How to f_ck up a $9,000 Mandeville 20b short block without even starting it
#1
rebreaking things

Thread Starter
Join Date: Apr 2006
Location: Manhattan
Posts: 866
Likes: 0
Received 0 Likes
on
0 Posts
How to f_ck up a $9,000 Mandeville 20b short block without even starting it
Step 1: Hire a highly recommended chassis shop in PA to modify the firewall, tunnel, move the motor back 6.5", and discover through first hand experience that they are a bunch of overpriced hacks.
Step 2: Hire a very expensive Porsche chassis shop in MA to rip out everything shop one did and do it all over again from scratch.
Step 3: pick the car up without checking the fitment of the coolant pipe exiting the rear housing because you focused on how they managed to ring up a $4,500 labor bill for an exhaust manifold (+$1,000 for materials).
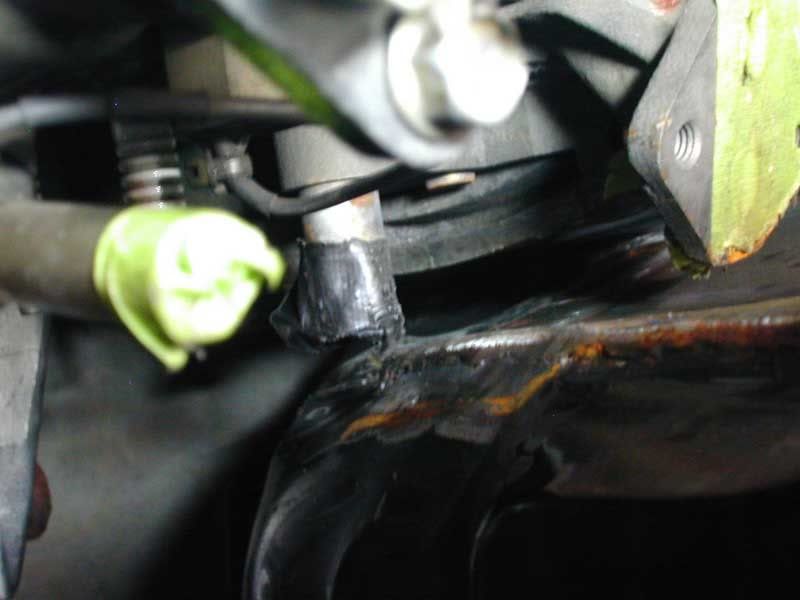
Step 4: Talk to a competent mechanic that removed the press fit pipe from the rear housing of his motor and threaded it for a 1/2" NPT fitting. It just came right out with a pair of vice grips, he said.
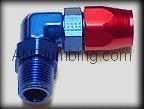
Step 5: Destroy one set of vice grips trying to take it out, accomplishing absolutely nothing, and then employ mid-evil tactics to remove the pipe with a more expensive set of vice grips that you had to drive 25 away to buy.
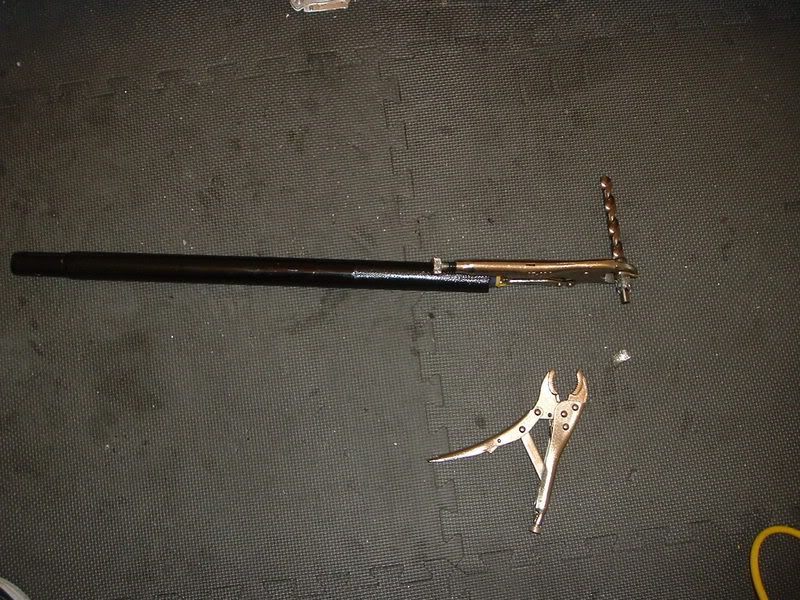
Step 6: Measure the hole and find that there is no way in hell it can be threaded for an NPT fitting without enlarging it.
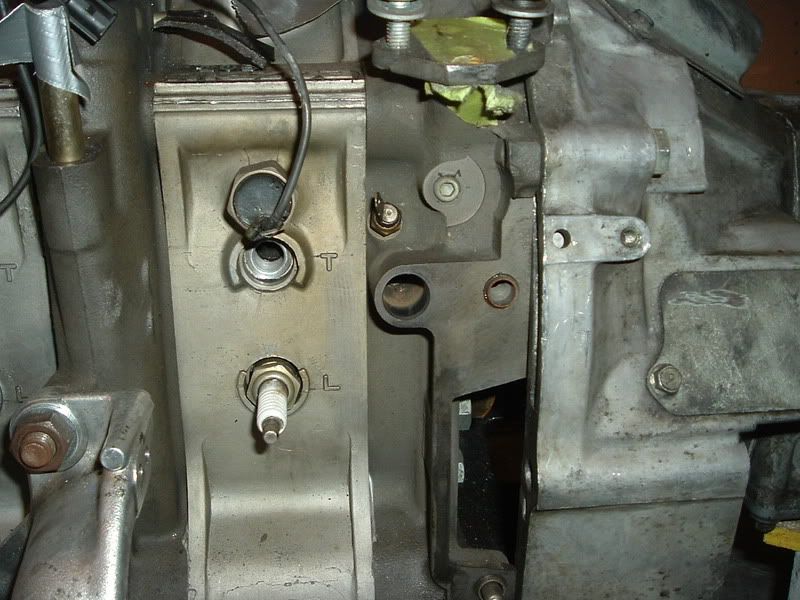
Step 7: Drive another 25 minutes back to the hardware store and **** away $200 on tools that will probably only be used once.
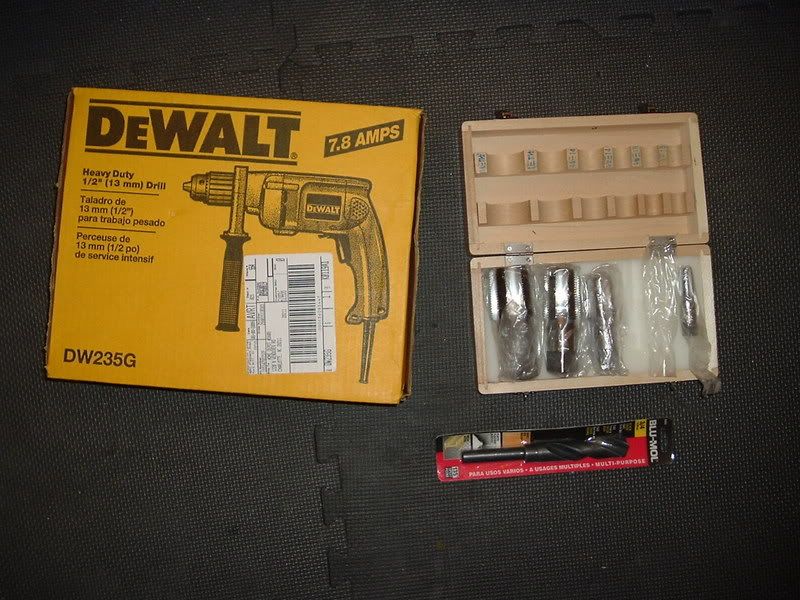
Step 8: Enlarge the hole with a drill bit that was probably developed by Exxon to run oil pipeline. At this point I remember saying, this seems like a really bad idea for many reasons. Remember that scene in Robocop when they drill the giant hole into the side of his head? He turned out ok.
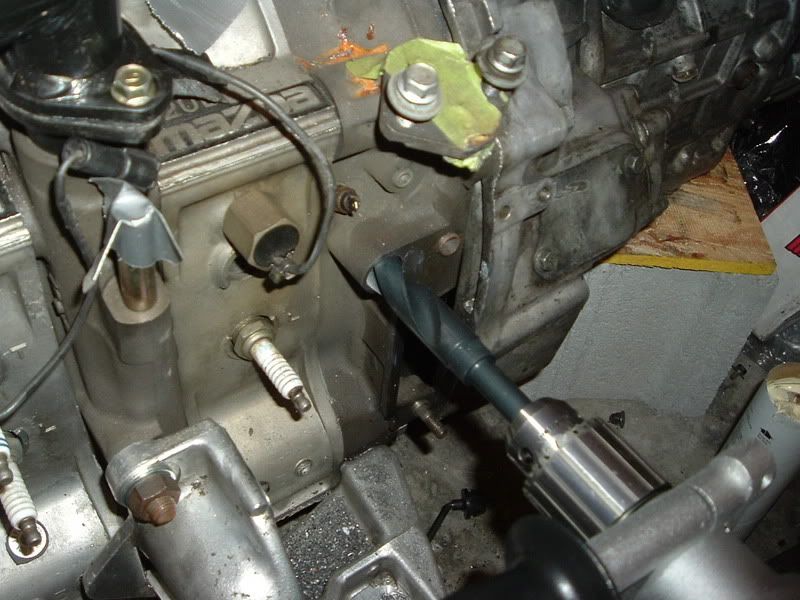
. . . . then again he was already dead when they did it.
Step 9: Successfully tap the hole, but then decide to go a little deeper to make sure the fitting doesn't stick out too far.
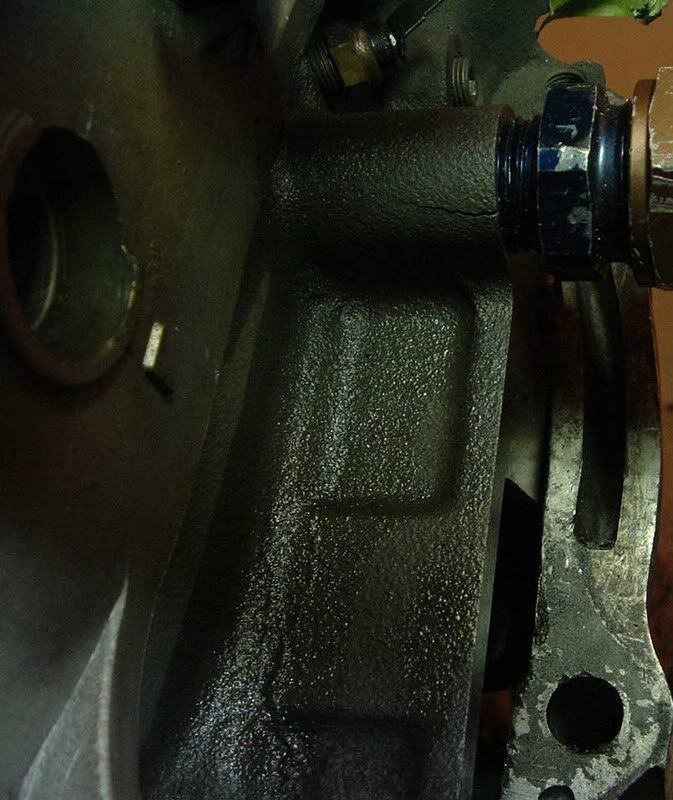
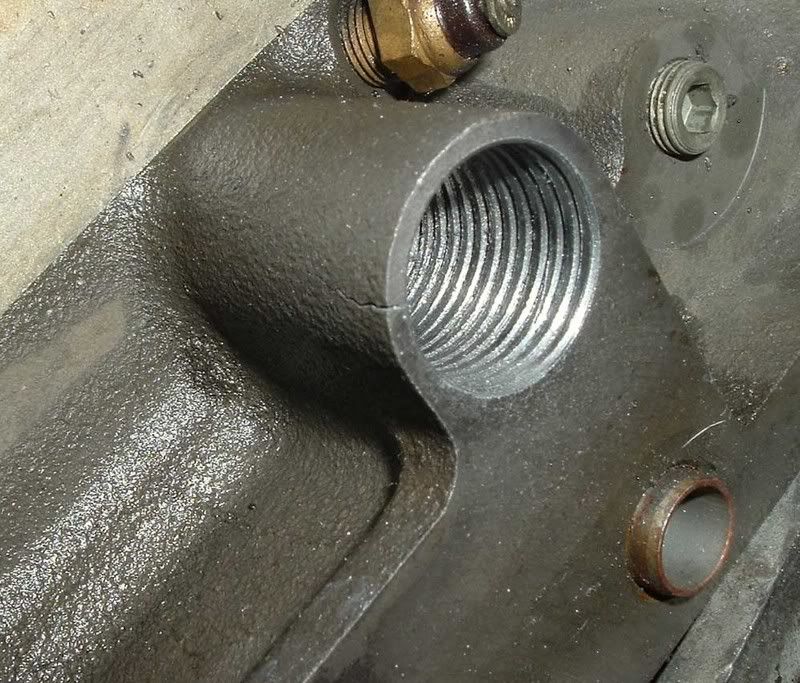
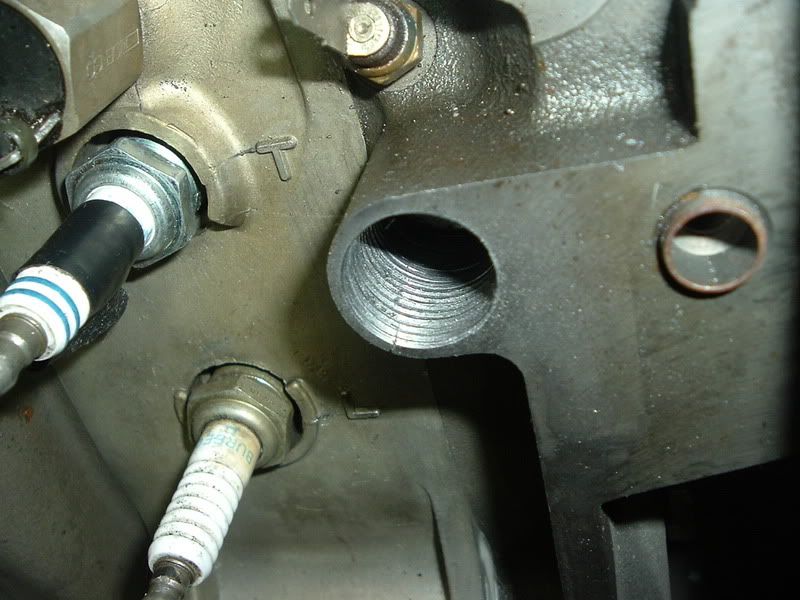
Any suggestions are appreciated. Two people have told me to weld it shut, but another said it will warp the housing. The only other option I see is replacing the rear iron.
Step 2: Hire a very expensive Porsche chassis shop in MA to rip out everything shop one did and do it all over again from scratch.
Step 3: pick the car up without checking the fitment of the coolant pipe exiting the rear housing because you focused on how they managed to ring up a $4,500 labor bill for an exhaust manifold (+$1,000 for materials).
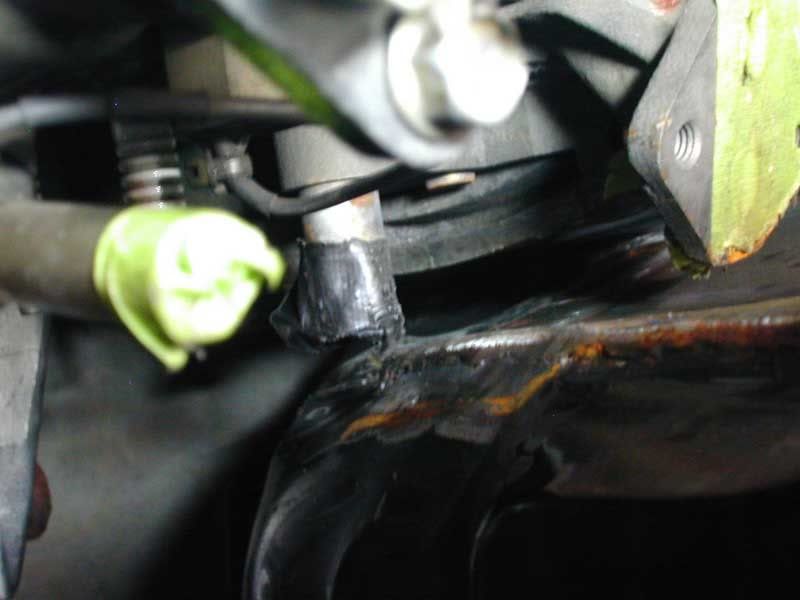
Step 4: Talk to a competent mechanic that removed the press fit pipe from the rear housing of his motor and threaded it for a 1/2" NPT fitting. It just came right out with a pair of vice grips, he said.
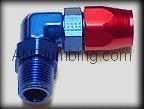
Step 5: Destroy one set of vice grips trying to take it out, accomplishing absolutely nothing, and then employ mid-evil tactics to remove the pipe with a more expensive set of vice grips that you had to drive 25 away to buy.
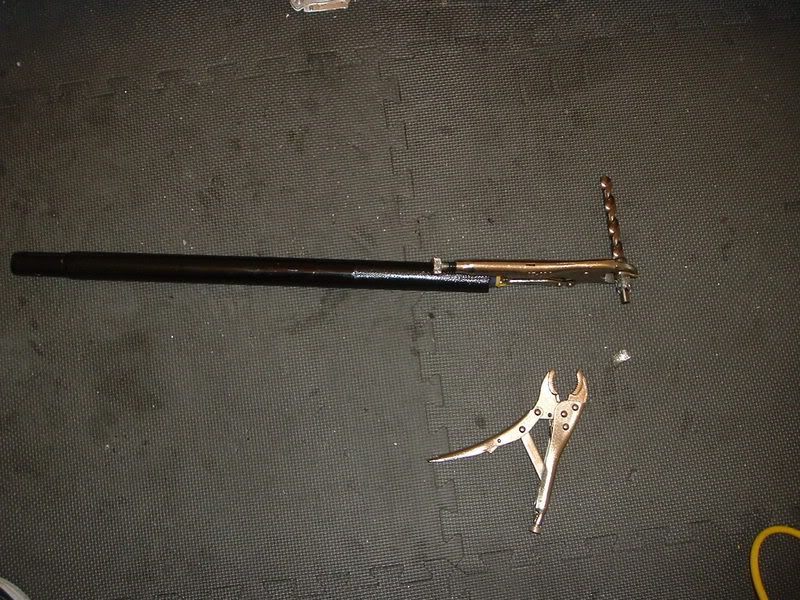
Step 6: Measure the hole and find that there is no way in hell it can be threaded for an NPT fitting without enlarging it.
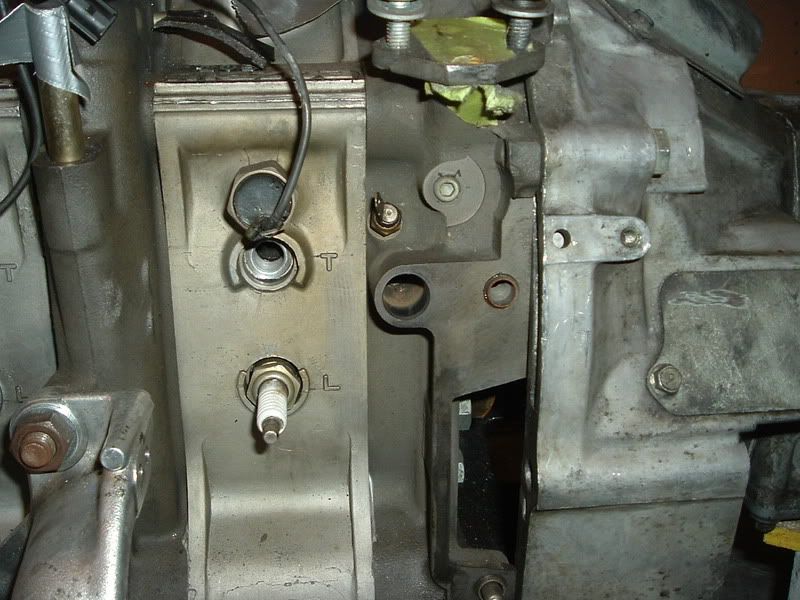
Step 7: Drive another 25 minutes back to the hardware store and **** away $200 on tools that will probably only be used once.
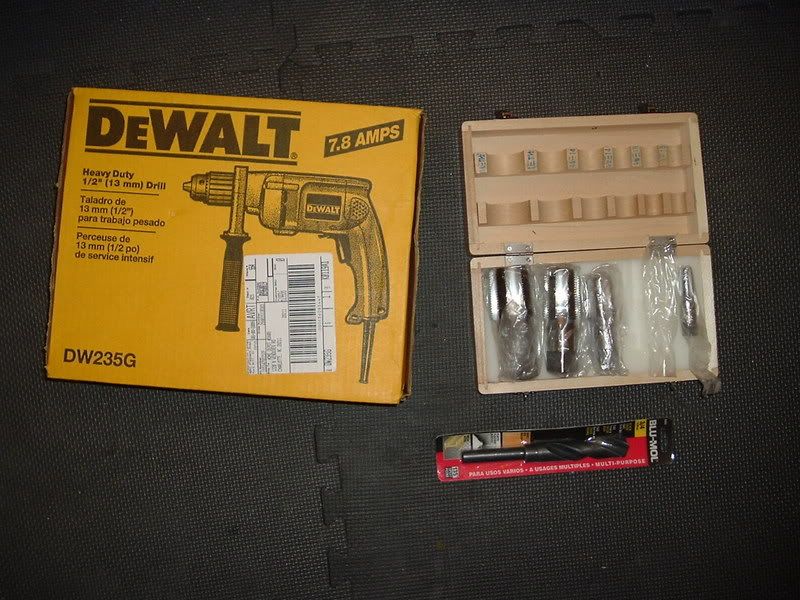
Step 8: Enlarge the hole with a drill bit that was probably developed by Exxon to run oil pipeline. At this point I remember saying, this seems like a really bad idea for many reasons. Remember that scene in Robocop when they drill the giant hole into the side of his head? He turned out ok.
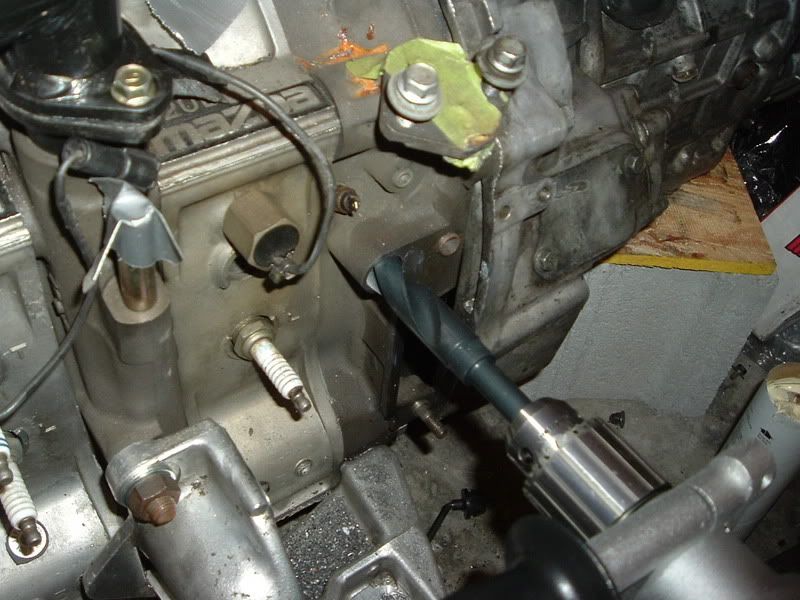
. . . . then again he was already dead when they did it.
Step 9: Successfully tap the hole, but then decide to go a little deeper to make sure the fitting doesn't stick out too far.
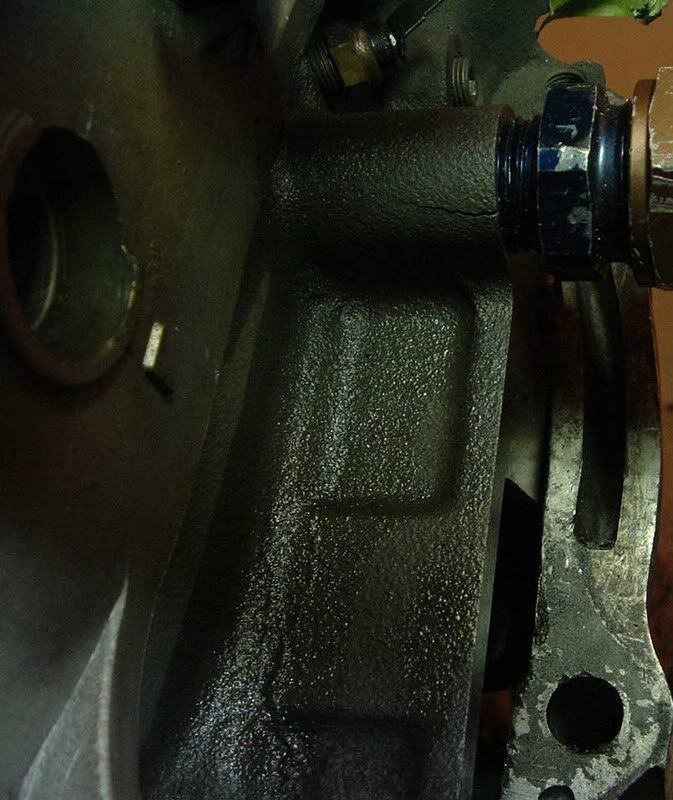
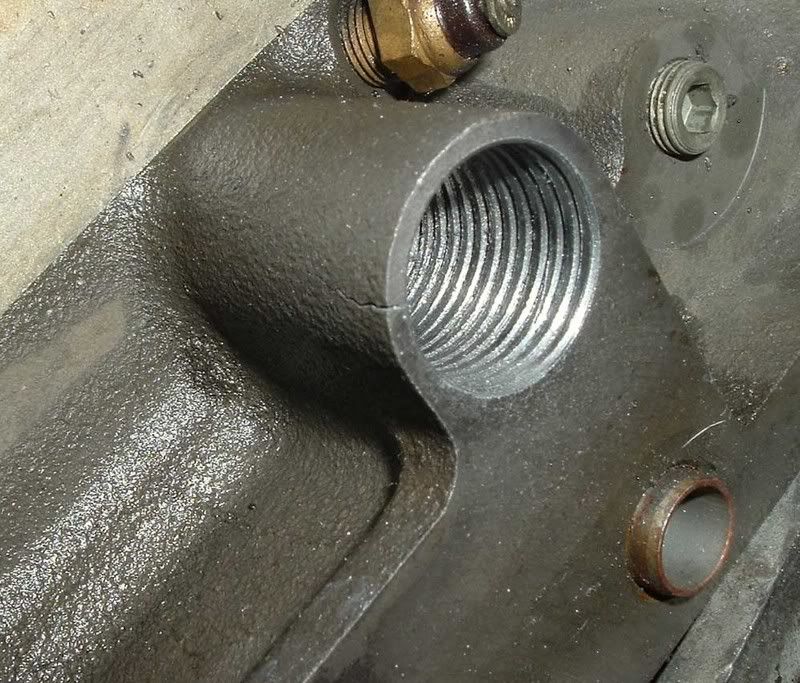
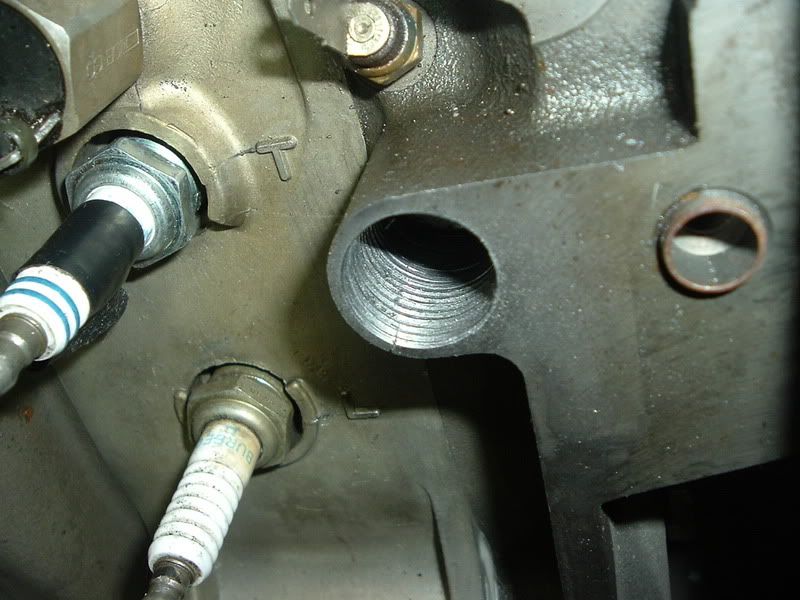


Any suggestions are appreciated. Two people have told me to weld it shut, but another said it will warp the housing. The only other option I see is replacing the rear iron.
#3
Lives on the Forum

It's called an iron, it's made of iron, iron is very difficult if not impossible to weld properly. To do it right you'd have to remove it anyway, just get a new one.
#6
Full Member

Join Date: Oct 2004
Location: Columbus OH
Posts: 180
Likes: 0
Received 0 Likes
on
0 Posts
I cant see how deep the crack is but I would not be replacing the whole iron. I put a weld on one of mine and I am not a welder. Also it only needs to hold about 1 bar of water pressure. Thats nothing, use thread sealant or jb weld.
Trending Topics
#8
Senior Member

Join Date: Nov 2005
Location: Phoenix, AZ
Posts: 310
Likes: 0
Received 0 Likes
on
0 Posts
if you were to weld a crack that small i cannot see it warping an entire iron.
And like what was said before it only need to hold up to 21 psi of water pressure
Regardless cast iron is a pita to weld period.
And like what was said before it only need to hold up to 21 psi of water pressure
Regardless cast iron is a pita to weld period.
#9
rebreaking things

Thread Starter
Join Date: Apr 2006
Location: Manhattan
Posts: 866
Likes: 0
Received 0 Likes
on
0 Posts
Thanks for all the input. The crack goes all the way through the wall and it extends about 1/2 way down to where the rotor housing meets the iron. I'm not worried about the coolant pressure as much as the stress the NPT fitting will place on it.
Black 91n/a I heard the same thing about welding to iron, but others have said if you use stainless rod you can weld it. Do you agree/disagree? The last thing I want to do is 1/2 *** this back togther only to have a problem down the road. On the other hand, the same thing could easily happen with a new housing. If it doesn't happen when it is tapped it might crack later on. Assuming it is possible to weld the housing, I could have a bead laid around it to add some strength. Otherwise I am going to have to think of a better way to do a tight 90 deg bend off the block. Before someone asks, I can't dent in the tunnel because the area that is causing the problem has a weld seam (not something I want to dent in) and it is where the gas pedal is mounted to the firewall. I could cut down the pipe a bit and try to find a really tight pre-formed rubber hose. I could also weld a 90 deg bend on the stock pipe. However I'm not sure either of these options will give me enough clearance. I could use a 3/8th fitting instead of a 1/2", but then I'm cutting the diameter of the coolant outlet down from about .70" to .55". Not sure what if any problems that could create . . .
Black 91n/a I heard the same thing about welding to iron, but others have said if you use stainless rod you can weld it. Do you agree/disagree? The last thing I want to do is 1/2 *** this back togther only to have a problem down the road. On the other hand, the same thing could easily happen with a new housing. If it doesn't happen when it is tapped it might crack later on. Assuming it is possible to weld the housing, I could have a bead laid around it to add some strength. Otherwise I am going to have to think of a better way to do a tight 90 deg bend off the block. Before someone asks, I can't dent in the tunnel because the area that is causing the problem has a weld seam (not something I want to dent in) and it is where the gas pedal is mounted to the firewall. I could cut down the pipe a bit and try to find a really tight pre-formed rubber hose. I could also weld a 90 deg bend on the stock pipe. However I'm not sure either of these options will give me enough clearance. I could use a 3/8th fitting instead of a 1/2", but then I'm cutting the diameter of the coolant outlet down from about .70" to .55". Not sure what if any problems that could create . . .
Last edited by CMonakar; 11-04-06 at 11:49 PM.
#10
Junior Member

Join Date: Nov 2006
Location: Portland OR
Posts: 45
Likes: 0
Received 0 Likes
on
0 Posts
man uguys suck.the rx-7 has brought us together like a family.so lets use our knowledge and experience with these cars and help eachother out im about to blow mine up.i jus need a little advice thats all. if not for me then do for the rotary.
#11
registered user

iTrader: (1)
Join Date: Jan 2006
Location: San Diego
Posts: 2,469
Likes: 0
Received 0 Likes
on
0 Posts
Tapping iron with a tappered tap is tricky. Ive done similar damage at least once. I say replace the rear Iron. Isn't a 13b-re rear iron the same as a 20B rear iron? If so you should be able to get one pretty easily.
If it where me personaly, I would block off the hole with JB weld, or something similar, and if you really need a heater take water from the water pump outlet.
If you replace the iron, next time use strait metric 18mm thread with a copper washer. The outlet is about 17.8MM. For the greatest clearence, use a banjo, If I'm not mistaken its the same size banjo that the oil cooler used.
If it where me personaly, I would block off the hole with JB weld, or something similar, and if you really need a heater take water from the water pump outlet.
If you replace the iron, next time use strait metric 18mm thread with a copper washer. The outlet is about 17.8MM. For the greatest clearence, use a banjo, If I'm not mistaken its the same size banjo that the oil cooler used.
#13
Lives on the Forum

I'm no welding expert, but I know that one shouldn't select iron when engineering a part that has to be welded. The problem with a crack, even if it's welded (unless it's perfect, which it never is), is that it will grow over time, especially in brittle materials, and iron is a brittle material.
To solve the problem of how to get a hose on there I'd look to fabricate an elbow using the stock tube. I'd pull it out, cut it off at 45 degrees slightly away from the block and weld on another piece, also cut at 45 degrees and insert it back into the block. This will make a 90 degree elbow that can hug the block very closely, closer than a bent hose can. You can then route the hose forward to wherever it needs to go.
To solve the problem of how to get a hose on there I'd look to fabricate an elbow using the stock tube. I'd pull it out, cut it off at 45 degrees slightly away from the block and weld on another piece, also cut at 45 degrees and insert it back into the block. This will make a 90 degree elbow that can hug the block very closely, closer than a bent hose can. You can then route the hose forward to wherever it needs to go.
#14
heres what I would do: Assuming the rear iron is now toast you have nothing to lose. buy a JB weld kit and thread your fitting in. Then JB weld all around the crack; sealing it. Don't laugh. You have nothing to lose except the cost of the JB weld. If it doesnt work, you would have to replace the iron anyway. If it does work, you just saved yourself alot of time, effort, cussing and money.
#16
I would suggest to try some JB weld first, since it is the least permanent and least expensive of the processes, just periodically check for leakage and keep an eye on temps, I am sure you do that already anyhow
Next I would have the iron welded, as somone stated earlier the iron needs to be preheated, more importantly the iron needs to be cooled slowly to prevent a crack/recracking. Typically a high nickel rod is used with iron due to its composition. I would call around your area to see if anyone would be willing to take a look at it and willing to attempt it (as assembled), if not you could tear it down and have it welded, although at that point, which is my last, I owuld just replace it.
You may also want to ask some guys on Miller Motorsports Msg board, they are great guys over there and I am sure they and lend some great advice. http://www.millermotorsports.com/mbo...isplay.php?f=3

Next I would have the iron welded, as somone stated earlier the iron needs to be preheated, more importantly the iron needs to be cooled slowly to prevent a crack/recracking. Typically a high nickel rod is used with iron due to its composition. I would call around your area to see if anyone would be willing to take a look at it and willing to attempt it (as assembled), if not you could tear it down and have it welded, although at that point, which is my last, I owuld just replace it.
You may also want to ask some guys on Miller Motorsports Msg board, they are great guys over there and I am sure they and lend some great advice. http://www.millermotorsports.com/mbo...isplay.php?f=3
#17
Seeing the title of this thread and As soon as i seen the first picture I knew what
happened.
you could jb weld the fitting in but i would put money on the crack possible getting longer
cast likes to do that.
I have welded cast lots, i even made a exhaust manifold for my rx2 using a 2nd gen
cast manifold and to get it to clear cut the pipe part off the back of it gave it a half turn
and welded it back on.
even with the force of the exhaust pipe working on that flange and massive heat
from running to lean it didn't fail.
that said
1. weld it without closing the gap welding out from the end of the crack out to the start.
2 find a 90 deg. stock pipe for that location used on jspec 13b's TII type motors
cut this fitting out of the jspec iron (it would be way to long as is)
3 jb weld (or similar) this fitting into the hole filling the nice threads which will hold lots of
epoxy and it should seal it.
matt
happened.
you could jb weld the fitting in but i would put money on the crack possible getting longer
cast likes to do that.
I have welded cast lots, i even made a exhaust manifold for my rx2 using a 2nd gen
cast manifold and to get it to clear cut the pipe part off the back of it gave it a half turn
and welded it back on.
even with the force of the exhaust pipe working on that flange and massive heat
from running to lean it didn't fail.
that said
1. weld it without closing the gap welding out from the end of the crack out to the start.
2 find a 90 deg. stock pipe for that location used on jspec 13b's TII type motors
cut this fitting out of the jspec iron (it would be way to long as is)
3 jb weld (or similar) this fitting into the hole filling the nice threads which will hold lots of
epoxy and it should seal it.
matt
#19
Banned. I got OWNED!!!
iTrader: (256)
What a nightmare... I feel your pain Bro...
The side plates are more steel than iron and can be TIG welded if you have a knowledgeable welder.. My guy is an old timer, who has been welding for over 40 years. He has welded/repaired many many sideplates for me. He has even repaired the O-ring grooves where they have broken or where corrosion caused them to collapse.
The side plates are more steel than iron and can be TIG welded if you have a knowledgeable welder.. My guy is an old timer, who has been welding for over 40 years. He has welded/repaired many many sideplates for me. He has even repaired the O-ring grooves where they have broken or where corrosion caused them to collapse.
#20
I didn't read the other post but you need to stop that crack. Mo matter what, stop that crack or it will continue. Stop drill it, Cut cut it. JB weld won't prevent the crack from progressing. Once that crack is exposed to vibration and tempatures it will get worse.
I would listen to now he is dead on what you need to do.
I would listen to now he is dead on what you need to do.
#21
Passing life by

I am sorry bud! Really am.
This is the type of work my shop does. I can see charging somewhere around the 4k range to modify your firewall and tunnel and mounts to fit the new location. Depending on the amount of new mounting locations possibly as high as 6.5k total bill. I do not see how you received a 4k bill for an exhaust manifold. Send it back and I will have Elliot make you one for well under 2k with 321 ss ceramic coated.
This business is tuff because shops like this give us a bad name. I assume you are somewhat happy with the Porsche shops work performed even though they did not tackle all angles and over looked some aspects. Could also be chalked up to there lack of knowledge of a rotary and what the items are used for.
Next why did you insist on moving the motor 6.5 back? You knew this was going to be some serious chedda.
As far as your hole. You used a pipe fitting they enlarge the threading as they go in. These bolts should tighten up not tighten down. You probably knew this but the tighten up part of the over tq you made cracked it as you see. I use some Teflon tape or liquid Teflon and tighten to like a spark plug just a little snug.
Fixing it. Weld it up. You can gas weld it or tig weld it. Run your tap into the hole. Now weld it shut. You do not need 100% penetration but you do need penetration. After you weld this up remove and run your tap again. Now redo your fitting :-) without cranking so far. You will not warp your stuff you will not get the block anywhere near this hot. The left in tap will prevent the portion of your new hole from warping.
This is the type of work my shop does. I can see charging somewhere around the 4k range to modify your firewall and tunnel and mounts to fit the new location. Depending on the amount of new mounting locations possibly as high as 6.5k total bill. I do not see how you received a 4k bill for an exhaust manifold. Send it back and I will have Elliot make you one for well under 2k with 321 ss ceramic coated.
This business is tuff because shops like this give us a bad name. I assume you are somewhat happy with the Porsche shops work performed even though they did not tackle all angles and over looked some aspects. Could also be chalked up to there lack of knowledge of a rotary and what the items are used for.
Next why did you insist on moving the motor 6.5 back? You knew this was going to be some serious chedda.
As far as your hole. You used a pipe fitting they enlarge the threading as they go in. These bolts should tighten up not tighten down. You probably knew this but the tighten up part of the over tq you made cracked it as you see. I use some Teflon tape or liquid Teflon and tighten to like a spark plug just a little snug.
Fixing it. Weld it up. You can gas weld it or tig weld it. Run your tap into the hole. Now weld it shut. You do not need 100% penetration but you do need penetration. After you weld this up remove and run your tap again. Now redo your fitting :-) without cranking so far. You will not warp your stuff you will not get the block anywhere near this hot. The left in tap will prevent the portion of your new hole from warping.
#22
rebreaking things

Thread Starter
Join Date: Apr 2006
Location: Manhattan
Posts: 866
Likes: 0
Received 0 Likes
on
0 Posts
I'll go into all that in a different thread. Bottom line, I think you'll understand why it was over $3000 for the labor, but not over $4000.
I am probably just going to replace the rear iron. I don't want this problem to resurface down the road. Can an FD iron be ported as large as a 20b iron? I thought it could, but a few people have recently said it can't- at least not using the same port shape. The block is a D-series. If anyone has a rear iron for it let me know. Any idea what they cost new, or if they are even available anymore from Mazdacomp?
I am probably just going to replace the rear iron. I don't want this problem to resurface down the road. Can an FD iron be ported as large as a 20b iron? I thought it could, but a few people have recently said it can't- at least not using the same port shape. The block is a D-series. If anyone has a rear iron for it let me know. Any idea what they cost new, or if they are even available anymore from Mazdacomp?
#23
Senior Member

iTrader: (2)
Join Date: Apr 2006
Location: South Flo-rida..south jersey originally
Posts: 615
Received 0 Likes
on
0 Posts
if you went to pa..you should of drove alittle bit more to jersey..and got jpr imports to do the work..atleast jim knows what he is doing and is very noticed on the forum..atleast from phillly and jersey guys
#25
Banned. I got OWNED!!!
iTrader: (256)
New rear Iron
Here is what you need.....
This is NEW cosmo RE
It will work on your 20B
Its coming to me from Japan and I will have it in my hands in about 10 to 12 days.
Only difference is one tension whole needs to be drilled large to accept the larger 20 tension bolt. I can drill it for free at the machine shop...
Problem solved
This is NEW cosmo RE
It will work on your 20B
Its coming to me from Japan and I will have it in my hands in about 10 to 12 days.
Only difference is one tension whole needs to be drilled large to accept the larger 20 tension bolt. I can drill it for free at the machine shop...
Problem solved