Why Apex Seals Fail
#76
Moderator

iTrader: (3)
Join Date: Mar 2001
Location: https://www2.mazda.com/en/100th/
Posts: 30,826
Received 2,594 Likes
on
1,842 Posts
j9fd3s,
My thought would be that preignition lifting of the apex seal would relate to very short engine/seal life.
The problem we are dealing with is lifting of the apex seals as shown in the photo below.
As you can see the carbon stains are similar, located in the same spot, and seem to have been building there for a long period.
The seal tip failed from "high cycle fatigue" (30,000 miles would be about 25 million cycles).
Barry
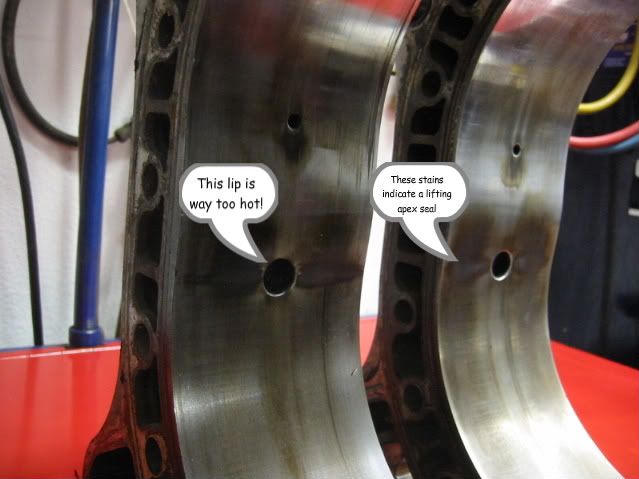
My thought would be that preignition lifting of the apex seal would relate to very short engine/seal life.
The problem we are dealing with is lifting of the apex seals as shown in the photo below.
As you can see the carbon stains are similar, located in the same spot, and seem to have been building there for a long period.
The seal tip failed from "high cycle fatigue" (30,000 miles would be about 25 million cycles).
Barry
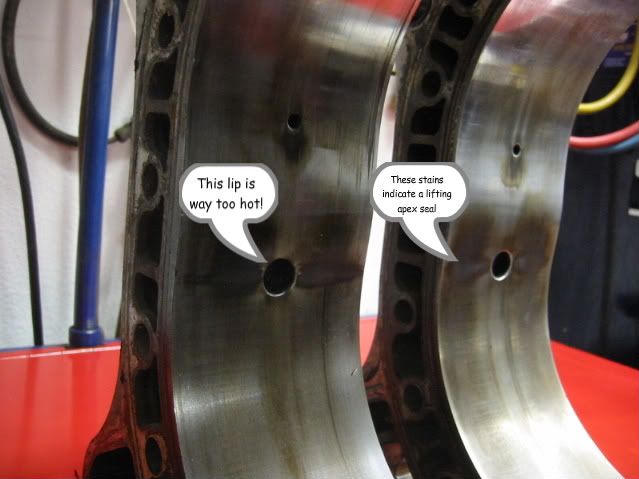
1. marks on the rotor housing surface.
2. failure of the apex seal tip
from racing beat
"Adequate cooling of rotor housings in racing applications is a challenging task. Inadequate cooling will most certainly lead to rapid apex seal wear, usually in the form of “chamfering” of the leading edge of the apex seal curved surface, and rotor housing inner surface deterioration; specifically, severe cracking, chipping, black deposits and chattering."
as to the tip failure, i see the wear pattern in every seal (even the rx2 carbon ive got here), but ive never seen an NA motor that broke. we even roadraced one for 4 seasons, in races up to 3 hours (imagine doing 14 dyno pulls a lap, times 100) with junkyard 100,000 mile seals.
if it was a fatigue failure the would ALL do it, but they don't.
#77
"Elusive, not deceptive!”

Thread Starter
i think you're describing two different things.
1. marks on the rotor housing surface.
2. failure of the apex seal tip
from racing beat
"Adequate cooling of rotor housings in racing applications is a challenging task. Inadequate cooling will most certainly lead to rapid apex seal wear, usually in the form of “chamfering” of the leading edge of the apex seal curved surface, and rotor housing inner surface deterioration; specifically, severe cracking, chipping, black deposits and chattering."
as to the tip failure, i see the wear pattern in every seal (even the rx2 carbon ive got here), but ive never seen an NA motor that broke. we even roadraced one for 4 seasons, in races up to 3 hours (imagine doing 14 dyno pulls a lap, times 100) with junkyard 100,000 mile seals.
if it was a fatigue failure the would ALL do it, but they don't.
1. marks on the rotor housing surface.
2. failure of the apex seal tip
from racing beat
"Adequate cooling of rotor housings in racing applications is a challenging task. Inadequate cooling will most certainly lead to rapid apex seal wear, usually in the form of “chamfering” of the leading edge of the apex seal curved surface, and rotor housing inner surface deterioration; specifically, severe cracking, chipping, black deposits and chattering."
as to the tip failure, i see the wear pattern in every seal (even the rx2 carbon ive got here), but ive never seen an NA motor that broke. we even roadraced one for 4 seasons, in races up to 3 hours (imagine doing 14 dyno pulls a lap, times 100) with junkyard 100,000 mile seals.
if it was a fatigue failure the would ALL do it, but they don't.
The distortion in the sparkplug area from the heat generated is the key. NA with 200 hp wouldn't provide much of a hump. But Mazda still addressed the problem by severing the housing at the three bosses next to the sparkplugs. Their 24-hr endurance engines than outlasted the Porsches.
But let's double or triple the HP. What do you think happens to the problem area?
Horsepower is heat. Now cutting the housings in the same area as NA engines will probably be catastrophic. Time for a new solution.
Barry
#78
I had a look at this the other day, and found you can nearly double the hole size in passage 5 with a needle file. And I don't think it would be too difficult to fit some sort of restrictor into passage 6. This area just happens to be the hottest part of the housing, and one passage flows too little, the other too much. Surely evening them out to a degree has to help.
I agree with running cold spark plugs. The colder you can get away with without fouling, the better.
Example: Carbed n/a 12a pp with approx 15K miles on the clock with normal electronic distributor ignition. I fitted an MSD box to the leading side and within a few thousand miles the engine wouldn't start due to lack of compression. Once pulled down I found big cracks and very severe high spots in the chrome around the leading holes. Springs and seals were still in ok condition, so it was the housings alone that were the problem.
The root of the problem was the fact that I didn't switch to colder plugs when I fitted the MSD. In hindsight, I should have gone 2 ranges colder.
I sanded the housings flat, removed the MSD, and rebuilt with some new springs & seals. Engine has just clicked over 15k miles again with no trouble.
#79
Moderator

iTrader: (3)
Join Date: Mar 2001
Location: https://www2.mazda.com/en/100th/
Posts: 30,826
Received 2,594 Likes
on
1,842 Posts
j9fd3s,
The distortion in the sparkplug area from the heat generated is the key. NA with 200 hp wouldn't provide much of a hump. But Mazda still addressed the problem by severing the housing at the three bosses next to the sparkplugs. Their 24-hr endurance engines than outlasted the Porsches.
But let's double or triple the HP. What do you think happens to the problem area?
Horsepower is heat. Now cutting the housings in the same area as NA engines will probably be catastrophic. Time for a new solution.
Barry
The distortion in the sparkplug area from the heat generated is the key. NA with 200 hp wouldn't provide much of a hump. But Mazda still addressed the problem by severing the housing at the three bosses next to the sparkplugs. Their 24-hr endurance engines than outlasted the Porsches.
But let's double or triple the HP. What do you think happens to the problem area?
Horsepower is heat. Now cutting the housings in the same area as NA engines will probably be catastrophic. Time for a new solution.
Barry
the competition prep manual from 1979 http://foxed.ca/rx7manual/manuals/comp.manual.pdf
has checks for the same things you are talking about, although its short on answers.
#80
Why aren't EGTs being mentioned outright here?
We are used to very high EGTs under load with an NA race engine, though these engines have very little backpressure in order to work right with the overlap so most of the EGT goes RIGHT OUT THE EXHAUST.
On a turbo rotary there is exhaust backpressure between the turbo and the engine and this REFLECTS THE EGTS INTO THE ENGINE INTERNALS so it is not advisable because of wear, thermal fatique or preignition points to allow the very high EGTs that will be observed at peak power.
You increase the fuel, do not run to retarded timing (possibly higher octane fuel or lower comp rotors if using high boost) and make you have a good ignition system so that there are minimal misfires (unburned air/fuel raises EGTs).
Much of this has been talked about in this thread without mentioning EGTs directly.
What are your EGTs and pre turbo exhaust backpressures under load Barry Bordes?
We are used to very high EGTs under load with an NA race engine, though these engines have very little backpressure in order to work right with the overlap so most of the EGT goes RIGHT OUT THE EXHAUST.
On a turbo rotary there is exhaust backpressure between the turbo and the engine and this REFLECTS THE EGTS INTO THE ENGINE INTERNALS so it is not advisable because of wear, thermal fatique or preignition points to allow the very high EGTs that will be observed at peak power.
You increase the fuel, do not run to retarded timing (possibly higher octane fuel or lower comp rotors if using high boost) and make you have a good ignition system so that there are minimal misfires (unburned air/fuel raises EGTs).
Much of this has been talked about in this thread without mentioning EGTs directly.
What are your EGTs and pre turbo exhaust backpressures under load Barry Bordes?
#81
"Elusive, not deceptive!”

Thread Starter
I had done an mock up similar to your feeler-gauge/apex seal rocking setups barry. Got playing around one night.....
I realize it may be a work around not addressing the heat issue itself, but the though had crossed my mind. What if you were to taper or even radius the ends of the apex seals where they meet the side housings? Whether a one piece or two piece design, it would allow some compliance when the apex seal rocks across the spark plug area. The corner seals should still be doing most of the sealing against the iron, and the sealing surface in the center of the corner seal to the apex seal will still be intact.
Good point Classicauto, but we should address the root cause.
I've gone through the gammot of "typical" mods to the housings. REMedey water pump (fc engine
) ribbed housings, current engine has one "common" ribbed housing, one with clipped dowl lands, and horizontal ribs. Tear down will show how effective each was, but so far, nothing has made a dent in the gigantic amount of heat present in that area. Or I suppose more accurately, that you can make headway in removing the heat from the housing, but until the heat is brought down to a level of manageability on par with the rest of the surface area of the engine, the problem will still exist.
Another possibility for improving pump efficiency would be to set a tighter impeller clearance. The pumps run anywhere from about .080"- .125" . Does anyone know what the minimum should be? My guess would be about .010".
The only mod I've yet to accomplish and still feel really good about the possibilitys of is adding entirely new "webs" around the boss area to allow the heat more places to sink to.
Yea, the more different mods that we could run at the same time the better. I might have to start pushing my last cooling mods to see their limits.
I realize it may be a work around not addressing the heat issue itself, but the though had crossed my mind. What if you were to taper or even radius the ends of the apex seals where they meet the side housings? Whether a one piece or two piece design, it would allow some compliance when the apex seal rocks across the spark plug area. The corner seals should still be doing most of the sealing against the iron, and the sealing surface in the center of the corner seal to the apex seal will still be intact.
Good point Classicauto, but we should address the root cause.
I've gone through the gammot of "typical" mods to the housings. REMedey water pump (fc engine

Another possibility for improving pump efficiency would be to set a tighter impeller clearance. The pumps run anywhere from about .080"- .125" . Does anyone know what the minimum should be? My guess would be about .010".
The only mod I've yet to accomplish and still feel really good about the possibilitys of is adding entirely new "webs" around the boss area to allow the heat more places to sink to.
Yea, the more different mods that we could run at the same time the better. I might have to start pushing my last cooling mods to see their limits.
Sorry I missed your reply earlier.
Barry
#82
"Elusive, not deceptive!”

Thread Starter
Why aren't EGTs being mentioned outright here?
Probably because we are addressing the distortion at the sparkplug. The rest of the housing is relatively less hot (I was going to say cool, but....).
We are used to very high EGTs under load with an NA race engine, though these engines have very little backpressure in order to work right with the overlap so most of the EGT goes RIGHT OUT THE EXHAUST.
On a turbo rotary there is exhaust backpressure between the turbo and the engine and this REFLECTS THE EGTS INTO THE ENGINE INTERNALS so it is not advisable because of wear, thermal fatique or preignition points to allow the very high EGTs that will be observed at peak power.
You increase the fuel, do not run to retarded timing (possibly higher octane fuel or lower comp rotors if using high boost) and make you have a good ignition system so that there are minimal misfires (unburned air/fuel raises EGTs).
Much of this has been talked about in this thread without mentioning EGTs directly.
What are your EGTs and pre turbo exhaust backpressures under load Barry Bordes?
Probably because we are addressing the distortion at the sparkplug. The rest of the housing is relatively less hot (I was going to say cool, but....).
We are used to very high EGTs under load with an NA race engine, though these engines have very little backpressure in order to work right with the overlap so most of the EGT goes RIGHT OUT THE EXHAUST.
On a turbo rotary there is exhaust backpressure between the turbo and the engine and this REFLECTS THE EGTS INTO THE ENGINE INTERNALS so it is not advisable because of wear, thermal fatique or preignition points to allow the very high EGTs that will be observed at peak power.
You increase the fuel, do not run to retarded timing (possibly higher octane fuel or lower comp rotors if using high boost) and make you have a good ignition system so that there are minimal misfires (unburned air/fuel raises EGTs).
Much of this has been talked about in this thread without mentioning EGTs directly.
What are your EGTs and pre turbo exhaust backpressures under load Barry Bordes?
Barry

#83
That is hot. Mine are at 750-800C at 2" from exhaust port under full load. I barely get up to 1000C under lean cruise!
You should try tuning to lower EGTs under load and see how much that helps. It will drop your power a small amount for sure, but it will help durability.
High EGTs will affect every part inside the engine. Yes, the spark plug is hottest part, but it WILL be cooler there as well if you lower your EGTs.
Maybe it would make more sense to you if I referred to it as combustion gas temperature instead of EGTs, and you are just monitoring this CGT from resultant EGTs.
BTW, Mazda documentation shows there is the most heat from the housings being exchanged into the coolant where the peak gas pressure is at (directly between the 3:00 and 6:00 position as viewed from the front with the spark plugs just above and below 3:00 possition). This is why they have more cooling in passage #6 as you show with your test.
The leading spark plug has the highest localized peak surface temperature. It also has a chrome surface that transfers heat very poorly to the steel and then aluminum housing and finally into the coolant.
So it is a great idea to try to control the heat of this localized insulated surface from the inside where the heat is coming from, EGTs will guide you.
You should try tuning to lower EGTs under load and see how much that helps. It will drop your power a small amount for sure, but it will help durability.
High EGTs will affect every part inside the engine. Yes, the spark plug is hottest part, but it WILL be cooler there as well if you lower your EGTs.
Maybe it would make more sense to you if I referred to it as combustion gas temperature instead of EGTs, and you are just monitoring this CGT from resultant EGTs.
BTW, Mazda documentation shows there is the most heat from the housings being exchanged into the coolant where the peak gas pressure is at (directly between the 3:00 and 6:00 position as viewed from the front with the spark plugs just above and below 3:00 possition). This is why they have more cooling in passage #6 as you show with your test.
The leading spark plug has the highest localized peak surface temperature. It also has a chrome surface that transfers heat very poorly to the steel and then aluminum housing and finally into the coolant.
So it is a great idea to try to control the heat of this localized insulated surface from the inside where the heat is coming from, EGTs will guide you.
#84
I run 1850 *F (1010 *C) EGT's on the rear rotor 1 inch from the exhaust port as well past ~6,800 RPM @ 16 PSi. I have tried different timing and AFR's and the EGT's are pretty consistent at high RPM.
I also ran about 900cc's (its probably more since I tested the flow with the car off) of water and the EGT's did not change. Then moved up to 20 PSi and the EGT's did not change. It seems the motor wants to run 1000+ *C EGT at high RPM regardless of tuning or water. I still haven't had time to test it with methanol though and winter is coming so meh.
thewird
I also ran about 900cc's (its probably more since I tested the flow with the car off) of water and the EGT's did not change. Then moved up to 20 PSi and the EGT's did not change. It seems the motor wants to run 1000+ *C EGT at high RPM regardless of tuning or water. I still haven't had time to test it with methanol though and winter is coming so meh.
thewird
#85
meth will lower the EGT's more then water. But I'm surprised you're not seeing as much of a drop with the water you have now marco.
Just a thought as well....
I'm not sure if this aspect has much of a role, but everything little thing helps. When talking about different heat range plugs, we're also covering a number of different tip designs. stock 9's with the "rotary" tip
and then we get into 10's, 10.5's and up, which may be the NGK variety with the single electrode, maybe they are the cheapies with a "normal" single electrode............but what or how much ofa difference does the tip design make to the heat retained in that area or pocket? To me, the stock plugs would seem to reject more of the heat given their shape (or lack of a pocket), but perhaps not?
Does NGK make a "rotary" plug with a range colder then 9?
Just a thought as well....
I'm not sure if this aspect has much of a role, but everything little thing helps. When talking about different heat range plugs, we're also covering a number of different tip designs. stock 9's with the "rotary" tip

Does NGK make a "rotary" plug with a range colder then 9?
#86
Yah, I found it weird, there was no temp drop with the water either. Maybe it might have something to do with my undersized intercooler (on purpose) since its at high RPM? Either way, I rev it to 8k-8.2k for extended periods at Mosport for example and it runs great. I'm happy with my timing and fuel but EGT's just go through the roof at high RPM.
I'll try the meth soon but it always seems I'm busy with other peoples cars or fixing my exhaust leaks. Running 1800+ *F for extended periods does naughty things to manifolds and downpipe flanges.
thewird
I'll try the meth soon but it always seems I'm busy with other peoples cars or fixing my exhaust leaks. Running 1800+ *F for extended periods does naughty things to manifolds and downpipe flanges.
thewird
#88
9:1 or 8.5:1 rotors thewird?
What are your intake air temps? Small intercooler doesn't necessarily mean high IAT, but high IAT will raise EGT.
It does seem odd you cannot lower your EGTs even with water.
On the other hand it is pretty cool your EGTs did not go up when you upped the boost.
What is your turbo/wastegate set up? Trying to get a feel for how much exhaust backpressure here.
Are your EGTs significanly lower below the mentioned 6,800rpm?
I have my turbo/manifold ported to heavily favor wastegate flow over turbo flow and a 60mm wastegate, but the turbo is very restrictive itself.
What are your intake air temps? Small intercooler doesn't necessarily mean high IAT, but high IAT will raise EGT.
It does seem odd you cannot lower your EGTs even with water.

On the other hand it is pretty cool your EGTs did not go up when you upped the boost.

What is your turbo/wastegate set up? Trying to get a feel for how much exhaust backpressure here.
Are your EGTs significanly lower below the mentioned 6,800rpm?
I have my turbo/manifold ported to heavily favor wastegate flow over turbo flow and a 60mm wastegate, but the turbo is very restrictive itself.
#89
"Elusive, not deceptive!”

Thread Starter
meth will lower the EGT's more then water. But I'm surprised you're not seeing as much of a drop with the water you have now marco.
Just a thought as well....
I'm not sure if this aspect has much of a role, but everything little thing helps. When talking about different heat range plugs, we're also covering a number of different tip designs. stock 9's with the "rotary" tip
and then we get into 10's, 10.5's and up, which may be the NGK variety with the single electrode, maybe they are the cheapies with a "normal" single electrode............but what or how much ofa difference does the tip design make to the heat retained in that area or pocket? To me, the stock plugs would seem to reject more of the heat given their shape (or lack of a pocket), but perhaps not?
Does NGK make a "rotary" plug with a range colder then 9?
Just a thought as well....
I'm not sure if this aspect has much of a role, but everything little thing helps. When talking about different heat range plugs, we're also covering a number of different tip designs. stock 9's with the "rotary" tip

Does NGK make a "rotary" plug with a range colder then 9?
Barry
#90
9:1 or 8.5:1 rotors thewird?
What are your intake air temps? Small intercooler doesn't necessarily mean high IAT, but high IAT will raise EGT.
It does seem odd you cannot lower your EGTs even with water.
On the other hand it is pretty cool your EGTs did not go up when you upped the boost.
What is your turbo/wastegate set up? Trying to get a feel for how much exhaust backpressure here.
Are your EGTs significanly lower below the mentioned 6,800rpm?
I have my turbo/manifold ported to heavily favor wastegate flow over turbo flow and a 60mm wastegate, but the turbo is very restrictive itself.
What are your intake air temps? Small intercooler doesn't necessarily mean high IAT, but high IAT will raise EGT.
It does seem odd you cannot lower your EGTs even with water.

On the other hand it is pretty cool your EGTs did not go up when you upped the boost.

What is your turbo/wastegate set up? Trying to get a feel for how much exhaust backpressure here.
Are your EGTs significanly lower below the mentioned 6,800rpm?
I have my turbo/manifold ported to heavily favor wastegate flow over turbo flow and a 60mm wastegate, but the turbo is very restrictive itself.
My turbo is the A-Spec 500R-SP and short runner manifold with a collected Tial 44mm wastegate. I actually have an exhaust backpressure sensor in my exhaust which I completely forgot about when tuning with water. Running 16-17 PSi my exhaust backpressure (after new Amuse titanium exhaust) was about ~3 PSi. After upping the boost to 20 PSi, the exhaust then has ~5 PSi of backpressure.
To note the old Racing Beat exhaust had over 10 PSi of backpressure at 16-17 PSi.
thewird
#91
"Elusive, not deceptive!”

Thread Starter
9:1 compression rotors. This is true AIT's are pretty stable at ~30*C even after a few laps on the track but it is a little cold outside lately.
My turbo is the A-Spec 500R-SP and short runner manifold with a collected Tial 44mm wastegate. I actually have an exhaust backpressure sensor in my exhaust which I completely forgot about when tuning with water. Running 16-17 PSi my exhaust backpressure (after new Amuse titanium exhaust) was about ~3 PSi. After upping the boost to 20 PSi, the exhaust then has ~5 PSi of backpressure.
Wird,
Where are you taking the backpressure reading from? Preturbo?
Weren't you running a cast HKS manifold before this new tubular manifold.
How much egt drop did you see from going ; no water-> water-> tubular manifold-> Amuse exhaust?
It sounds like you saying it remained about the same.
To note the old Racing Beat exhaust had over 10 PSi of backpressure at 16-17 PSi.
thewird
My turbo is the A-Spec 500R-SP and short runner manifold with a collected Tial 44mm wastegate. I actually have an exhaust backpressure sensor in my exhaust which I completely forgot about when tuning with water. Running 16-17 PSi my exhaust backpressure (after new Amuse titanium exhaust) was about ~3 PSi. After upping the boost to 20 PSi, the exhaust then has ~5 PSi of backpressure.
Wird,
Where are you taking the backpressure reading from? Preturbo?
Weren't you running a cast HKS manifold before this new tubular manifold.
How much egt drop did you see from going ; no water-> water-> tubular manifold-> Amuse exhaust?
It sounds like you saying it remained about the same.
To note the old Racing Beat exhaust had over 10 PSi of backpressure at 16-17 PSi.
thewird
#92
Wird,
Where are you taking the backpressure reading from? Preturbo?
Weren't you running a cast HKS manifold before this new tubular manifold.
How much egt drop did you see from going ; no water-> water-> tubular manifold-> Amuse exhaust?
It sounds like you saying it remained about the same.
Where are you taking the backpressure reading from? Preturbo?
Weren't you running a cast HKS manifold before this new tubular manifold.
How much egt drop did you see from going ; no water-> water-> tubular manifold-> Amuse exhaust?
It sounds like you saying it remained about the same.
thewird
#93
Senior Member

Join Date: Nov 2008
Location: Czech republic
Posts: 357
Likes: 0
Received 0 Likes
on
0 Posts
Backpressure is taken after the turbo just before the resonator. No, I never ran an HKS manifold. What I'm saying is there was no EGT drop at all. When I compare EGT's I only compare high RPM EGT's at high gears (4th,5th) since the lower stuff varies too much between single pulls. The EGT's steadily climb as RPM goes up though.
thewird
thewird
#95
"Elusive, not deceptive!”

Thread Starter
It would seem that with a simple gauge this pressure would be an average of the pressure that the exhaust port would experience,
not the high pressure pulse and then a bleed down through the turbine wheel.
Barry
#96
Senior Member

Join Date: Nov 2008
Location: Czech republic
Posts: 357
Likes: 0
Received 0 Likes
on
0 Posts
https://www.rx7club.com/single-turbo-rx-7s-23/15-000-miles-twin-t04s-daily-driver-450719/page3/
read it throught-some interesting info from RICE
https://www.rx7club.com/single-turbo-rx-7s-23/wastegate-dynamics-greatly-effect-backpressure-683202/
again.
Simply said, once RPMs go over max torque-max VE%, and mainly after wastegate opens-EBP goes rapidly UP....
#97
Senior Member

Join Date: Nov 2008
Location: Czech republic
Posts: 357
Likes: 0
Received 0 Likes
on
0 Posts
I see what you mean, pressure after turbine is also important-as low as possible and it seems its ok in your case...
#98
On flats

iTrader: (29)
Join Date: Oct 2004
Location: Albuquerque
Posts: 1,379
Likes: 0
Received 0 Likes
on
0 Posts
Originally Posted by Liborek
. . . after wastegate opens-EBP goes rapidly UP.
I disagree that pressure in the exhaust manifold will increase after opening the wastegate. I've read the threads that you mention, but the logic doesn't add up.
There is no way that introducing a massive hole (opening a wastegate) to a pressurized vessel (exhaust manifold) will increase pressure.
#99
Senior Member

Join Date: Nov 2008
Location: Czech republic
Posts: 357
Likes: 0
Received 0 Likes
on
0 Posts
I don't mean to be combative, so please read this as just a technical exchange, not an insult.
I disagree that pressure in the exhaust manifold will increase after opening the wastegate. I've read the threads that you mention, but the logic doesn't add up.
There is no way that introducing a massive hole (opening a wastegate) to a pressurized vessel (exhaust manifold) will increase pressure.
I disagree that pressure in the exhaust manifold will increase after opening the wastegate. I've read the threads that you mention, but the logic doesn't add up.
There is no way that introducing a massive hole (opening a wastegate) to a pressurized vessel (exhaust manifold) will increase pressure.
I also have to have re-read it many times, but this is hardly to denied with datalogs in front of us...
#100
On flats

iTrader: (29)
Join Date: Oct 2004
Location: Albuquerque
Posts: 1,379
Likes: 0
Received 0 Likes
on
0 Posts
What the "simple equation" fails to take into account is the inertia of the turbine and compessor. The reason we don't run small turbines and huge wastegates is for boost/EMP stability.
With tiny turbines, the inertia is greatly reduced. Therefore, when the wastegate opens, it is quick to slow down. As it slows, boost drops causing the wastegate to close again. At this point, the engine will be turning more quickly than when the wastegate first opened. Because it's turning more quickly, it is making more power and therefore more and hotter exhaust. For this reason, when the wastegate closes to help pick boost back up, we see a huge spike in EMP.
Thinking of it from a slightly different approach. . .what is producing the EMP? The engine is, right? How is the engine going to suddenly (literally instantly as required by your posit) produce a more highly pressurized exhaust charge in response to a wastegate opening downstream? There is no physical way for that to happen.
With tiny turbines, the inertia is greatly reduced. Therefore, when the wastegate opens, it is quick to slow down. As it slows, boost drops causing the wastegate to close again. At this point, the engine will be turning more quickly than when the wastegate first opened. Because it's turning more quickly, it is making more power and therefore more and hotter exhaust. For this reason, when the wastegate closes to help pick boost back up, we see a huge spike in EMP.
Thinking of it from a slightly different approach. . .what is producing the EMP? The engine is, right? How is the engine going to suddenly (literally instantly as required by your posit) produce a more highly pressurized exhaust charge in response to a wastegate opening downstream? There is no physical way for that to happen.