Welding!
#1
Welding!
Ok, so everyone has the Tig and Mig welders, plasma cutters and whatnot.
I wish I had skills in that, so I bring you this:

I used a laser welder on this. I am pretty good with laser and phaser weldings. Would stepping up to Tig/Mig be too hard?
Sorry about the picture not being RX7 related. I wish I could find the picture of my throttle cable I had to cast and weld.
Anyways, here is some welding, on the micro level
I wish I had skills in that, so I bring you this:

I used a laser welder on this. I am pretty good with laser and phaser weldings. Would stepping up to Tig/Mig be too hard?
Sorry about the picture not being RX7 related. I wish I could find the picture of my throttle cable I had to cast and weld.
Anyways, here is some welding, on the micro level

#2
Banned. I got OWNED!!!
Join Date: Dec 2007
Location: paradise Florida
Posts: 946
Likes: 0
Received 0 Likes
on
0 Posts
defiantly!
mig welding is a piece of cake, arc welding is a little harder, and tig welding is a little harder still.
as long as you get a good amount of practice in, you'll see your skills improve very quickly.
mig welding is a piece of cake, arc welding is a little harder, and tig welding is a little harder still.
as long as you get a good amount of practice in, you'll see your skills improve very quickly.
#3
Engine, Not Motor

iTrader: (1)
Join Date: Feb 2001
Location: London, Ontario, Canada
Posts: 29,789
Likes: 0
Received 108 Likes
on
91 Posts
What is it? Looks like a pocket knife?
I've never operated a laser welder but once you have a few hours with the TIG torch under your belt you should be able to easily make welds like that using GTAW.
MIG welding is a bit of an oddball. It is very easy to make awesome looking MIG welds that are totally useless.
If you want to learn welding properly, start with arc welding or a set of torches. Arc welding will tech you electrode control and keeping a steady pattern/travel speed. A set of torches will prepare you for TIG and set the foundation for all other forums of welding.
MIG really isn't a very good way to learn as the process offers less feedback. The only thing you learn is how to set the machine properly and maintain a gun pattern.
I've never operated a laser welder but once you have a few hours with the TIG torch under your belt you should be able to easily make welds like that using GTAW.
MIG welding is a bit of an oddball. It is very easy to make awesome looking MIG welds that are totally useless.
If you want to learn welding properly, start with arc welding or a set of torches. Arc welding will tech you electrode control and keeping a steady pattern/travel speed. A set of torches will prepare you for TIG and set the foundation for all other forums of welding.
MIG really isn't a very good way to learn as the process offers less feedback. The only thing you learn is how to set the machine properly and maintain a gun pattern.
#4
What is it? Looks like a pocket knife?
I've never operated a laser welder but once you have a few hours with the TIG torch under your belt you should be able to easily make welds like that using GTAW.
MIG welding is a bit of an oddball. It is very easy to make awesome looking MIG welds that are totally useless.
If you want to learn welding properly, start with arc welding or a set of torches. Arc welding will tech you electrode control and keeping a steady pattern/travel speed. A set of torches will prepare you for TIG and set the foundation for all other forums of welding.
MIG really isn't a very good way to learn as the process offers less feedback. The only thing you learn is how to set the machine properly and maintain a gun pattern.
I've never operated a laser welder but once you have a few hours with the TIG torch under your belt you should be able to easily make welds like that using GTAW.
MIG welding is a bit of an oddball. It is very easy to make awesome looking MIG welds that are totally useless.
If you want to learn welding properly, start with arc welding or a set of torches. Arc welding will tech you electrode control and keeping a steady pattern/travel speed. A set of torches will prepare you for TIG and set the foundation for all other forums of welding.
MIG really isn't a very good way to learn as the process offers less feedback. The only thing you learn is how to set the machine properly and maintain a gun pattern.
I found the picture of the old throttle cable. I used a bicycle brake line for the cable, and I molded/cast the stock 1st gen cable end.

#5
Red Pill Dealer

iTrader: (10)
I always wanted to try laser welding. I microweld for work (actually welding looking through a microscope). It's basically a TIG set-up.

Trending Topics
#10
Red Pill Dealer

iTrader: (10)
#11
rotory addict
Join Date: Aug 2009
Location: Burns/Hines Oregon
Posts: 14
Likes: 0
Received 0 Likes
on
0 Posts
i have been taking welding in high school and i am one of the best in my class and i prefer stick arc but i am good with mig i suck with tig and i am ok with oxy-acetylene i have my own arc welder at home so i use it allot and i think that arc is more versitile then mig because you can use differnt rods for differnt jobs so yea i will try to take some pics of what i do and post them on my profile
#12
On flats

iTrader: (29)
Join Date: Oct 2004
Location: Albuquerque
Posts: 1,379
Likes: 0
Received 0 Likes
on
0 Posts
the razor by itself is easy. Aaron challenged anyone to do it to a railroad track. Similarly, any LARGE piece of steel will do. . . basically, something that can take no heat (blade) to a massive heat sink (rail or big piece of plate). The heat modulation will be extraordinarily challenging because the blade will just want to melt and blow out. Nothing a good amount of pre-heating shouldn't be able to fix.
#14
Red Pill Dealer

iTrader: (10)
I'd like to see the aluminum foil. That would make you a way better aluminum welder than me. I suck at it.
With the micro TIG welding thin to thick is easy. I've already done plenty of it. I will try the blade to a large chunk of steel this next week. I don't think I can come up with railroad track.
With the micro TIG welding thin to thick is easy. I've already done plenty of it. I will try the blade to a large chunk of steel this next week. I don't think I can come up with railroad track.
#15
Engine, Not Motor

iTrader: (1)
Join Date: Feb 2001
Location: London, Ontario, Canada
Posts: 29,789
Likes: 0
Received 108 Likes
on
91 Posts
Once you see how the foil is done, it's actually not hard to do. I forgot to bring the foil to the shop yesterday so I'll just tell the secret. 
Clamp the two pieces of foil in a vice with the edges you want to join facing straight up and about 1MM higher then the jaws of the vice. Set the welder to AC, mostly cleaning and at it's lowest current setting. Strike your arc about an inch from the aluminum on the vice and then rapidly flick the torch down the foil with the current as low as possible.

Clamp the two pieces of foil in a vice with the edges you want to join facing straight up and about 1MM higher then the jaws of the vice. Set the welder to AC, mostly cleaning and at it's lowest current setting. Strike your arc about an inch from the aluminum on the vice and then rapidly flick the torch down the foil with the current as low as possible.
#17
Red Pill Dealer

iTrader: (10)
Not exactly a railroad track but here you go.

Backside

I would really like to try that LASER welding some time. I've seen impressive examples.
Where's yours?

Backside

I would really like to try that LASER welding some time. I've seen impressive examples.
the razor by itself is easy. Aaron challenged anyone to do it to a railroad track. Similarly, any LARGE piece of steel will do. . . basically, something that can take no heat (blade) to a massive heat sink (rail or big piece of plate). The heat modulation will be extraordinarily challenging because the blade will just want to melt and blow out. Nothing a good amount of pre-heating shouldn't be able to fix.
#19
Red Pill Dealer

iTrader: (10)
I think it's a Novatech. I've found it's more the microscope that makes the difference though they make a really good power supply. We've made the scope portable (stand with wheels and a longer arm) and I have used just the scope with a Thermalarc 110 portable supply with satisfactory results. Sometimes things are just too damn big to take to the table but the repair dictates the micro-welders use. I generally use a .020" tungsten and .020" and .015" welding wire.
It also has a high intensity fiber optic light that allows you to see through the shader (there's a shader in a flip out door under the scope so I don't need a helmet or glasses) without an arc going. Though the arc makes everything real easy to see.
Pic of me with a piece two big for a table but not a cart.

.020", .040", and .062" tungstens.

The torch.

Another example.
It also has a high intensity fiber optic light that allows you to see through the shader (there's a shader in a flip out door under the scope so I don't need a helmet or glasses) without an arc going. Though the arc makes everything real easy to see.
Pic of me with a piece two big for a table but not a cart.

.020", .040", and .062" tungstens.

The torch.

Another example.
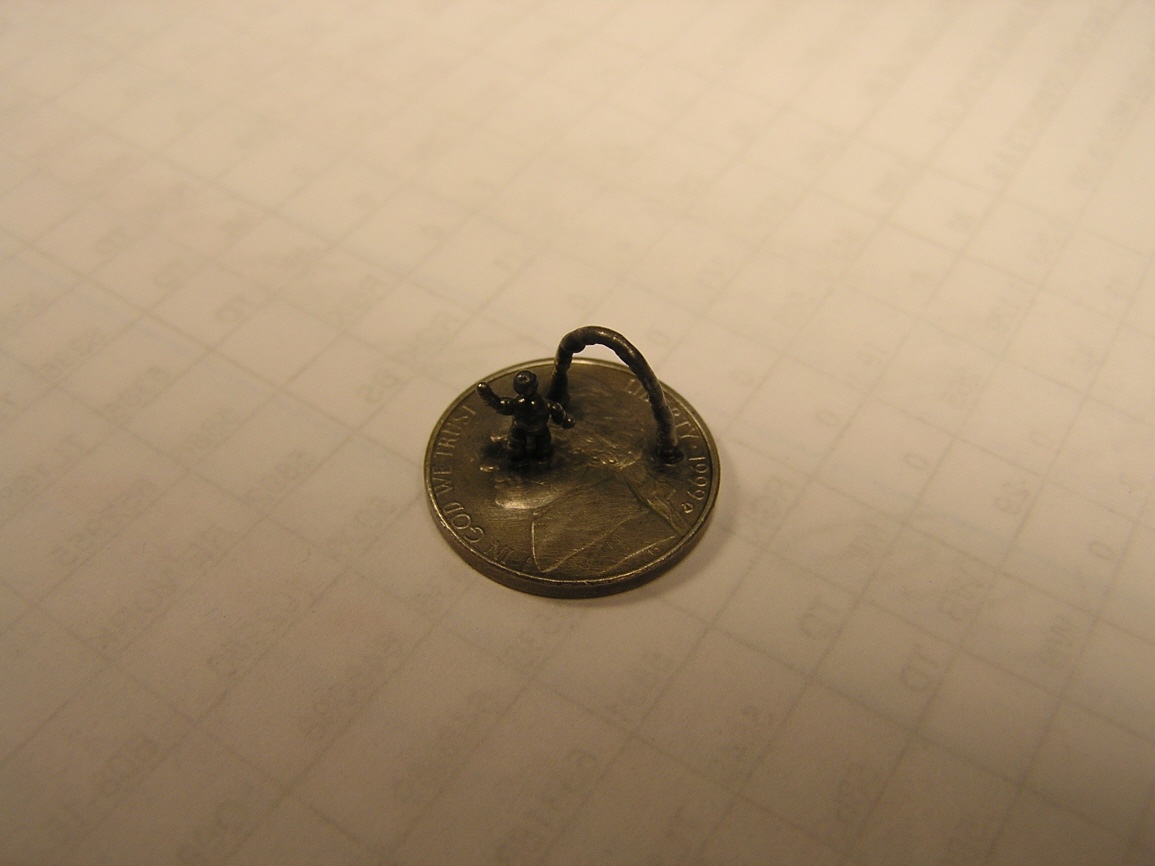
#23
i like to challange myself evey once and a while with welding. so try this (its always fun), weld a soda can. not two of them end to end. but cut one in half and weld it back together.
and this includes filler metal getting the dime look. without using filler its fusing, not welding...
i have never used a "micro welder". but i have done similar, micro welding is just TIG welding to a very small degree, you can accomplish the same with add-on magnification lenses to your helmet if you have good eyesight already. I have used a .040 tungsten in a normal sized TIG. but thats the smallest ive seen for a regular torch...
tonyd89, did you build the man and arch with just using filler? if so, VERY NICE! i use to practice arc/filler control with aluminum by building a tower strait up with little beads in school. but i do most welding at home on my Lincoln 175 squarewave. so getting low amp's and a steady arch when easing of the pedal can be tricky... i should step it up to a big boy welder real soon.
and this includes filler metal getting the dime look. without using filler its fusing, not welding...
i have never used a "micro welder". but i have done similar, micro welding is just TIG welding to a very small degree, you can accomplish the same with add-on magnification lenses to your helmet if you have good eyesight already. I have used a .040 tungsten in a normal sized TIG. but thats the smallest ive seen for a regular torch...
tonyd89, did you build the man and arch with just using filler? if so, VERY NICE! i use to practice arc/filler control with aluminum by building a tower strait up with little beads in school. but i do most welding at home on my Lincoln 175 squarewave. so getting low amp's and a steady arch when easing of the pedal can be tricky... i should step it up to a big boy welder real soon.