressure ratio = 3.1)
specific heat of the mass: Air = 0.238 relative specific heat (at constant pressure and temperature, so this is approximate).
Time unit = 1 minute (this is the common unit for mass flow and injection flow, so we will use this).
Accordingly:
An air mass of 77lbs increases in temperature 261 deg F in a period of 1 minute. 77 * 261 = 20097 units. Multiply this product by the specific heat of the mass and you can quantify the heat gained: 20097 * 0.238 = 4783 btu gained (normalized to a period of 1 minute).
So now you need to figure out how much water to add to reduce the temp by the desired amount, which Howard has stated as 50 to 100 deg F.
The latent heat of vaporization for water is about 970.4 Btu per pound of water vaporized. Water boils at 212 deg F at an ambient atmospheric pressure of 1 atm which is about 14.7 psi and slightly higher than 1 bar.
So here's where things get tricky. Note the foregoing is the heat of Vaporization--and note that this is NOT the same as Atomization. Because the boiling point of water rises with an increase in the ambient pressure, there is now a lower delta between the compressor outlet temperature and the temperature at which water boils. This is important because it sets a practical limit to how much heat you can remove with pure water. If the water doesn't boil off, the temp isn't going to be reduced much, or very quickly. The rate at which water vaporizes below its boiling point is much slower (aka evaporation); a process less suited or useful for reducing IATs.
At 29psi boost (gauge) the absolute pressure is going to be about 44psi or so and water boils at ~ 273 def F at this pressure. That's a difference of only 329 deg - 273 deg or 56 deg F that we can efficiently/effectively remove by rapid vaporization. (This means we cannot lower the temp 100 deg F using water only.)
NOTE: This is the primary reason that water is limited as to its effect on reducing IATs and perhaps a factor as to why pure water may lose its effectiveness as an injectant as boost increases (per published NACA tests). Because alcohols are more volatile, the boiling point of water/alcohol mixtures are reduced; increasing the headroom available for its evaporation and thus its potential effectiveness for WAI application.
Getting back to the problem at hand:
Let's say we want to evaporate enough water to reduce the compressor sensible outlet temps by 50 deg F (in consideration of the ~ 56deg limit imposed above).
From the foregoing equations, we know that out 77# of air has gained 4783 btu to get from 68 deg F ambient to 329 deg F at the compressor outlet. So each degree F of temp rise = 18.33 btu = 4783 btu / 261 t(rise).
Therefore, to reduce the sensible temperature of the mass 50 deg F, we need to convert 18.33 * 50 or about 916 btu/min.
If we divide 916 btu by the water's latent heat of evaporation, we find that we need 0.944 pounds of water to accomplish this (916 btu/min / 970.4 btu/lb).
Water is 8.33 lb/gal and 231 cu. in./gal (by volume). Knowing this, we divide 0.944 lb / 8.33 lb = 0.113 gallons required; and,
0.113 gal * 231 = 26.178 cu in * 16.387 = 429cc / min.
So approx 429cc/min water required to reduce compressor outlet temps by ~ 50 deg F. solely by latent heat of vaporization (assuming 100% phase conversion).
And engineering types may note that, as expected, the results of the foregoing are congruent with the saturation pressure of water vapor in air at the specified conditions; thus generally validating the result.
The foregoing is simplified for purposes of illustration and is a close approximation. Some values are estimated, some assumptions have been made (e.g., dry air intake) and some factors are neglected to keep it straightforward and avoid being too technical and unnecessarily complicated.
I hope this sheds some quantitative insight on this subject and helps you guys out.
#13
Senior Member

I have been accused of over-simplifying things, so bear with me...
Wouldn't the best effect be achieved by spraying into the hot air exiting the turbo?
It just seems you'd have more of the evaporation happening as a result of the heat in the air stream, and if you spray before the turbo some of the effort would go into cooling the compressor wheel and housing.
Just wondering
Wouldn't the best effect be achieved by spraying into the hot air exiting the turbo?
It just seems you'd have more of the evaporation happening as a result of the heat in the air stream, and if you spray before the turbo some of the effort would go into cooling the compressor wheel and housing.
Just wondering
#14
Generally it is not a good idea to spray between the turbo and the IC. It may make the IC less efficient. And when I did my pre turbo WI vs post IC dyno tests, the AIt's actually rose more with the pre turbo WI, suggesting that the IC was less efficient and pre turbo WI is not the best location to cool AIT, my FRAITS was at the IC outlet and the post IC nozzle was spraying after the FRAITS. I'm now spraying W/M pre turbo and pre throttle body into the beginning of the greddy elbow, fraits in the stock location, and after a few tests tonight I think this may be working the best for AITs.
Also check out the two sites below talking about nozzle placements, although they differ a little.
Where Do I Position My Water Injection Nozzles
Where to locate your alcohol-water injection nozzle - DevilsOwn Injection
Also check out the two sites below talking about nozzle placements, although they differ a little.
Where Do I Position My Water Injection Nozzles
Where to locate your alcohol-water injection nozzle - DevilsOwn Injection
Thread
Thread Starter
Forum
Replies
Last Post
rx8volks
Canadian Forum
0
08-13-15 04:55 AM