Supercharger for an FD?
#26
Senior Member

Join Date: Mar 2003
Location: new york city
Posts: 283
Likes: 0
Received 0 Likes
on
0 Posts
for some reason people think that superchargers are safer than a turbo? i for one think this is not true. superchargers are constantly turning this makes it give you boost fast. but you have to realize that this also makes constant preasure maybe not much but when your driving slow its making some. wich will infact shorten the life of the motor and also cause you to guzzle gas. also a turbo dosent always have to be boosting at low rpm's you can drive around slow not putting strain on the motor. you actually have a choice if you want to race or cruise. in an fd i think it would severly affect the life of the motor?
#27
Furious Ass-Monkey

Join Date: May 2005
Location: Palo Alto, CA
Posts: 207
Likes: 0
Received 0 Likes
on
0 Posts
Originally Posted by rotary
for some reason people think that superchargers are safer than a turbo? i for one think this is not true. superchargers are constantly turning this makes it give you boost fast. but you have to realize that this also makes constant preasure maybe not much but when your driving slow its making some. wich will infact shorten the life of the motor and also cause you to guzzle gas. also a turbo dosent always have to be boosting at low rpm's you can drive around slow not putting strain on the motor. you actually have a choice if you want to race or cruise. in an fd i think it would severly affect the life of the motor?
#28
Packaging is the reason there are no ICs on factory superchargers. A "V" engine with a V mounted supercharger is hard to package with a IC.
Turbos do present a exhaust flow restriction but the power they pump into the engine more than offsets the restriction.
It's only a power restriction until the turbine begins producing boost.
Your comparison is kind of irrelevant, because once the turbine begins producing boost, there are no losses.
Think of it this way. You have an NA engine making X hp. IF you put a turbo in the exhaust path, but do not plumb the boost into the intake, you lose power. IF you put a blower on the accessory belt but do not plumb it into the intake, you lose power. IF you plumb either back into the intake, you gain a lot of power, but that still doesnt mean that either is free to operate. IF you had a way to produce boost into the intake (say, via an external air compressor) that did not require energy from the engine to operate, well you'd make more power per PSI than either the turbo OR the blower. Energy is not free, it has to come from somewhere.
Because a supercharger must be mounted as close to the intake tract as close as possible due to its design, which often negates the possibility to install an IC (this is one of the reasons why air/water ICs are often used, because they don't have the same space requirements as an air/air IC). You'll note that the vast majority of bolt-on SC applications only produce small boost pressures, to keep the intake temps from soaring.
The most commonly used SC is a "Roots" type blower, which doesn't actually internally compress the intake charge like centrifugal or screw-type SCs. In very simplistic terms, it depends on "compounding" the intake charge in the intake tract itself (the reason why it must be mounted as close as possible to the intake, negating an IC installation) to produce boost, which generates more heat.
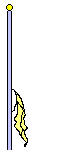
I'll say it again. Air heats up the same amount when compressed at a given pressure level, regardless of the method used to compress. The only differential arises when the materials doing the compressing are at different temperatures themselves...a compressor wheel and housing connected to a hot exhaust wheel/housing/manifold, or a compressor wheel and housing connected to slightly warm intake manifold. It's common sense here.
A street-based SC installation will usually require an electrically-operated clutch of some sort to allow the engine to generate enough speed to offset the parasitic drag at very low rpms, as well as disconnect it at cruising rpm to cut drag and increase efficiency;
those units aren't very light. The blower unit is can also be quite heavy, due to the necessary construction for structural integrity to withstand belt torque and high rpms.
superchargers are constantly turning this makes it give you boost fast.

but you have to realize that this also makes constant preasure maybe not much but when your driving slow its making some. wich will infact shorten the life of the motor and also cause you to guzzle gas

also a turbo dosent always have to be boosting at low rpm's you can drive around slow not putting strain on the motor. you actually have a choice if you want to race or cruise
#30
Rotary Enthusiast

Join Date: Jan 2005
Location: orlando/st. petersburg
Posts: 769
Likes: 0
Received 0 Likes
on
0 Posts
To the starter of this thread,
A. Buy a rx6 kit which spools like stock with better power and reliability.
B. Run a single turbo with a t3 exhaust side.
A. Buy a rx6 kit which spools like stock with better power and reliability.
B. Run a single turbo with a t3 exhaust side.

#31
I haven't read the whole thing but as a Mechanical Engineer I can certainly tell you that the heat introduced to the intake charge by forced induction is due to the compression of the air more than anything else.
The heat added by the compressor shaft/impeller is negligible compared to the heat due to compression itself, which can be aproximated as adiabatic (no heat exchange) due to the very short time the air is in contact to the compressor wheel or other components.
This is true wether it's a turbocharger or a supercharger but to this adiabatic compression heat we need to add heat due to compressor thermal and volumetric inefficiencies. The less efficient the compressor, the more heat is added due to an increase in the velocity of the air molecules due to turbulence. This is where the turbocharger's higher efficiency comes into play. For any given boost pressure, a more effcient compressor will output air at lower temperature than the less efficient one.
Here's a nice calculator for you to play with: http://www.stealth316.com/2-turbotemp.htm
Now, we are discussing instant boost superchargers here, correct? This rules out centriugal ones that work at higher rpms like turbos and leaves us with positive displacement superchargers which generally are less eficient than turbochargers. This lower efficiency is what results in higher compressor outlet tempratures. Some lysholm or whipple screw-type positive displacement superchargers can be as efficient as turbochargers but here's where parasitic losses show their ugly face.
Superchargers are driven off the engine's output shaft, via pulley and belt, through a small gearset. 100% of the power used by the supercharger comes from the power produced by the engine, in other words, we lose significant power to produce more power. Even at the same efficiency the supercharger will produce less power given similar boost and flow than the equvalent turbocharger.
Turbochargers harness the kinetic energy in the very hot, high velocity, expanding exhaust gases to spin the compressor. Most of the power used by the turbo comes from this kinetic energy recycled form the exhaust; some comes from the pressure difference between compressor inlet and outlet thus the turbocharger also robs the engine of some power due to the backpressure created (this is one reason a bigger exhaust pipe is better). The engine power robbed by the turbocharger is much less than the supercharger's though, due to the inherent energy recycling of otherwise wasted heat in the exhaust gases.
I think this is my longest post ever!
The heat added by the compressor shaft/impeller is negligible compared to the heat due to compression itself, which can be aproximated as adiabatic (no heat exchange) due to the very short time the air is in contact to the compressor wheel or other components.
This is true wether it's a turbocharger or a supercharger but to this adiabatic compression heat we need to add heat due to compressor thermal and volumetric inefficiencies. The less efficient the compressor, the more heat is added due to an increase in the velocity of the air molecules due to turbulence. This is where the turbocharger's higher efficiency comes into play. For any given boost pressure, a more effcient compressor will output air at lower temperature than the less efficient one.
Here's a nice calculator for you to play with: http://www.stealth316.com/2-turbotemp.htm
Now, we are discussing instant boost superchargers here, correct? This rules out centriugal ones that work at higher rpms like turbos and leaves us with positive displacement superchargers which generally are less eficient than turbochargers. This lower efficiency is what results in higher compressor outlet tempratures. Some lysholm or whipple screw-type positive displacement superchargers can be as efficient as turbochargers but here's where parasitic losses show their ugly face.
Superchargers are driven off the engine's output shaft, via pulley and belt, through a small gearset. 100% of the power used by the supercharger comes from the power produced by the engine, in other words, we lose significant power to produce more power. Even at the same efficiency the supercharger will produce less power given similar boost and flow than the equvalent turbocharger.
Turbochargers harness the kinetic energy in the very hot, high velocity, expanding exhaust gases to spin the compressor. Most of the power used by the turbo comes from this kinetic energy recycled form the exhaust; some comes from the pressure difference between compressor inlet and outlet thus the turbocharger also robs the engine of some power due to the backpressure created (this is one reason a bigger exhaust pipe is better). The engine power robbed by the turbocharger is much less than the supercharger's though, due to the inherent energy recycling of otherwise wasted heat in the exhaust gases.
I think this is my longest post ever!

Last edited by neit_jnf; 01-03-06 at 07:32 PM.
#32
Senior Member

Join Date: Dec 2003
Location: Stanford, CA
Posts: 260
Likes: 0
Received 0 Likes
on
0 Posts
Hello-
No. That's not true.
I'll say it again, too: no. It's not common sense... it's wrong.
Sorry, I don't mean to be an ***, but you clearly don't understand the physics of compressors. In particular, you do not understand how inefficiency comes into play.
Let me start at the beginning... if you have an ideal compression stage, then you are correct. This is called an 100% adiabatic compression... it's where no heat enters nor leaves the gas as it's compressed. The gas will increase in temperature, and any way you do it, it will increase the same amount for the same pressure increase.
Now, here's the problem: neither turbochargers nor positive displacement ("roots") superchargers nor centrifugal superchargers are adiabatic. They all have an adiabatic efficiency less than 100%. Look at compressor maps for any of the above... NONE of them EVER have a 100% efficient operating range. Now, where does that inefficiency go? It goes into heating up the intake charge. In fact, it's directly proportional:
(actual temp change) = (ideal temp change) / (compressor's adiabatic efficiency)
This equation is nothing new... I'm no genius by stating it here. It's in just every primer to forced induction design you'll find...
So, a 75% efficient compressor would have 2/3 the temperature increase that a 50% efficient compressor would. Those are about the efficiencies of centrifugal compressors (turbos and centrifugal superchargers) and positive displacement compressors (roots superchargers).
Now, there is one more thing to consider... heat transfer. Superchargers are often far removed from exhaust systems. Turbos, however, are *closer*. However, and here's the common misnomer, this isn't *that* big of a deal. In common practice, there's not that much of a problem with turbos getting exhaust heat... the amount is FAR less than the amount you get just from compression alone. In fact, for most practical purposes, it's basically ignored. Again, if you don't believe me, go look it up in the books.
If you want a fast-n-easy online reference, there's a decent writeup here: http://www.stealth316.com/2-adiabat1.htm It even has a calculator so you can plug in a few numbers.
There's one more point we need to clarify: centrifugal superchargers are NOT the answer to our prayers. First, let's clarify what we mean by "lag." There are two problems to think about:
1. The transient problem: when you shove the gas down, it takes time for stuff to spool. Superchargers have lag, too, as the gases in the piping do need to be compressed, but it is much less than turbos.
2. The steady-state problem: if you hold your foot down, there are some rpm at which you simply cannot make boost no matter how long you wait. In particular, low rpm have problems.
Positive displacement superchargers are far superior to turbos in both of these regards, but at the expense of poor efficiency (i.e. less power AND more temperature rise). Turbos take a big hit to transient problem and a modest (although not yet crippling) hit to the steady-state low rpm problem, but give awesome efficiency.
Centrifugal superchargers have the efficiency of turbos, the transient response of positive displacement superchargers, but the steady-state low rpm response is absolutely pathetic. It blows, big time.... it's WAY worse than turbos. They are only really popular on big, untuned muscle cars. They don't help with the already-great low end, but make up for poor breathing on the high end with boost. If you think your single turbo has a peaky powerband, then you DEFINATELY don't want a centrifugal supercharger :-).
Now, you may ask, why the hell does this happen? Well, let's go back to the basics...
"Positive displacement" means that the volumetric flow is proportional to the shaft speed. This means that the volume of air a roots supercharger pushes through is proportional to engine speed. This gives torque curves that are kinda/sorta flat from about zero rpm on up. This is desirable. The pressure rise from this pumping is incidental... it's a by-product of the pumping of a fixed volumetric flow.
"Centrifugal" pumps, in many ways, are the opposite of positive displacement ones. Rather than link volumetric flow to shaft speed, they link pressure increase to shaft speed. To be precise, the pressure rise is proportional to the square of shaft speed. Now, if we fix the shaft speed to the engine speed like a centrifugal supercharger, we have a really sucky setup. Let's say we make it operate in its efficient range at some pressure at 4000rpm engine speed. Then, at 2000rpm, it makes just about no boost, and at 8000rpm with some form of boost control, it's *way* outside its efficient range.
Turbos have a slick way of getting around this problem... rather than link compressor shaft speed to engine speed, they link it to another centrifugal pump that happens to be running in reverse (i.e. the exhaust turbine). Now, the backpressure on the exhaust is related to a shaft speed, which is in turn related to the boost pressure on the intake. So, this means that the intake boost is roughly proportional to the exhaust backpressure, so it's possible to get a constant boost pressure at a wide range of engine rpm. It also means that the turbo speed is roughly constant with respect to boost pressure, not engine speed. If you listen to the whine given by a centrifugal supercharger vs. a turbo, then this should make perfect sense :-).
Of course, at low rpm, you can't pump enough exhaust to generate enough backpressure on the turbine. But, it's still way better than a centrifugal supercharger. Plus, wastegates are kinda free... when you vent exhaust around the turbos, you aren't losing any power.
Take care,
Shad
Originally Posted by RotaryResurrection
A turbo puts more heat into the air at the same psi versus a blower. There is no way around that fact...air heats up the same amount at a given pressure regardless of the method of pressurizing it;
Originally Posted by RotaryResurrection
I'll say it again. Air heats up the same amount when compressed at a given pressure level, regardless of the method used to compress. The only differential arises when the materials doing the compressing are at different temperatures themselves...a compressor wheel and housing connected to a hot exhaust wheel/housing/manifold, or a compressor wheel and housing connected to slightly warm intake manifold. It's common sense here.
Sorry, I don't mean to be an ***, but you clearly don't understand the physics of compressors. In particular, you do not understand how inefficiency comes into play.
Let me start at the beginning... if you have an ideal compression stage, then you are correct. This is called an 100% adiabatic compression... it's where no heat enters nor leaves the gas as it's compressed. The gas will increase in temperature, and any way you do it, it will increase the same amount for the same pressure increase.
Now, here's the problem: neither turbochargers nor positive displacement ("roots") superchargers nor centrifugal superchargers are adiabatic. They all have an adiabatic efficiency less than 100%. Look at compressor maps for any of the above... NONE of them EVER have a 100% efficient operating range. Now, where does that inefficiency go? It goes into heating up the intake charge. In fact, it's directly proportional:
(actual temp change) = (ideal temp change) / (compressor's adiabatic efficiency)
This equation is nothing new... I'm no genius by stating it here. It's in just every primer to forced induction design you'll find...
So, a 75% efficient compressor would have 2/3 the temperature increase that a 50% efficient compressor would. Those are about the efficiencies of centrifugal compressors (turbos and centrifugal superchargers) and positive displacement compressors (roots superchargers).
Now, there is one more thing to consider... heat transfer. Superchargers are often far removed from exhaust systems. Turbos, however, are *closer*. However, and here's the common misnomer, this isn't *that* big of a deal. In common practice, there's not that much of a problem with turbos getting exhaust heat... the amount is FAR less than the amount you get just from compression alone. In fact, for most practical purposes, it's basically ignored. Again, if you don't believe me, go look it up in the books.
If you want a fast-n-easy online reference, there's a decent writeup here: http://www.stealth316.com/2-adiabat1.htm It even has a calculator so you can plug in a few numbers.
There's one more point we need to clarify: centrifugal superchargers are NOT the answer to our prayers. First, let's clarify what we mean by "lag." There are two problems to think about:
1. The transient problem: when you shove the gas down, it takes time for stuff to spool. Superchargers have lag, too, as the gases in the piping do need to be compressed, but it is much less than turbos.
2. The steady-state problem: if you hold your foot down, there are some rpm at which you simply cannot make boost no matter how long you wait. In particular, low rpm have problems.
Positive displacement superchargers are far superior to turbos in both of these regards, but at the expense of poor efficiency (i.e. less power AND more temperature rise). Turbos take a big hit to transient problem and a modest (although not yet crippling) hit to the steady-state low rpm problem, but give awesome efficiency.
Centrifugal superchargers have the efficiency of turbos, the transient response of positive displacement superchargers, but the steady-state low rpm response is absolutely pathetic. It blows, big time.... it's WAY worse than turbos. They are only really popular on big, untuned muscle cars. They don't help with the already-great low end, but make up for poor breathing on the high end with boost. If you think your single turbo has a peaky powerband, then you DEFINATELY don't want a centrifugal supercharger :-).
Now, you may ask, why the hell does this happen? Well, let's go back to the basics...
"Positive displacement" means that the volumetric flow is proportional to the shaft speed. This means that the volume of air a roots supercharger pushes through is proportional to engine speed. This gives torque curves that are kinda/sorta flat from about zero rpm on up. This is desirable. The pressure rise from this pumping is incidental... it's a by-product of the pumping of a fixed volumetric flow.
"Centrifugal" pumps, in many ways, are the opposite of positive displacement ones. Rather than link volumetric flow to shaft speed, they link pressure increase to shaft speed. To be precise, the pressure rise is proportional to the square of shaft speed. Now, if we fix the shaft speed to the engine speed like a centrifugal supercharger, we have a really sucky setup. Let's say we make it operate in its efficient range at some pressure at 4000rpm engine speed. Then, at 2000rpm, it makes just about no boost, and at 8000rpm with some form of boost control, it's *way* outside its efficient range.
Turbos have a slick way of getting around this problem... rather than link compressor shaft speed to engine speed, they link it to another centrifugal pump that happens to be running in reverse (i.e. the exhaust turbine). Now, the backpressure on the exhaust is related to a shaft speed, which is in turn related to the boost pressure on the intake. So, this means that the intake boost is roughly proportional to the exhaust backpressure, so it's possible to get a constant boost pressure at a wide range of engine rpm. It also means that the turbo speed is roughly constant with respect to boost pressure, not engine speed. If you listen to the whine given by a centrifugal supercharger vs. a turbo, then this should make perfect sense :-).
Of course, at low rpm, you can't pump enough exhaust to generate enough backpressure on the turbine. But, it's still way better than a centrifugal supercharger. Plus, wastegates are kinda free... when you vent exhaust around the turbos, you aren't losing any power.
Take care,
Shad
#36
It Just Feels Right

Off topic, but let me just throw out a bizarre idea I've had since I was knee high to a married grasshopper. You engineers can tell me if it's dumb. Why not take the engine coolant, run it thru an exhaust heat exchanger (no exhaust restriction!) until it turns to steam. The steam drives a turbine and compressor (and possibly other accessories like A/C). Two thirds of the energy in gas is wasted in heat. Turbo's only recover part of it. I want more.
#37
Full Member

iTrader: (2)
Join Date: Feb 2002
Location: Gulfport MS
Posts: 144
Likes: 0
Received 0 Likes
on
0 Posts
I can see why you want around 350rwhp for a autocross/street driven FD. That was exactly how I felt about it, so I went single turbo: GT35R with a .82A/R exhaust, SMIC and getting 350rwhp on 15 psi. Spool up seems almost instant (good power in the 2000RPM range). I'm very impressed when comparing it to some of the supercharged cars I have driven. Setup was a little expensive but very reliable. PM me if you have any specific questions and I'd be glad to answer them. Jerry
#38
2/4 wheel cornering fiend

Good Lord, where to start?
I believe the term/statement I was referring to was "a restriction to power", not any restriction in general terms...
Not true. Besides the compressor efficiency dissertations given by neit_jnf and Shad Laws, even once the maximum boost level is reached, the drag imposed by the twin lobe shafts (and belt/pulleys) continues to build because you are working against that pressure.
No, it doesn't "have" to be mounted as close as possible to the intake tract, but if you want any sort of response and recovery efficiency-- especially at low rpms-- then yes, you do.
They are mounted that way because the design parameters of a Roots-type blower demand it for responsive performance, especially at low rpms/boost levels. If they're mounted that way because they don't need ICs with the low boost/hi compression, then why go through all the trouble of mounting it so close to the intake tract? Why not just mount it outside the engine, connect a manifold runner, and run a pulley off to the side and be done with it? Because the Roots-type blower uses the intake tract as its compression chamber, unlike screw and centrifugal SCs.
Hmm, and why is that? Again, because the Roots blower is using the intake tract for compression, so an IC is only condensing "part" of the intake charge.
Good for you, but how does that purpose-built OEM application apply to installing a custom unit on an FD?
If they "recirculate almost nothing", then why do their efficiency ratings drop like a rock at higher rpms? FYI, it's actually one of the reasons why bypass valves were developed...
I never said it was an absolute requirement, but nevertheless, much of this efficiency-- like a turbo-- is determined by the size and drive ratio of the SC, as well as overall final transmission gearing. If you have a blower that is small in size with low drive ratios, you can get improved gas mileage at cruise over a NA application, but your overall power increase will suffer. Fast forwarding to Rotary Resurrection's claim of improved fuel economy at cruise, if this were always the case, wouldn't all the manufacturers have produced cars with smaller SC-ed engines by now?
Right, and so does a turbo...
OK, sure, without getting defensive and resorting to BS flags and the like, in the grand scheme of semantics, I'll agree that power is being drawn from the exhaust to drive the turbo. However, that is energy that is normally wasted and is being "recycled"; the SC is drawing power directly from the engine that isn't.
The Paxton blower is a centrifugal type, which means it doesn't have to mounted as close, since-- like a turbo-- it has its own compression chamber.
Not sure what you meant by this...
Besides the explanations given by neit_jnf and Shad Laws, I recommend you examine a modern jet engine to see how it works...
Again, this is entirely dependent on the blower size/applicaton and drive ratio/pulleys. If they were more efficient and increased gas mileage at cruise, then why would the OEM manufacturers spend the R&D time and money to develop clutch drive pulleys?
I think this is my longest post ever...
Originally Posted by edmcguirk
I have to disagree with everything that Kento said.
Just because a turbo makes more power than it loses doesn't mean that it isn't a restriction. Have you ever heard of a turbo running lower pressure in the exhaust manifold than the intake manifold?
Just because a turbo makes more power than it loses doesn't mean that it isn't a restriction. Have you ever heard of a turbo running lower pressure in the exhaust manifold than the intake manifold?
Originally Posted by edmcguirk
A roots SC does not have increasing losses with RPM, it has increasing losses with higher boost.
Originally Posted by edmcguirk
A roots SC does not have to be mounted close to the engine. True, it does work a little better but only at low RPM.
Originally Posted by edmcguirk
The vast majority of bolt on roots SC are mounted close with no intercooler because they are mounted on high compression engines. The kits are limited to 5 PSI by the compression ratio. At that boost, they almost don't need intercoolers.
Originally Posted by edmcguirk
Roots SC's respond differently than turbos to intercoolers. An intercooled turbo keeps the same boost with more volume but an intercooled roots has lower boost with the same volume. Good for roots but not significant. Great for turbos.
Originally Posted by edmcguirk
My MR2SC came with roots SC and an intercooler running 8PSI stock which has been upgraded to 12PSI quite easily.
Originally Posted by edmcguirk
Oops, I won't disagree with this point. It's inaccurate but not completely wrong. (BTW, they recirculate almost nothing)
Originally Posted by edmcguirk
Street based roots SC do not require an electrical pulley clutch. OEM SC have them because it helps MPG slightly. A bypass valve is adequate but even that is not strictly necessary. A roots SC that makes a 2 litre engine equal to a 3 litre engine will be more efficient than a 3 litre engine even if it has no clutches, bypass valves, or even an intercooler. All those add-ons are there to try to get the boosted 2 Litre engine to be as efficient as a non-boosted 2 Litre engine.
Originally Posted by edmcguirk
A roots type SC draws less power than AC when you are making boost less than 1 PSI. It does draw a lot more when under full boost but we already know it produces more than it loses.
Originally Posted by RotaryResurrection
And then what, the turbo magically spins without any energy required or any restriction imposed? Bullshit...it takes the same amount of energy to spin the turbo regardless of intake manifold pressure. My above mentioned experiment takes boost out of the equation, to make it as simple as possible for people to understand. Put a turbine wheel and housing into the exhaust stream and you get a restriction throughout the powerband. Sure, hooking up the compressor to boost into the manifold makes more power...that doesnt mean that the turbo isn't requiring energy to operate, or posing a restriction to the exhaust still.
Originally Posted by RotaryResurrection
The paxton blower I bought for my denali leaves enough room to run FMIC piping if I wanted. It's not much more difficult than a turbo install, just all depends on location and pipe routing. OF course roots and screw blowers that are designed to bolt onto the actual intake would be much harder to plumb, but one of the FC guys has done this as well. https://www.rx7club.com/forum/showthread.php?t=495497
Originally Posted by RotaryResurrection
SO your intake manifold runs warmer than your exhaust huh?
Originally Posted by RotaryResurrection
I'll say it again. Air heats up the same amount when compressed at a given pressure level, regardless of the method used to compress.
Originally Posted by RotaryResurrection
The drag at low rpm on a blower is not unlike the restriction the turbo's turbine poses to the engine it is on. A blower makes the engine MORE EFFICIENT at any rpm because it is helping move air into the engine that it would otherwise have to work to SUCK IN on it's own. For this reason, superchargers usually INCREASE GAS MILEAGE at cruise.
I think this is my longest post ever...

#39
Senior Member

Join Date: Dec 2003
Location: Stanford, CA
Posts: 260
Likes: 0
Received 0 Likes
on
0 Posts
Hello-
Not dumb at all. It's a bit tricky to pull off, and certainly isn't exactly the weight-efficient way to go, but it can indeed increase overall efficiency (i.e. gas mileage).
In fact, just a few weeks ago, I read a few articles about a project that BMW is working on to do just that. They have turbines on the exhaust gases and on the coolant. I can't find the best link on it right now, but here's one of them:
http://www.motoring.co.za/index.php?fArticleId=3047964 Check it out.
Take care,
Shad
Originally Posted by mibad
Off topic, but let me just throw out a bizarre idea I've had since I was knee high to a married grasshopper. You engineers can tell me if it's dumb. Why not take the engine coolant, run it thru an exhaust heat exchanger (no exhaust restriction!) until it turns to steam. The steam drives a turbine and compressor (and possibly other accessories like A/C). Two thirds of the energy in gas is wasted in heat. Turbo's only recover part of it. I want more.
In fact, just a few weeks ago, I read a few articles about a project that BMW is working on to do just that. They have turbines on the exhaust gases and on the coolant. I can't find the best link on it right now, but here's one of them:
http://www.motoring.co.za/index.php?fArticleId=3047964 Check it out.
Take care,
Shad
#40
neit_jnf and Shad Laws, thanks for taking the time to post ACCURATE information.
mibad, that's an interesting idea. You'd be sitting at a stoplight sounding like a steam locomotive blowing off "boost." Probably difficult to implement and dangerous, but regardless, interesting. I think one of the main problems would be the large scale necessary to make this worth while and condensing the steam back into water quick enough. It'd basically be like a steam powerplant.
mibad, that's an interesting idea. You'd be sitting at a stoplight sounding like a steam locomotive blowing off "boost." Probably difficult to implement and dangerous, but regardless, interesting. I think one of the main problems would be the large scale necessary to make this worth while and condensing the steam back into water quick enough. It'd basically be like a steam powerplant.
#41
total newb

Join Date: Sep 2004
Location: Anacortes, WA
Posts: 76
Likes: 0
Received 0 Likes
on
0 Posts
neit_jnf and Shad Laws, a round of applause!
I think a big problem for this topic has been the misconception that a belt-driven supercharger is going to provide a more "usable", "better", or "linear" powerband than any turbocharger. Maximum Boost covers how to correctly size turbochargers for a given application and target use. - I'd suggest to anyone reading this who didn't quite grasp some of the things said by neit_jnf and Shad Laws to pick up copies of Maximum Boost and Supercharged by Corky Bell.
I think a big problem for this topic has been the misconception that a belt-driven supercharger is going to provide a more "usable", "better", or "linear" powerband than any turbocharger. Maximum Boost covers how to correctly size turbochargers for a given application and target use. - I'd suggest to anyone reading this who didn't quite grasp some of the things said by neit_jnf and Shad Laws to pick up copies of Maximum Boost and Supercharged by Corky Bell.
#42
Senior Member

Join Date: Dec 2003
Location: Stanford, CA
Posts: 260
Likes: 0
Received 0 Likes
on
0 Posts
Originally Posted by Kento
No, it doesn't "have" to be mounted as close as possible to the intake tract, but if you want any sort of response and recovery efficiency-- especially at low rpms-- then yes, you do.
Originally Posted by Kento
Why not just mount it outside the engine, connect a manifold runner, and run a pulley off to the side and be done with it? Because the Roots-type blower uses the intake tract as its compression chamber, unlike screw and centrifugal SCs.
Originally Posted by Kento
Hmm, and why is that? Again, because the Roots blower is using the intake tract for compression, so an IC is only condensing "part" of the intake charge.
Intercoolers condense ALL of the intake charge. This is true for turbos and superchargers alike... unless there is some very strange bypass system (which I've never seen on any application... it makes no sense and has no advantage).
Now, recall that positive displacement superchargers have a FIXED FLOW RATE at a given RPM. So, if you take a given setup and simply add an intercooler, the flow rate will not change. The volume of ambient air pushed through will be the same. Provided that the ambient temperature of this inlet air is the same, then the mass of air pushed through the blower is also the same. Period. Now, what happens to a fixed mass of air when we make it cooler, yet keep it's volume the same? Its pressure decreases.
Now, what about turbos? Again, keeping ALL other factors equal, the pressure should also decrease. The wastegate typically looks at the boost pressure right after the turbo itself, not after the intercooler. So, it has no idea what's happening downstream of the turbos... all it knows is what the pressure is that the turbos are putting out and it opens up a given amount for that pressure. However, when people usually do this, they also retweak their wastegate controls so the boost pressure is the same... it's much easier to do this than it is to change the belt ratio of a supercharger :-).
Take care,
Shad
#43
Senior Member

Join Date: Mar 2003
Location: new york city
Posts: 283
Likes: 0
Received 0 Likes
on
0 Posts
i know a supercharger dosent boost at idle im not dumb but it will create more preasure than a turbo will at low rpm. do you honestly think a supercharged rotary will last longer? i dont. if it was sooooo much better then it would have been done years ago and coppied a million times over already? come on now how long has this forum been around? plenty of people have thought about it. but its just not logical to change it when there is some much more potential with a turbo?
#44
Senior Member

Join Date: Dec 2003
Location: Stanford, CA
Posts: 260
Likes: 0
Received 0 Likes
on
0 Posts
Hmm... perhaps a little qualitative scorecard would help. Scale of 1-5 where 1 is good and 5 is bad:
Power at peak point:
1 - Turbo
3 - Twin screw blower
3 - Centrifugal blower
5 - Roots blower
Power throughout whole powerband:
1 - Turbo
3 - Twin screw blower
4 - Centrifugal blower
5 - Roots blower
Power at low rpm:
3 - Turbo
1 - Twin screw blower
5 - Centrifugal blower
1 - Roots blower
Transient lag:
5 - Turbo
1 - Twin screw blower
1 - Centrifugal blower
1 - Roots blower
Intake charge temperature increase:
1 - Turbo
1 - Twin screw blower
2 - Centrifugal blower (can't keep in efficient range for whole rpm band)
5 - Roots blower
These are just my own generalizations... there are likely some special cases that might make this ranking not exact. But, you get the idea :-).
Take care,
Shad
Power at peak point:
1 - Turbo
3 - Twin screw blower
3 - Centrifugal blower
5 - Roots blower
Power throughout whole powerband:
1 - Turbo
3 - Twin screw blower
4 - Centrifugal blower
5 - Roots blower
Power at low rpm:
3 - Turbo
1 - Twin screw blower
5 - Centrifugal blower
1 - Roots blower
Transient lag:
5 - Turbo
1 - Twin screw blower
1 - Centrifugal blower
1 - Roots blower
Intake charge temperature increase:
1 - Turbo
1 - Twin screw blower
2 - Centrifugal blower (can't keep in efficient range for whole rpm band)
5 - Roots blower
These are just my own generalizations... there are likely some special cases that might make this ranking not exact. But, you get the idea :-).
Take care,
Shad
#45
Newbie

iTrader: (9)
Join Date: Feb 2002
Location: MI
Posts: 1,171
Likes: 0
Received 0 Likes
on
0 Posts
wow there are a lot of falsities in this thread... all i'm going to say to the thread starter is that if you dont want a high HP application, and also a low rpm spool, just get a small turbo, you have to keep in mind that S/C's dont reach full boost RIGHT away, they just build it up a little faster, the turbo i have on my protege builds full boost at a really low rpm, because its really small, LOTS of auto-xer's use turbo's and are very succesful with them...
#46
It Just Feels Right

Originally Posted by Shad Laws
Hello-
Not dumb at all. It's a bit tricky to pull off, and certainly isn't exactly the weight-efficient way to go, but it can indeed increase overall efficiency (i.e. gas mileage).
In fact, just a few weeks ago, I read a few articles about a project that BMW is working on to do just that. They have turbines on the exhaust gases and on the coolant. I can't find the best link on it right now, but here's one of them:
http://www.motoring.co.za/index.php?fArticleId=3047964 Check it out.
Take care,
Shad
Not dumb at all. It's a bit tricky to pull off, and certainly isn't exactly the weight-efficient way to go, but it can indeed increase overall efficiency (i.e. gas mileage).
In fact, just a few weeks ago, I read a few articles about a project that BMW is working on to do just that. They have turbines on the exhaust gases and on the coolant. I can't find the best link on it right now, but here's one of them:
http://www.motoring.co.za/index.php?fArticleId=3047964 Check it out.
Take care,
Shad
This thread has been an education too.
#47
Senior Member
Join Date: Jul 2003
Location: Wayne, NJ 07470
Posts: 416
Likes: 0
Received 0 Likes
on
0 Posts
Originally Posted by Shad Laws
Hmm... perhaps a little qualitative scorecard would help. Scale of 1-5 where 1 is good and 5 is bad:
Power throughout whole powerband:
1 - Turbo
3 - Twin screw blower
4 - Centrifugal blower
5 - Roots blower
Power throughout whole powerband:
1 - Turbo
3 - Twin screw blower
4 - Centrifugal blower
5 - Roots blower
I don't know if I would agree with the turbo being a 1 for a broad powerband. Many turbo systems operating under 10 PSI can have a pretty broad powerband but above 10 PSI there begins to become a real trade off between top end and bottom end. Most of those turbo systems that have quick spool or acceptable boost below 2000 RPM are starting to run out of breath at the top end. And it only gets worse with more boost.
Just to reiterate my position:
There is no doubt that a turbo is more efficient.
A turbo is capable of more total HP.
but
For medium HP, a roots SC doesn't come in far behind and the advantage of a broader HP band and less thermal stress on an angine that already suffers from too much thermal stress makes it an interesting option for an FD.
Under 15 PSI I feel that there is not a huge advantage to either system. Efficiency and total power goes to the turbo while stress and broad power goes to the SC.
If I ever buy an FD, I will think long and hard about swapping an SC. If the turbo needed replacing, I would do it in a heartbeat.
If an SC wasn't illegal in my racing class, I would already have one on my FC.
ed
Last edited by edmcguirk; 01-04-06 at 04:37 PM.
#48
Senior Member

Join Date: Dec 2003
Location: Stanford, CA
Posts: 260
Likes: 0
Received 0 Likes
on
0 Posts
Hello-
I think we're defining things different ways :-).
What I meant by "power throughout the powerband" was the setup that is capable of making the largest amount of power throughout the engine's powerband. Most engines have a specific rpm range that is most useful for making power. For the stock FD, it's about 4500-7500rpm. It's no mistake that our gearing (and the sequential changeover) matches that :-). Although the stock FD can make full boost and almost full torque from 2500-4500rpm, I'd hardly call that the powerband.
I meant this rating in contrast to the "power at peak point" rating. This one is based ONLY on the amount of power robbed from the engine to produce boost at the most optimal point. Turbos win since they're efficient and some of their energy is for free. Twin screws and centrifugals are next since they're efficient but all of their energy is a loss. Roots is last.
To have maximum "power throughout the powerband," the setup needs not only to be efficient at it's optimal point, but also be able to operate pretty efficiently in rpm near that point. Twin screw, roots, and turbo setups are ALL capable of making the power feel "consistent" throughout the powerband. The only one that has a fault with consistency is the centrifugal supercharger, which is why it gets dinged in this rating.
It seems like you're trying to address the problem of a consistent torque throughout the whole rpm range, not just the powerband. In this case, I agree with you: turbos are going to lose to twin screw and roots superchargers. I thought I'd addressed this with my "power at low rpm" rating, although perhaps I wasn't very clear in making this known :-).
Hmm... hang on a sec... "too much thermal stress?" Perhaps we're confusing each other once again, but to me, this means that you want a setup that will keep the engine as cool as possible for a given power output level, right? Well, if that's the case, then roots superchargers are not you're friend. In fact, they're the worst of the bunch... for a given output level, they'll demand the most from the engine of any one setup AND blow out the hottest intake air. These induce as much thermal stress as possible of any of the four setups.
The roots has several disadvantages compared to a turbo. A much better comparison is a twin screw supercharger, which has approximately the same efficiency as a turbo. The turbo still has more power (and less "thermal stress" since it draws less from the engine), but the twin screw supercharger has the advantages of no lag and boost from zero rpm.
If you are building a track car, stick with the turbo. It will give you more power for the same amount of boost/thermal stress/etc. You don't need to make boost at low rpm since you should just about always be in the powerband (if not, then downshift! :-) ). And, you can deal with the lag by anticipating when you need the boost and giving it gas sooner.
If you are building a drag car, then you might consider the supercharger. The lag and lack of low rpm boost are harmful to your launch. For more power, just crank up the boost... you only need to make power for less than 15 seconds, anyway :-).
If you are building a street car, then it's a big toss-up. Although they don't make the car ultimately faster, having low rpm boost and no lag are nice things to have. One way to help even the tables is to install what's known as (get this!) a "sequential twin turbo" system. I think you FD folk *might* have heard of this before :-). It helps out with the lack of low rpm boost from a turbo quite a bit, making the advantage of a supercharger much less.
The problem with sequential turbo systems (besides complexity, cost, maintenance, etc.) has to do with the engine layout and lag. For the least amount of lag, and the most efficient turbocharging (i.e. most heat in exhaust), you want the exhaust manifold of a turbo system to be VERY short. In fact, if you could bolt the turbo directly onto the exhaust port you should :-). The rotary has a big advantage here: all of the exhaust ports are very close to one another. Inline-4 engines are also advantageous, and is one reason why Evo's can get away with so much boost without *that* much lag. Engines with two cylinder banks, such as the V6, V8, flat-6, etc., have a problem. If you want only one turbo, then you need a long exhaust manifold. Yuck. If you want twin sequential turbos, you still need that long manifold so that all of the exhaust can be directed into one turbo at low speeds... yuck again. But, if you go with twin parallel turbos, you can put one on each cylinder bank, each with their own very short exhaust manifolds. It's no mistake that this arrangement is so common, even on engines without much boost (such as the Audi V6 2.7 twin turbo in the S4, Allroad, etc.)
This, BTW, is why Porsche moved away from the sequential twin turbo system for their flat-6 engines after the 959. They realized that the sequential system induced quite a bit of lag since they had two very far apart cylinder banks to join together. By going to a parallel twin arrangement, they could make this problem disappear. Plus, hey, it was cheaper :-).
Take care,
Shad
Originally Posted by edmcguirk
From my experience with the MR2SC I would place the Roots just slightly behind the TwinScrew for broad powerband. I would rate it a 3.
I don't know if I would agree with the turbo being a 1 for a broad powerband. Many turbo systems operating under 10 PSI can have a pretty broad powerband but above 10 PSI there begins to become a real trade off between top end and bottom end. Most of those turbo systems that have quick spool or acceptable boost below 2000 RPM are starting to run out of breath at the top end. And it only gets worse with more boost.
I don't know if I would agree with the turbo being a 1 for a broad powerband. Many turbo systems operating under 10 PSI can have a pretty broad powerband but above 10 PSI there begins to become a real trade off between top end and bottom end. Most of those turbo systems that have quick spool or acceptable boost below 2000 RPM are starting to run out of breath at the top end. And it only gets worse with more boost.
What I meant by "power throughout the powerband" was the setup that is capable of making the largest amount of power throughout the engine's powerband. Most engines have a specific rpm range that is most useful for making power. For the stock FD, it's about 4500-7500rpm. It's no mistake that our gearing (and the sequential changeover) matches that :-). Although the stock FD can make full boost and almost full torque from 2500-4500rpm, I'd hardly call that the powerband.
I meant this rating in contrast to the "power at peak point" rating. This one is based ONLY on the amount of power robbed from the engine to produce boost at the most optimal point. Turbos win since they're efficient and some of their energy is for free. Twin screws and centrifugals are next since they're efficient but all of their energy is a loss. Roots is last.
To have maximum "power throughout the powerband," the setup needs not only to be efficient at it's optimal point, but also be able to operate pretty efficiently in rpm near that point. Twin screw, roots, and turbo setups are ALL capable of making the power feel "consistent" throughout the powerband. The only one that has a fault with consistency is the centrifugal supercharger, which is why it gets dinged in this rating.
It seems like you're trying to address the problem of a consistent torque throughout the whole rpm range, not just the powerband. In this case, I agree with you: turbos are going to lose to twin screw and roots superchargers. I thought I'd addressed this with my "power at low rpm" rating, although perhaps I wasn't very clear in making this known :-).
Originally Posted by edmcguirk
For medium HP, a roots SC doesn't come in far behind and the advantage of a broader HP band and less thermal stress on an angine that already suffers from too much thermal stress makes it an interesting option for an FD.
The roots has several disadvantages compared to a turbo. A much better comparison is a twin screw supercharger, which has approximately the same efficiency as a turbo. The turbo still has more power (and less "thermal stress" since it draws less from the engine), but the twin screw supercharger has the advantages of no lag and boost from zero rpm.
If you are building a track car, stick with the turbo. It will give you more power for the same amount of boost/thermal stress/etc. You don't need to make boost at low rpm since you should just about always be in the powerband (if not, then downshift! :-) ). And, you can deal with the lag by anticipating when you need the boost and giving it gas sooner.
If you are building a drag car, then you might consider the supercharger. The lag and lack of low rpm boost are harmful to your launch. For more power, just crank up the boost... you only need to make power for less than 15 seconds, anyway :-).
If you are building a street car, then it's a big toss-up. Although they don't make the car ultimately faster, having low rpm boost and no lag are nice things to have. One way to help even the tables is to install what's known as (get this!) a "sequential twin turbo" system. I think you FD folk *might* have heard of this before :-). It helps out with the lack of low rpm boost from a turbo quite a bit, making the advantage of a supercharger much less.
The problem with sequential turbo systems (besides complexity, cost, maintenance, etc.) has to do with the engine layout and lag. For the least amount of lag, and the most efficient turbocharging (i.e. most heat in exhaust), you want the exhaust manifold of a turbo system to be VERY short. In fact, if you could bolt the turbo directly onto the exhaust port you should :-). The rotary has a big advantage here: all of the exhaust ports are very close to one another. Inline-4 engines are also advantageous, and is one reason why Evo's can get away with so much boost without *that* much lag. Engines with two cylinder banks, such as the V6, V8, flat-6, etc., have a problem. If you want only one turbo, then you need a long exhaust manifold. Yuck. If you want twin sequential turbos, you still need that long manifold so that all of the exhaust can be directed into one turbo at low speeds... yuck again. But, if you go with twin parallel turbos, you can put one on each cylinder bank, each with their own very short exhaust manifolds. It's no mistake that this arrangement is so common, even on engines without much boost (such as the Audi V6 2.7 twin turbo in the S4, Allroad, etc.)
This, BTW, is why Porsche moved away from the sequential twin turbo system for their flat-6 engines after the 959. They realized that the sequential system induced quite a bit of lag since they had two very far apart cylinder banks to join together. By going to a parallel twin arrangement, they could make this problem disappear. Plus, hey, it was cheaper :-).
Take care,
Shad
#49
Senior Member
Join Date: Jul 2003
Location: Wayne, NJ 07470
Posts: 416
Likes: 0
Received 0 Likes
on
0 Posts
When I talk about "thermal stress" I am not talking about the heat of making HP. By that token, the more HP you make, the more thermal stress you have. Also, the more efficient the engine is, the lower the thermal stress is. (all around bad news for the roots)
I am talking about the heat that is forced back on the engine because the turbo is restricting free exhaust flow. The rotary engine is already a bit sensitive to heat, any help is appreciated. I feel that the heat at the exhaust port will be reduced and the heat in the engine bay will also be reduced. (not to mention that the loss of most of the solenoids and intake plumbing should allow better airflow around the engine)
A roots SC will produce hotter air because it is less efficient but a good intercooler can take care of that easily.
On the race track peak HP is most important. The rest doesn't really matter as long as you win the race (and your sponsor can afford a new engine). You should be able to adjust your gearset and driving style to keep even a centrifugal SC in the powerband.
I'm talking about the street where you can usually afford to give up maximum HP for driveability.
A twin screw is all around better than a roots but they are not generally available at reasonable prices. Good roots SC in the 300 HP range are available all day on ebay for $300.
The only real downside that I see is that I have no idea how horrible the MPG would be after a swap to a roots SC.
ed
I am talking about the heat that is forced back on the engine because the turbo is restricting free exhaust flow. The rotary engine is already a bit sensitive to heat, any help is appreciated. I feel that the heat at the exhaust port will be reduced and the heat in the engine bay will also be reduced. (not to mention that the loss of most of the solenoids and intake plumbing should allow better airflow around the engine)
A roots SC will produce hotter air because it is less efficient but a good intercooler can take care of that easily.
On the race track peak HP is most important. The rest doesn't really matter as long as you win the race (and your sponsor can afford a new engine). You should be able to adjust your gearset and driving style to keep even a centrifugal SC in the powerband.
I'm talking about the street where you can usually afford to give up maximum HP for driveability.
A twin screw is all around better than a roots but they are not generally available at reasonable prices. Good roots SC in the 300 HP range are available all day on ebay for $300.
The only real downside that I see is that I have no idea how horrible the MPG would be after a swap to a roots SC.
ed
#50
Full Member

Thread Starter
Join Date: Aug 2005
Location: York, PA
Posts: 79
Likes: 0
Received 0 Likes
on
0 Posts
If I would have known where this thread would end up I never would of started it!!!
I personally feel that a supercharger would just make everything much easier for my application, AUTO X. Thats why I like the acronym K.I.S.S Keep It Simple Stupid!!!! Here's just 2 reasons:
1. Cheaper-- I could use the stock fuel system on 12-14 psi of boost and most likely a stock ECU. If I need more boost, change a wheel. Going single would be more expensive because you have to buy a turbo setup, fuel management, intercooler setup, boost controller etc..
2. Simple-- Once its installed there is practically no maintenance, no selonoids to break, vacuum lines to crack, couplers to split. The intercooler is optional (Dual oil coolers would probably help just as much).
Easy! I like easy and realistically who really needs 450+ hp unless you drag
But if I would go single how does a Garret GT28 sound?? I hear it spools fast and you can easily get 15 psi out of it. Does anyone make this kit? I thought RX7store was doing it but haven't heard anything.
I personally feel that a supercharger would just make everything much easier for my application, AUTO X. Thats why I like the acronym K.I.S.S Keep It Simple Stupid!!!! Here's just 2 reasons:
1. Cheaper-- I could use the stock fuel system on 12-14 psi of boost and most likely a stock ECU. If I need more boost, change a wheel. Going single would be more expensive because you have to buy a turbo setup, fuel management, intercooler setup, boost controller etc..
2. Simple-- Once its installed there is practically no maintenance, no selonoids to break, vacuum lines to crack, couplers to split. The intercooler is optional (Dual oil coolers would probably help just as much).
Easy! I like easy and realistically who really needs 450+ hp unless you drag
But if I would go single how does a Garret GT28 sound?? I hear it spools fast and you can easily get 15 psi out of it. Does anyone make this kit? I thought RX7store was doing it but haven't heard anything.